What is Quality Assurance Plan? 9 Steps to Create a Great Plan
A quality assurance plan is more of a detailed document that outlines how a company will ensure the quality of its products or services. It includes all quality control procedures, policies, and standards that a company must follow to ensure that its products or services meet all customer requirements. Creating a quality assurance plan may seem daunting, but it doesn’t have to be. Following these 9 steps, you can create a great quality assurance plan to help your company meet all its quality goals.
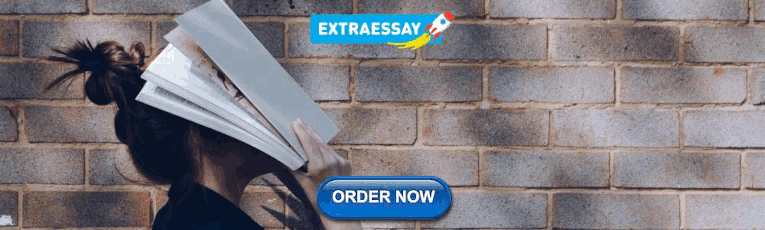
Defining Objectives And Goals
The first step in creating an efficient quality assurance plan is to define your objectives and goals. It will help you ascertain what to do to ensure that your products or services meet the required standards.
There are some significant things to review when defining objectives and goals:
- What are your customer’s needs and expectations?
- What are your company’s goals?
- What are the industry standards?
Once you have reviewed these factors, you can start setting objectives and goals. Make sure they are (SMART):
- Time-bound
9 Steps to Create a Great Quality Assurance Plan
Setting procedures and policies for all.
Setting procedures and policies for all is the first step in creating a quality assurance plan. By doing this, you will ensure that everyone involved in the project understands what is expected of them and how they should go about meeting those expectations.
There are various things to consider when setting procedures and policies, including:
- What standards will be used to assess quality?
- How will those standards be enforced?
- Who will be responsible for ensuring that quality standards are met?
- What processes will be implemented to check for compliance with quality standards?
- How will non-compliance be dealt with?
Once you have established procedures and policies for all aspects of the project, you can create specific quality assurance plans for individual tasks.
Schedule Roles And Responsibilities
When creating a quality assurance plan, scheduling roles and responsibilities is essential. It will ensure that everyone knows their part in the process and that tasks are properly completed. Here are some tips for scheduling roles and responsibilities:
- Define who will be responsible for each task.
- Delegate tasks based on skillset and experience.
- Set deadlines for each task.
- Hold regular meetings to check in on progress and cater to any issues.
By scheduling roles and responsibilities, you can create a quality assurance plan that will run smoothly and efficiently.
Documentation in Different Phases
Documentation is an integral part of quality assurance. It provides a record of what has been done and can be used to help track progress and identify areas for improvement. Documentation can be divided into different phases, each with its purpose.
The first phase of documentation is the planning phase. It is when the project manager creates a high-level plan for the project. The plan includes the overall objectives, scope, timeline, and budget. This phase also includes creating a quality assurance plan. The quality assurance plan outlines how the project will be monitored and controlled.
The second phase of documentation is the execution phase. This is when the actual work of the project is carried out. During this phase, documents are created that describe how the work was done and what was accomplished. These documents can help assess whether the project met its objectives and identify any areas for improvement.
The third phase of documentation is the monitoring and evaluation phase. It is when quality assurance activities are carried out to ensure that the project remains on track and meets its objectives. If problems are identified, they are documented, and corrective actions are taken to address them.
The fourth and final phase of documentation is the closure phase. This is when the project is completed, and all remaining work is documented. The closure report includes a summary of the project, an assessment of its success, and recommendations for future projects.
Also Read: How To Become A Better Project Manager? Top 10 Tips
Review And Audit
Reviewing and auditing in a quality assurance plan is a process of monitoring the quality of the products or services being delivered by a company. This can be done internally by employees or externally by independent third-party organizations. The purpose of reviewing and auditing is to ensure that the company meets its quality standards and delivers its products or services consistently and reliably.
There are many benefits to conducting reviews and audits as part of a quality assurance plan:
- It helps identify areas where the company may fall short of its quality standards. This information can be used to improve how the company operates.
- Review and audit results can provide valuable feedback to management about how well the company’s quality assurance plan is working.
- Regular reviews and audits can help build confidence among customers and other stakeholders in the company’s ability to deliver high-quality products or services.
Testing Phase
Testing helps ensure that products and systems are designed and built correctly and meet customer expectations. The testing phase in the quality assurance plan is verifying that a product or system meets the requirements specified in the design.
It also includes checking to see if the product or system works as expected and identifying any areas where it does not meet the requirements.
This allows businesses to make necessary improvements before release, which can save time and money in the long run. A well-executed testing phase can also help to boost customer confidence in a product or service.
Functional testing focuses on the specific features of your software and how well they work. For example, if you’re developing a web application, functional testing would involve:
- Testing things like login functionality.
- Adding items to a shopping cart.
- Checking out.
Non-functional testing assesses how well your software performs in terms of things like speed, scalability, and security. This type of testing is significant for web applications since they need to handle large amounts of traffic and data.
Troubleshooting Problems
There is no one-size-fits-all answer, as the troubleshooting process will vary depending on the specific quality assurance plan that you have in place. However, there are some general steps that you can take to troubleshoot any problems that may arise:
- First, identify the problem. This may seem obvious, but it’s essential to be specific when identifying the issue. What exactly is not working? What are the symptoms?
- Once you’ve identified the problem, try to reproduce it. This will help you narrow down the potential causes of the issue.
- Once you’ve reproduced the problem, start eliminating potential causes one by one. Check for common issues, such as incorrect configuration or data entry errors.
- If you’re still having trouble finding the root cause of the problem, consider enlisting the help of a more experienced colleague or consultant.
- Finally, document what went wrong and how you fixed it once you’ve found and resolved the issue. This information can be invaluable next time a similar problem arises.
Project Control
Project control in a quality assurance plan is the process of monitoring and regulating the progress of a project to ensure that it meets the requirements for quality. It involves setting up a system to track progress, identify issues and risks, and take corrective action as needed.
Project control helps to ensure that a project stays on track and meets its objectives. It can help identify potential problems early on, so they can be catered to before they cause significant delays or cost overruns. It also allows stakeholders to see the project’s progress and whether it is meeting their expectations.
When it comes to creating a quality assurance plan, training is one of the most critical steps. After all, if your team isn’t adequately trained on how to implement and follow the plan, it won’t be effective.
Two main types of training should be included in your quality assurance plan:
- Initial training – This is the training that should be provided to new employees or those who will be responsible for carrying out the quality assurance plan. It should cover the basics of the plan and how it should be implemented.
- Ongoing training – Once the initial training is complete, ongoing training should be provided on an as-needed basis. This could include refresher courses or more detailed training on specific aspects of the plan.
Risk Management
Risk management is a vital element of any quality assurance plan. By identifying and assessing risks early on, you can avoid potential problems down the road. Check out a few tips for creating an effective risk management plan:
- Identify all potential risks. It includes both external and internal risks. Consider all aspects of your business, from product development to marketing to financial stability.
- Assess the probability and impact of each risk. How likely is the risk that will occur? And if it does occur, how severe will the impact be?
- Create mitigation strategies for each risk. Once you’ve identified and assessed the risks, it’s time to develop mitigation strategies. This may include everything from changing your manufacturing process to increasing your marketing budget.
- Implement and monitor your risk management plan. Regularly monitor your plan to ensure it effectively reduces or eliminates risks. Make necessary adjustments as needed.
By following these steps, you can create an effective risk management plan to help keep your business on track to success.
Things To Remember While Creating A Quality Assurance Plan
When creating a quality assurance plan for your project, there are many aspects to consider. Keep these key points in mind:
1) Define your objectives and success criteria upfront. It will help you determine what needs to be included in your plan and how to measure success.
2) Create a detailed plan of action. Include who is responsible for each task, when it needs to be completed, and what the deliverables will be.
3) Ensure you have adequate resources to carry out the plan. This includes people, time, and budget.
4) Implement the plan and track progress. Regularly review results against your objectives and make adjustments as needed.
5) Be prepared to adapt. Things will inevitably change during your project, so be flexible and adjust your plans accordingly.
Also Read: Steps To Create A Successful Go-To-Market Strategy
Best Practices of a Quality Assurance Plan
The best practices of a quality assurance plan are necessary to follow to create a great plan. Four main best practices should be followed:
- Define the scope of the quality assurance plan.
- Identify who is responsible for each step of the quality assurance process.
- Develop measurable criteria for assessing whether quality objectives have been met.
- Establish a process for monitoring progress and taking corrective action as needed.
By following these best practices, you can be sure that your quality assurance plan will be effective and help you to achieve your desired results.
Why is Quality Assurance Plan Necessary For Every Business?
It is a document that outlines the processes and procedures that will be followed to ensure quality standards are met. It is an essential tool for any business, as it can help to improve customer satisfaction, reduce costs, and increase efficiency.
There are many benefits to having a quality assurance plan in place; below, we will explore five of them in more detail.
- Improved Customer Satisfaction
One of the essential advantages of having a quality assurance plan is that it can lead to improved customer satisfaction. Customers who receive products or services that meet their expectations are more likely to be satisfied with the purchase. This can lead to more business and positive word-of-mouth marketing for your company.
- Reduced Costs
Another benefit of implementing a quality assurance plan is that it can help to reduce costs associated with rework or product defects. By ensuring that products meet quality standards before they are released to customers, businesses can avoid the costly process of fixing issues after the fact. In some cases, this can also lead to reduced warranty claims.
- Increased Efficiency
Having a quality assurance plan can also help increase efficiency within your business operations. When everyone understands the procedures that need to be followed and there is a straightforward process for measuring quality, it becomes easier to streamline operations and eliminate wastefulness. This increased efficiency can save your company time and money in the long run.
- Greater competitiveness
In today’s marketplace, businesses need to be able to compete on quality as well as price. Having a quality assurance plan in place can demonstrate to potential customers that you are serious about providing high-quality products and services. It can provide you with a competitive edge and help you to win new business.
- Enhanced reputation
Finally, another benefit of having a quality assurance plan is that it can help to enhance your company’s reputation. When customers know that you have high standards for quality, they will be more likely to trust your brand. This increased trust can lead to more business and further opportunities down the line.
Quality assurance is a process that helps to ensure that products and services meet the requirements of customers or clients. By creating a quality assurance plan, businesses can develop specific goals and objectives to meet quality standards. By following these steps, you can be sure that your quality assurance plan will be comprehensive and effective in helping your business meet its quality goals.
To successfully manage operations, supply chains, and projects, it’s essential to understand how the quality assurance and control processes work. Our Advanced Certificate in Operations, Supply Chain and Project Management course can help you gain that knowledge.
This comprehensive course delves into operations management, inventory planning, supply chain optimization, project management principles, and quality assurance and control. It also includes exercises to help you apply the concepts in real-world scenarios.
More Information:
A Beginner’s Guide To Operations Management
Major Decision Areas In Supply Chain Management
How To Achieve Optimum Professional Growth
Brand Management v/s Product Management: Know Key Differences
Recommended videos for you
The agile way with pmi-acp®, path to pmp : cracking project integration management – i, itil foundation : master the art of implementing it service management, path to pmp- i, path to pmp : cracking project integration management – ii, itil : master the art of implementing it service management – ii, lean six sigma certification for starters, refresh and evaluate your readiness for pmp exam, a beginning to itsm, introduction to pmi-acp®, meaning of six sigma: the industry-independent methodology, the agile way with pmi-acp-i, itil csi: the age of continual service improvement, the agile way with pmi-acp – ii, the agile way with pmi-acp, path to pmp, introduction to pmp®, recommended blogs for you, scrum vs kanban: battle of the agile frameworks, an introduction to pmbok® guide, career progression with pmp® for non project managers, project time management – how to optimize project schedule, what is scrum everything you need to know about project management, itil® 4 tutorial for beginners – know how to get started with itil® 4, pmp® certification – become a certified project management professional, how to perform project integration management to ensure success, project management career path: bag top project management jobs with pmp® certification, all you need to know about prince2® exam levels, what are the project manager roles and responsibilities, project scope management – know how to manage project efficiently, career prospects with pmp® certification, supply chain management 101: all you need to know about escm, how to remove project clutter using konmari, project management processes and phases explained, 8 reasons to learn pmi-acp®, all you need to know about itil® 3 vs itil® 4, introduction to agile domain areas, what is agile project management a beginners guide, join the discussion cancel reply, trending courses in project management and methodologies, pmp certification training course.
- 72k Enrolled Learners
- Weekend/Weekday
PRINCE2® Foundation & Practitioner Ce ...
- 12k Enrolled Learners
Advanced Executive Certificate in Supply Chai ...
- 1k Enrolled Learners
Certified Scrum Master® (CSM) Certificati ...
- 5k Enrolled Learners
Six Sigma Green Belt Certification Training
- 4k Enrolled Learners
Executive Development Programme in General Ma ...
Microsoft® project 2013 training.
- 3k Enrolled Learners
PMI® Agile Certified Practitioner Trainin ...
- 8k Enrolled Learners
CSPO® Certification Training Course
Pmi-rmp® certification training course, browse categories, subscribe to our newsletter, and get personalized recommendations..
Already have an account? Sign in .
20,00,000 learners love us! Get personalised resources in your inbox.
At least 1 upper-case and 1 lower-case letter
Minimum 8 characters and Maximum 50 characters
We have recieved your contact details.
You will recieve an email from us shortly.

Researched by Consultants from Top-Tier Management Companies
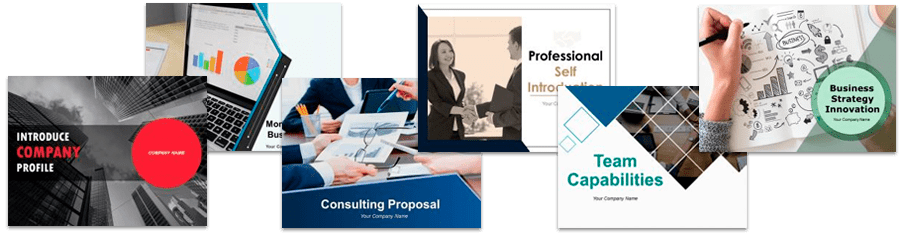
Powerpoint Templates
Icon Bundle
Kpi Dashboard
Professional
Business Plans
Swot Analysis
Gantt Chart
Business Proposal
Marketing Plan
Project Management
Business Case
Business Model
Cyber Security
Business PPT
Digital Marketing
Digital Transformation
Human Resources
Product Management
Artificial Intelligence
Company Profile
Acknowledgement PPT
PPT Presentation
Reports Brochures
One Page Pitch
Interview PPT
All Categories
Top 10 Quality Assurance Plan Templates with Samples and Examples

Sapna Singh

Toyota Motor Corporation, a Japanese multinational manufacturer, has built a global reputation for producing high-quality goods and services. The corporation follows the beliefs of Toyota Industries founder Sakichi Toyoda, who declared, " A product should never be sold until it has been carefully manufactured and thoroughly and satisfactorily tested. " The company’s dedication to maintaining and enhancing "quality" has led to customers, too, to associate its products with quality. No surprises then that rivals, worldwide, have imitated its manufacturing methods.
According to a Fortune study on quality of goods and services, Walt Disney, Intel, Apple, Singapore Airlines, and Procter & Gamble have been named among the "World's Most Admired Companies."
Dashboards are the ideal visual tools for providing a comprehensive picture of critical performance measures, allowing for informed decisions and strategic planning. Click here to view our Quality Dashboard Templates .
Quality enables companies to differentiate their product or service from competition. Continuously raising the quality of goods, services, and business procedures is a key objective for businesses hoping to thrive in the increasingly global marketplace. A Quality Assurance Plan (QAP) provides basic guidance, direction, and focus for tracking, evaluating, and reporting quality assurance (QA) operations in an organization.
Quality Assurance Plan: A systematic approach to maintain your business performance.
This proactive step to keep the quality of a product or service at a certain level is a competitive differentiator. Businesses use it to maintain their commitment to producing high-quality goods and services.
Discover SlideTeam’s Top 10 Quality Management Plan Templates as an excellent resource for businesses seeking to communicate their quality management plans.
This blog identifies and showcases methods for tracking compliance and maintaining consistent product management output throughout time, including planning, reviewing, monitoring, and reporting. This ensures that your quality assurance approach includes inspection and improvement of every stage of the manufacturing process. Use these Top 10 Quality Assurance Plan Templates for peak performance and dependability. These templates will help you self-assess and ensure that your work meets set criteria. The 100% customizable nature of the templates allows you to edit your presentations. The content-ready slides give you the much-needed structure.
Use SlideTeam’s top-notch PPT Templates to keep a business’s quality high.
Template 1: quality assurance plan analysis and management ppt.
Quality assurance in project management is a set of actions to improve project quality. Use this PowerPoint Template to define your project improvement plan. This 60-slide complete deck contains slides on quality control, customer focus, leadership, people involvement, process approach, system approach to management, continual improvement, decision making, beneficial supplier relations, dimensions of quality, service gap model, and quality determinants to help you in increasing business efficiency and improving customer satisfaction. Employ this presentation resource to enhance procedures to guarantee consistent quality standards. Download it now!

Download this template
Template 2: Project Quality Assurance and Control Plan PPT
Need to verify that process quality control techniques are used for quality measurement? Check out this PPT Deck to help you analyze your organization’s project control plan and procedures to ensure they deliver the expected results. This deck is an excellent tool for presenting a quality management plan for product assurance and control. Employ it to put quality standards in place and a management plan via control assurance activities and a checklist. It discusses multiple control activities, lists, quality assurance, logs, and an assurance issue reporting plan. This is meant to help you provide specifics about handling quality risks, reviews with the risk register, and project communication. Use this download to establish your project’s policies, processes, and goals for quality. Get it right away!

Template 3: Quality Assurance Plan and Procedures PPT Template
Quality control techniques are essential in project management to keep the quality of a product or service at a set level. This PPT Template provides a framework for a project control plan that includes structure, process, and outcome evaluations. This presentation helps the firm improve its product quality, brand reputation, and customer happiness with the deployment of quality control tools and techniques. These are affinity diagrams, box and whisker plots, cost of quality, customer experience, data gathering, and analysis tools. It also discusses decision matrix, Deming cycle, failure mode effect analysis, fishbone diagram, ISO 9001, Kano model, QMS, root cause analysis, Six Sigma tools, and TQM. Use this PowerPoint Presentation to prevent subpar product development by a thorough evaluation of services. Save it now!

Template 4: Quality Assurance Plan and Procedures PPT Presentation
Process quality control procedures are crucial for maintaining high product quality standards and long-term company performance. Use this PPT Template to provide hands-on support for the project management strategy. This deck includes quality control techniques, such as Gage Repeatability and Reproducibility (GR&R), force field analysis, Gantt chart, etc., to cover all aspects of the project. This slide is an excellent tool for developing a quality assurance plan focused on meeting requirements across the product management cycle. Get it now!

Template 5: Quality Assurance Plan and Procedures PPT Template
Here is another process quality control measure representing practical strategies and methods to conduct quality maintenance. Use this PowerPoint Presentation to create a sample project control plan to ensure acceptable project deliverables. This comprehensive deck comprises multiple quality control techniques and Quality Management System (QMS) features to monitor and evaluate the quality of project management. Employ this slide to manage areas of your product development and limit the possibility of errors during manufacturing. Get it now!

Template 6: Quality Assurance Plan for Project Management PPT
Project managers employ quality assurance plans to help businesses reduce risks and avoid blunders. Use this PPT Template to construct a project improvement mechanism to support teams in delivering results that satisfy the project’s requirements and expectations. This slide covers planning, quality assurance, and controlling, including setting quality standards, deciding needs, continual improvements, measuring quality, validating deliverables, and submitting change requests. This helps in the tracking of compliance and the maintenance of consistent project outcomes over time. Use this presentation to assess quality performance and ensure proper quality standards and procedures are followed throughout the project. Get it today!

Template 7: Organizations Project Quality Assurance Plan PPT
Need to carry out quality measurement and management actions to establish a measurable, manageable, and efficient project control plan? Use this PowerPoint Slide to develop a process quality control strategy for regular quality reviews to ensure the project meets the defined quality standards. The template explains creating a quality assurance plan and managing project quality. It addresses issues such as the objective, activity, indication, instrument, accountable person, measurement to be performed, status, and results. Use this presentation to define the standards, criteria, and procedures for guaranteeing the quality of a project’s outputs, processes, and outcomes. This will ensure that your consumers receive the greatest product possible. Grab it now!

Template 8: Steps to Develop Quality Assurance Project Plan PPT
This PPT Template illustrates the steps in creating a quality assurance project control plan. This is an excellent handbook for project quality monitoring and process control techniques in project management. It covers the creation of a Quality Assurance Project Plan (QAPP) team, determining your project’s goals and objectives, gathering background information, refining your project, designing your project’s sampling, analytical, and data requirements, developing an implementation plan, drafting your standard operating procedures sops and QAPP, revising your QAPP and submitting it for final approval, starting your monitoring project, and evaluating and refining your QAPP. Take into account all these steps of distribution or manufacture to ensure that there are no flaws. Use this resource to develop a robust quality assurance plan to support your company in meeting its objectives on quality. Grab it now!

Template 9: Continuous Improvement and Planning Model for Quality Assurance Framework
This continuous improvement and planning model for quality assurance framework is a multi-stage quality measurement system that provides businesses with improved and long-term results. This project quality assessment approach is divided into four stages: Plan, implement, monitor, and improve. The goal is to create a culture of high standards, continual improvement, and sharing best practices. Use this presentation to discover and prevent faults or inconsistencies, ensuring a high-quality final product or service. Get it now!

Template 10: Software Quality Assurance Test Plan
This PowerPoint Presentation provides a blueprint for quality control techniques to validate the program’s quality under test. This project management component helps track changes as the project progresses and stay current. This slide covers test planning, test-oriented software development management and working conditions, etc. This will allow you to establish a software testing process’s strategy, objectives, resources, and schedule. Use this template as a starting point for testing and coordinating operations within a QA team. Get it right away!

The systematic approach to track and address quality issues.
A quality assurance plan aids in the definition of quality standards, resources, processes, and quality control requirements. Use SlideTeam’s PPT Templates to improve traceability and assure compliance with internal and external standards.
PS Browse our pre-designed Test Plan Templates to choose the best course for testing a system or software application.
Related posts:
- Top 10 Project Management Best Practices for Foolproof Administration
- Top 5 Project Management Framework Templates with Samples and Examples
- [Updated 2023] 30 Best Gantt Chart PowerPoint Templates For an Effective Visualization of Your Project
- 50+ Project Management Templates That Will Make Your Next Project a Cakewalk
Liked this blog? Please recommend us

Top 7 Test Plan Templates with Samples and Examples

Top 10 Quality Management Plan Templates with Samples and Examples

Top 10 Quality Dashboard Templates with Samples and Examples
This form is protected by reCAPTCHA - the Google Privacy Policy and Terms of Service apply.
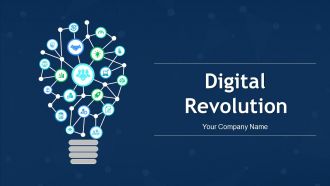
Digital revolution powerpoint presentation slides
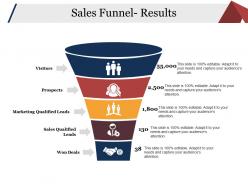
Sales funnel results presentation layouts
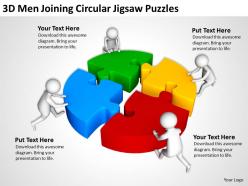
3d men joinning circular jigsaw puzzles ppt graphics icons
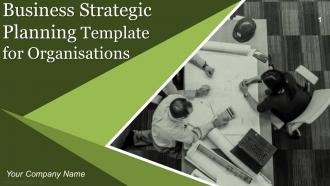
Business Strategic Planning Template For Organizations Powerpoint Presentation Slides
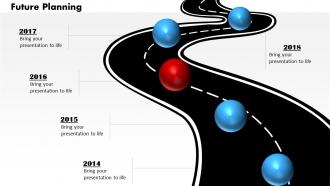
Future plan powerpoint template slide
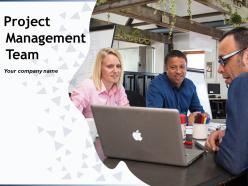
Project Management Team Powerpoint Presentation Slides
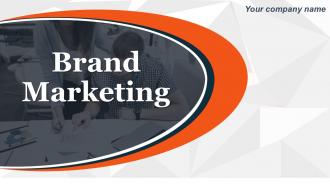
Brand marketing powerpoint presentation slides
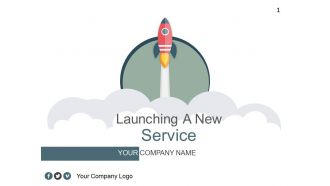
Launching a new service powerpoint presentation with slides go to market
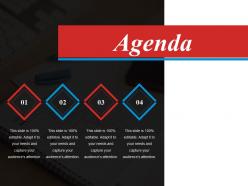
Agenda powerpoint slide show
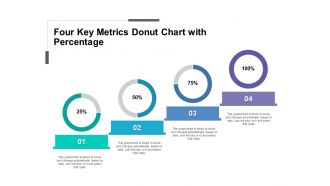
Four key metrics donut chart with percentage
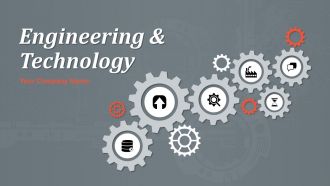
Engineering and technology ppt inspiration example introduction continuous process improvement
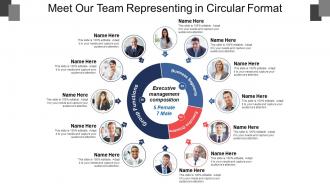
Meet our team representing in circular format

No search results found!!!
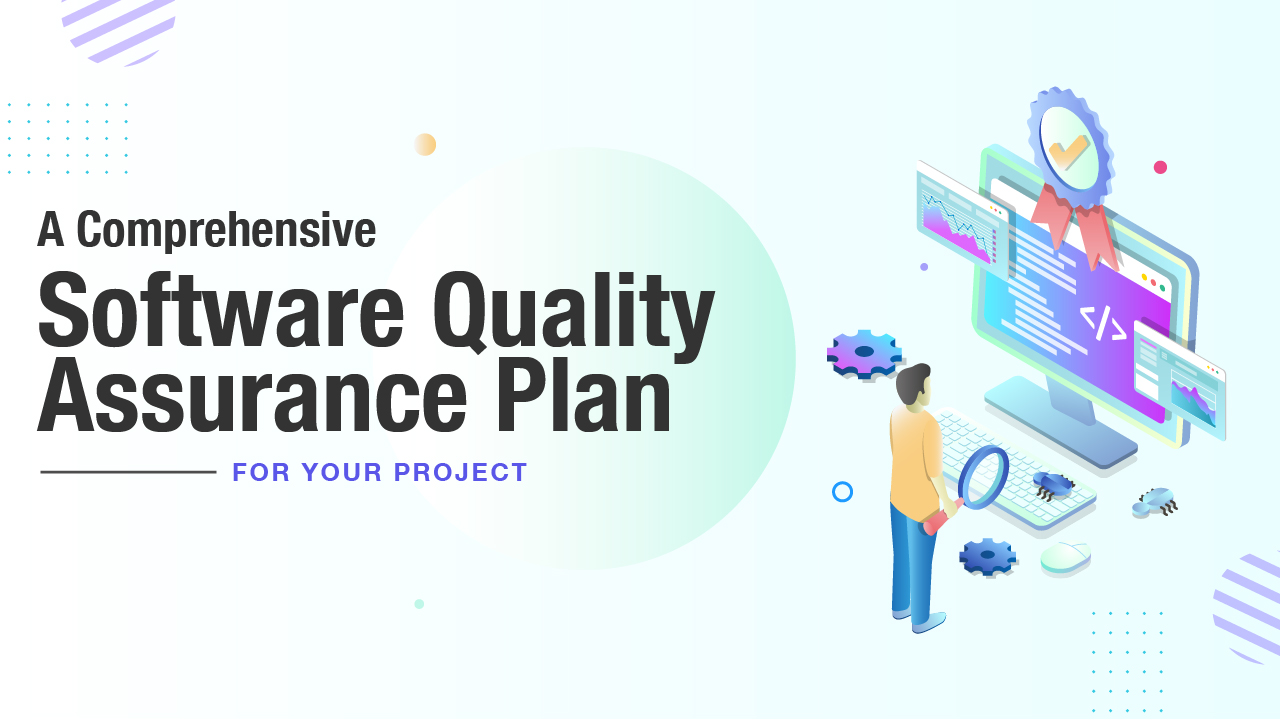
6 Key Steps to Creating A Quality Assurance Plan
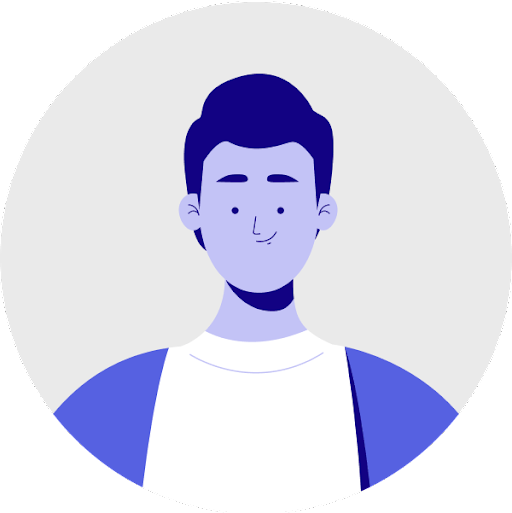
As a software developer or project manager, you know that ensuring the quality and reliability of your software is crucial to its success. But how do you create a solid Software Quality Assurance plan to help you achieve these goals?, this blog post will explore the critical elements of a successful SQA plan and provide tips and techniques for implementing it in your project.
We’ll cover topics such as setting clear objectives, defining your target audience, and choosing the right testing tools and techniques. Whether you’re just starting with SQA or looking to improve your existing processes, this post has something for you. So let’s get started!
Table Of Contents
- 1 What Is a Quality Assurance Plan?
- 2 Objectives And Goals of Quality Assurance Plan
- 3.1 Identify the role and responsibilities of the SQA team-
- 3.2 List of the work products the SQA auditor will review and audit-
- 3.3 Create the schedule to perform the SQA tasks-
- 3.4 Define the standards/methodology:
- 3.5 Review the process
- 4 Things To Remember While Creating A Quality Assurance Plan (Best Practices)
- 5 Why Is a Quality Assurance Plan Important for Software Companies?
- 6 Conclusion
- 7.1 What is the quality assurance plan process?
- 7.2 What are the components of a quality assurance plan?
- 7.3 Where is SQA used?
- 7.4 What is SQA software testing?
What Is a Quality Assurance Plan?
A Software Quality Assurance Plan is a managerial tool and a proactive measure to prevent defects and consumes less time. It is usually associated with two teams. It has auditing and reporting functions. It ensures that the software being developed meets the standard demand and works parallel to its development. Thus, it ensures that the result will meet the expectations of the customer/client or business. It is used for both small and big industry businesses.
The first team includes the Software engineers assigned to develop the product. The second team consists of the SQA team responsible for performing quality assurance planning, oversight, record keeping, and reporting.
Objectives And Goals of Quality Assurance Plan
Creating a fantastic quality assurance strategy is an exciting endeavor. But, before we get started, let’s define our objectives and aims to ensure we’re on the right track. Here are some critical considerations:
1. Customer requirements and expectations: Put yourself in the shoes of your customers and learn what they actually want from your products or services. This will direct you towards exceeding their expectations and providing complete fulfillment.
2. Company Objectives: Every company has its own set of goals and dreams. Determine your company’s goals and align your quality assurance approach accordingly. It’s like striking the proper balance between your goals and the path to accomplishment.
3. Industry Standards: Who wants to be left in the dust? Stay ahead of the competition by researching and comprehending industry standards. Knowing the benchmarks allows you to guarantee that your products or services meet or exceed the defined standards.
After we’ve completed our research, it’s time to set ship for the country of aims and goals. But keep in mind that we want to be SMART about it:
4. Specific: Identify the specific areas you wish to improve or concentrate on. Vague ideas will not suffice. Let’s go specific and focus on the target.
5. Measurable: Establish measurable criteria to track your progress. It’s similar to having a fitness tracker for your quality assurance strategy. Set milestones and metrics that will help you to measure your progress and celebrate your victories.
6. Achievable: Dreams are wonderful, but let us be practical, will we? Make certain that your aims and goals are attainable. It’s like attempting to climb a mountain that is difficult but not impossible. Remember that small steps lead to big leaps!
7. Relevant: Stick to the path that is consistent with your main purpose. Your objectives and goals should be pertinent to your company and the quality improvements you desire. It’s like selecting the best tool for the job—the ideal match that guarantees your efforts have meaning and impact.
8. Time-bound: Time does not wait for anybody, therefore let us set deadlines. Establish a timetable for achieving your objectives and ambitions. It’s like having a countdown clock that motivates you and keeps you on target.
Your quality assurance strategy will have a clear direction and a tactical roadmap if these objectives and goals are in sight.
Develop Quality Assurance Plan
Just like a test requires a test plan; similarly, an SQA requires a Quality Assurance plan before its implementation. The primary aim of devising an SQA plan is to ensure that the best quality is delivered to the end user.
The QA team should focus on the following aspects to prepare an SQA plan:
Identify the role and responsibilities of the SQA team-
- The SQA testing team plans the tests and works on possible scenarios, procedures, and scripts.
- The team is responsible for setting benchmark standards, procedures, and methods for software quality assurance testing and maintaining product quality.
- The team is assigned to report any defects in the software quality assurance activities using bug-tracking mechanisms.
- The team also identifies and analyses problems encountered in program functioning or output.
- It is also responsible for implementing audits and checks and works on follow-up.
- The team also conducts Training for process implementors.
List of the work products the SQA auditor will review and audit-
- The SQA auditor documents the risk management activities.
- An SQA auditor also prepares metrics reports and estimates the budget required.
- An SQA auditor is involved in planning and preparing the documents for a test.
- SQA auditors are responsible for the overall organization, human resource planning, and devising a training plan.
- SQA auditor is entrusted with monitoring and controlling the collected metrics.
- Another work product that an SQA auditor will review and audit is the report on issue management.
- An SQA auditor will also review and audit the test report documents.
Create the schedule to perform the SQA tasks-
The Test Manager should emphasize SQA activities and the work output for each job when they describe the functions for the SQA auditor to complete in this step. The project development timetable often determines the SQA schedule.
Define the standards/methodology:
There are specific methods that ought to be followed in the software quality assurance technique :
- Defining the policies and methods that are intended to avert defects that occur in the management process.
- Documenting and compiling the procedures and guidelines.
- Informing and training the staff to use the policies and guidelines.
Review the process
The entire SQA techniques should be reviewed periodically to ensure the guidelines and policy procedures are duly met. There are five significant reviews:
- Reviewing the project planning
- Reviewing the analysis done for software requirement
- Reviewing the test plan and test design
- Checking the entire process before the final release
- Reviewing the closing of the project.
Things To Remember While Creating A Quality Assurance Plan (Best Practices)
Alright, let’s continue our quality assurance journey and dive into the other important elements of a well-crafted plan. Here’s what we’ll be exploring:
Setting Procedures and Policies for All:
Establishing clear processes and regulations ensures everyone is aware of expectations and upholds quality standards, ensuring everyone follows the appropriate standards.
Schedule Roles and Responsibilities:
During the quality assurance process, team members will be aware of their roles and duties, akin to actors knowing their lines and cues.
Documentation in Different Phases:
Documenting our quality journey through project phases, similar to taking pictures, will help us develop, learn, and make adjustments, providing valuable resources for future initiatives.
Review and Audit:
Routine quality inspections assess and audit quality assurance initiatives to ensure they align with goals and are worthwhile. This process is similar to a strategy checkup to ensure soundness and functionality.
Testing Phase:
The action takes place here! To find any bugs or problems, we’ll put our goods and services through a thorough testing process. To make sure they are top-notch, it’s like taking our inventions for a test drive and pushing them to their limits.
Troubleshooting Problems:
Address obstacles head-on, examining underlying reasons, devising cures, and implementing them like sleuths to maintain proper functioning and address issues effectively.
Project Control:
Imagine yourself as the leader of our quality project, monitoring key performance indicators and making wise decisions to ensure we’re heading in the right direction.
Fund training initiatives to enhance team members’ abilities and expertise, fostering a high-quality culture and thriving in their professions. Provide necessary tools for success.
Risk Management:
Proactively identifying potential dangers and developing plans to reduce them serves as a safety net, ensuring quality issues are mitigated and preparing for outstanding achievements by controlling risks.
Why Is a Quality Assurance Plan Important for Software Companies?
A quality assurance plan is crucial for software companies due to the following reasons:
1. Assures product dependability through extensive testing and validation.
2. Keeps customers satisfied by providing high-quality items.
3. Reduces risks and expenses by detecting problems early on.
4. Ensures industry standards and laws are followed.
5. Encourages ongoing improvement and efficiency in development practices.
Overall, a quality assurance plan is vital for software companies to deliver reliable, high-quality products, maintain customer satisfaction, reduce risks and costs, comply with industry standards, and drive continuous improvement.
Any business, regardless of size, relies on Software quality assurance techniques and plans used by Software testers, Project managers, and Quality assurance professionals to produce successful and smooth deliveries without any defects.
Software Quality Assurance Plan is essential when fulfilling the promises made to the customers and clients. It must be noted that creating a schedule for the SQA task is the most critical step in implementing it as it assists in the time management and timely delivery of the software development project, which produces customer satisfaction and sustains the name of your business in the market.
Frequently Asked Questions:
What is the quality assurance plan process.
The quality assurance (QA) plan process involves developing and implementing a document that outlines the strategies and activities that will be used to ensure that a product or service meets certain standards of quality. The specific steps in the QA plan process can vary depending on the needs and goals of an organization. Still, a typical approach might include the following efforts: Define the plan’s scope, Identify the stakeholders, establish a testing strategy, Create test cases, review and report on test results, etc.
What are the components of a quality assurance plan?
The components of a QA plan can vary depending on an organization’s specific needs and goals. Still, some common elements include Quality objectives, Scope, Quality standards, Quality control processes, Quality assurance activities, Software Testing Strategies , Training and education, Quality metrics, and Continuous improvement. Read More on Quality Control VS Quality Assurance
Where is SQA used?
Software quality assurance (QA) is used throughout the software development life cycle (SDLC) to ensure that a software product meets specified requirements and is fit for its intended purpose. QA activities may involve verifying the software’s functionality, testing its performance and scalability, and checking for security vulnerabilities.
What is SQA software testing?
Software quality assurance (SQA) is the testing process of evaluating a software product or system to determine whether it meets the requirements and standards. QA testing aims to identify and fix the defects before they are released to the users.
Bala Subba Rao
Bala SubbaRao is a Digital Marketer, and a passionate writer, who is working with MindMajix, a top global online training provider. He also holds in-depth knowledge of IT and demanding technologies such as Business Intelligence, Salesforce, Cybersecurity, Software Testing, QA, Data analytics, Project Management and ERP tools, etc.
Like what you see?
Subscribe to get all our latest blogs, updates delivered directly to your inbox.
Test automation made easy
Start your smart continuous testing journey today with Testsigma.
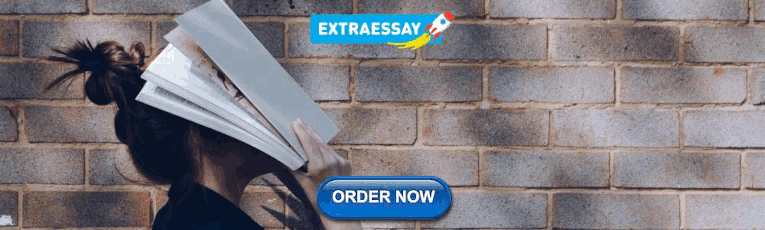
SHARE THIS BLOG
Related posts.
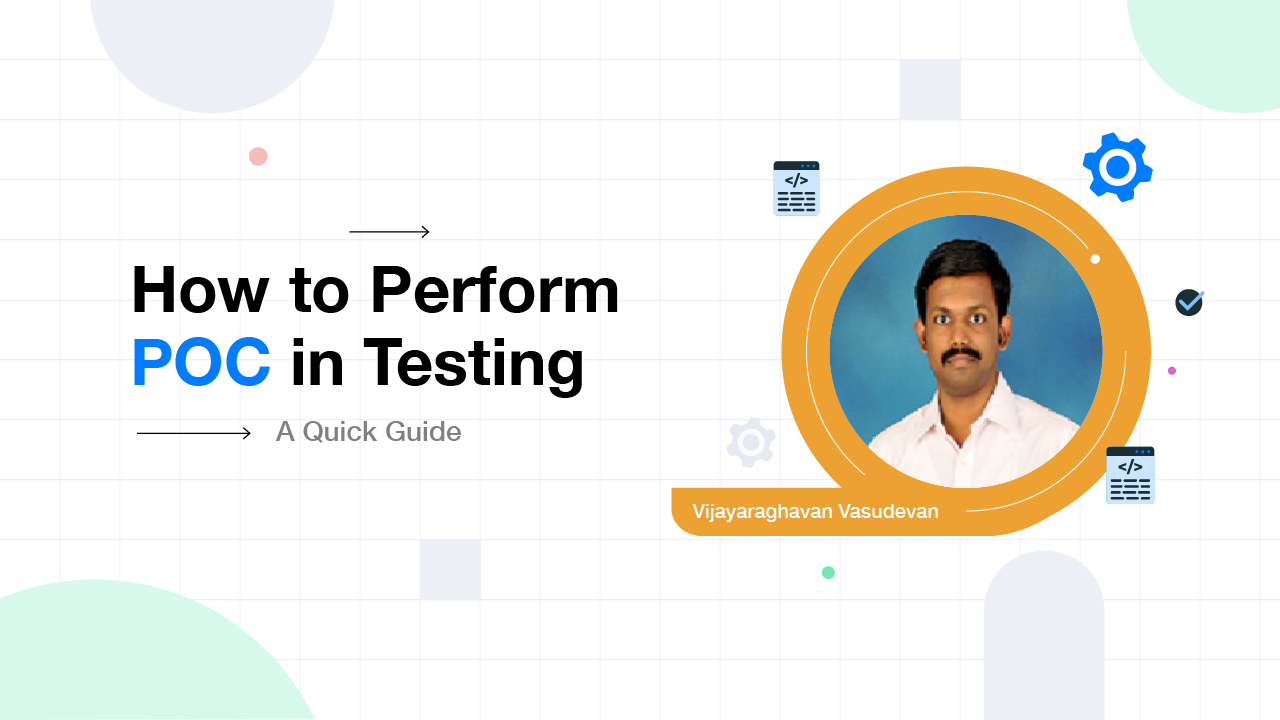
- Guidance on quality plans just updated

In order to effectively transform business ideas into actions, you need a plan. A quality plan. Guidance on how to create one has just been updated, providing a powerful tool to complement any quality management system, including ISO 9001.
Producing something – whether it be a product, service, process or project – always involves a series of interconnected or complementary processes and tasks that have to be performed, and planning them effectively in advance often leads to better results. A quality plan helps organizations do just that, as it includes a specification of the actions, responsibilities and associated resources that are needed to achieve the desired outcomes. It is useful as it describes how an organization will actually go about producing the product or service and how these actions can have an impact on other processes or parts of the business. It is a particularly useful tool for validating new products, services or processes before the work begins and for demonstrating to stakeholders how their requirements are going to be met.
ISO 10005:2018 , Quality management – Guidelines for quality plans, gives guidelines for establishing and applying quality plans, and it has just been updated to provide more guidance and more examples to be relevant to organizations of all shapes and sizes.
Roy Ackema, Convener of the working group that updated the standard, said that while it is not essential to have in place ISO 9001 , ISO’s flagship standard for quality management systems, in order to benefit from the guidance of ISO 10005, the two standards are based on many of the same concepts and principles, making them highly complementary to each other.
“ISO 10005 was updated to reflect modern business practices,” he said.
“This includes improvements to the terminology and concepts as described in the 2015 version of ISO 9001, such as those related to addressing the needs and expectations of relevant parties and managing organizational knowledge.”
“It also offers more guidance on how to apply risk-based thinking to decide the processes, resources and methods to be used.”
ISO 10005 was developed by working group 26 of ISO technical committee ISO/TC 176/SC 2, Quality systems , the secretariat of which is held jointly by BSI , ISO’s member for the UK and SAC , ISO’s member for China.
It can be purchased from your national ISO member , or the ISO Store .
Press contact
Journalist, blogger or editor?
Want to get the inside scoop on standards, or find out more about what we do? Get in touch with our team or check out our media kit .
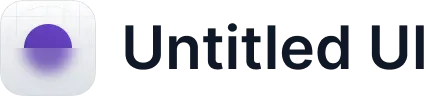
How To Create An Effective Annual Operating Plan (+Template)
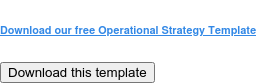
Do you even need one? Perhaps your organization excels at executing business strategies, keeping everything on track while you monitor performance in real-time.
That's the hope, isn't it?
But let's be honest. You wouldn't be here reading this article if you were confident in your existing annual operating planning process.
So let’s dive in and explore the step-by-step process to create your annual operating plan. This guide also includes a free planning template that will help you flesh out the plan’s details.

What Is An Annual Operating Plan?
An annual operating plan (AOP) is a forward-looking blueprint that translates your business strategy into actionable steps. It’s a detailed roadmap that outlines your organization's strategic objectives, annual budget, detailed action plans, and resource allocation for a specific fiscal year.
%20(1).png)
With an AOP (also known as the annual business plan), you get a 10,000-foot view of how to allocate project resources and what risks to manage so you can execute key priorities. The plan serves as a bridge between high-level business goals and day-to-day operations.
💡What is the difference between a business strategy and an annual operating plan (AOP)? Business strategy outlines the choices you need to make for your organization to win. AOP involves budget allocation, timelines, and deliverables, empowering your team to execute your strategy successfully.
Benefits Of An Annual Operating Plan
Organizations can realize the full benefits of an annual operating plan when it's tightly integrated with their strategic plan and financial budget. Here’s how:
Maximized resource efficiency and utilization
An AOP ensures efficient resource allocation to projects and initiatives that align with the business strategy and financial budget. It helps you direct human, financial, and other assets toward achieving strategic objectives , minimizing resource waste by linking daily operations with long-term goals.
Alignment and focus on key business priorities
An annual operating plan provides a clear roadmap toward a shared vision and helps everyone in your team understand their roles in meeting business objectives. It promotes collaboration and communication while eliminating silos, fostering a unified, goal-driven work environment.
Controlled strategy execution
By defining specific Key Performance Indicators (KPIs) and milestones in your AOP, you can easily assess whether the company is on track to achieve its goals. These metrics will help you identify areas that require immediate course correction to stay aligned with the overall strategy.
Confident, data-driven decisions
A well-rounded AOP provides you with data to help you make the right decisions. These insights empower proactive responses to opportunities and challenges, ensuring that all team actions are focused on outcomes.
How To Create An Annual Operating Plan?
Here’s a step-by-step guide for you to follow:
Step 1: Do the initial research and analysis
To kick off the planning process, assess the current state of your organization. Review the previous year's performance, considering various data sources, including financial statements and operational reports .
By doing a thorough business review , you ensure that your annual operating plan for next year is grounded in reality.
This helps you create a holistic plan that considers your business’s needs, strengths, and weaknesses. It also sets the stage for subsequent operational and financial planning —more on this later in the article.
👉How Cascade helps you:
With Cascade’s extensive library of 1,000+ integrations , you can centralize all your business data in one place. This simplifies data analysis and gives you easy access to past performance for an objective and thorough review.
Step 2: Consult with key stakeholders to understand the needs
The effectiveness of your annual operating plan (AOP) hinges on its alignment with your overarching company goals. Without it, you’re just creating a set of plans that, when executed, will have little to no impact on the overall business strategy.
To ensure organizational alignment , discuss with the CEO and CFO about key business priorities. Also, meet with other key stakeholders like department heads to gather insights on departmental needs and priorities.
Their input will help you set realistic and achievable objectives and also get them fully onboard when the time comes to put the plan in motion.
👉How Cascade helps you:
Cascade’s Metrics Library helps you tie metrics with your business objectives so you can have total visibility of what’s happening across the organization and achieve data-driven organizational alignment from top to bottom.
Step 3: Set a budget and allocate resources
First, look at your revenue goals and identify how much will you actually need to sell to hit your targets.
Collaborate with department heads to assess the availability of manpower, equipment, and other resources. Verify whether these are sufficient to meet your set targets.
List out expenses, covering everything from materials and labor to marketing and new equipment. This exercise provides a clear picture of how much of resources you’ll need to allocate across various projects and functions to fulfill the objectives of your annual plan.
👉How Cascade helps you:
Cascade makes budget tracking possible with custom fields that can capture data and link them to objectives. The budget custom field is a numerical field type where you can set the allocated, forecast, and spent values. As you work on your plan, you can update the relevant values and see a progress bar of the allocation vs. actuals.
📹 Check out this short video and learn how to set your custom field for budget tracking:
Step 4: Prepare a plan
In this step, you should define your metrics and go beyond mere measurement. Set concrete targets. Then, link these targets to initiatives , projects, and actions that will drive you toward those numbers.
Whether your organization operates with multiple departmental plans or a single, unified annual operating plan, ensure each department head outlines key projects and action plans aimed at achieving their annual targets.
When setting your KPIs to track progress, don’t forget to focus on both leading and lagging indicators .
Cascade’s free operational plan template gives you a clear and simple plan structure that you can use to easily collaborate with other department heads or team leaders. It’s pre-filled with examples and fully customizable to fit your needs.
📚 Are you an organization with multiple business units, each requiring its own AOP aligned with a central strategic plan? Explore our case study to see how a customer uses Cascade for strategic alignment between AOPs of different business units and the organization’s overarching 3-year strategy.
Step 5: Review and approve
Ensure your AOP is well-rounded and considers the needs of different stakeholders . Have different departments review the plan to promote alignment and collaboration. This step also ensures everyone is on the same page from the start.
After an internal review, secure approval from decision-makers, such as board members or executives, to gain buy-in at the highest levels. This buy-in makes it easier to implement your annual plan.
Step 6: Execute and monitor
Everyone involved must start working on their assigned initiatives. Ensure every team member knows that their duties are time-bound and remains accountable for completing them.
To make sure you're staying on course, it's vital to keep an eye on the progress through the KPIs established earlier. Monitoring progress against objectives ensures that you stay on track throughout the year.
💡 Tip: Set a regular schedule to review your annual operating plan. Depending on your needs, this could be weekly, monthly, quarterly, or semi-annually.
Cascade can help with monitoring through its user-friendly dashboards and comprehensive reporting capabilities.
Dashboards use chart widgets and graphs populated with real-time data so you can understand what’s happening in different time frames.
.jpg)
Cascade’s reports empower decision-making by providing the context of the data presented.
.png)
Annual Operating Plan Example With A Free Template
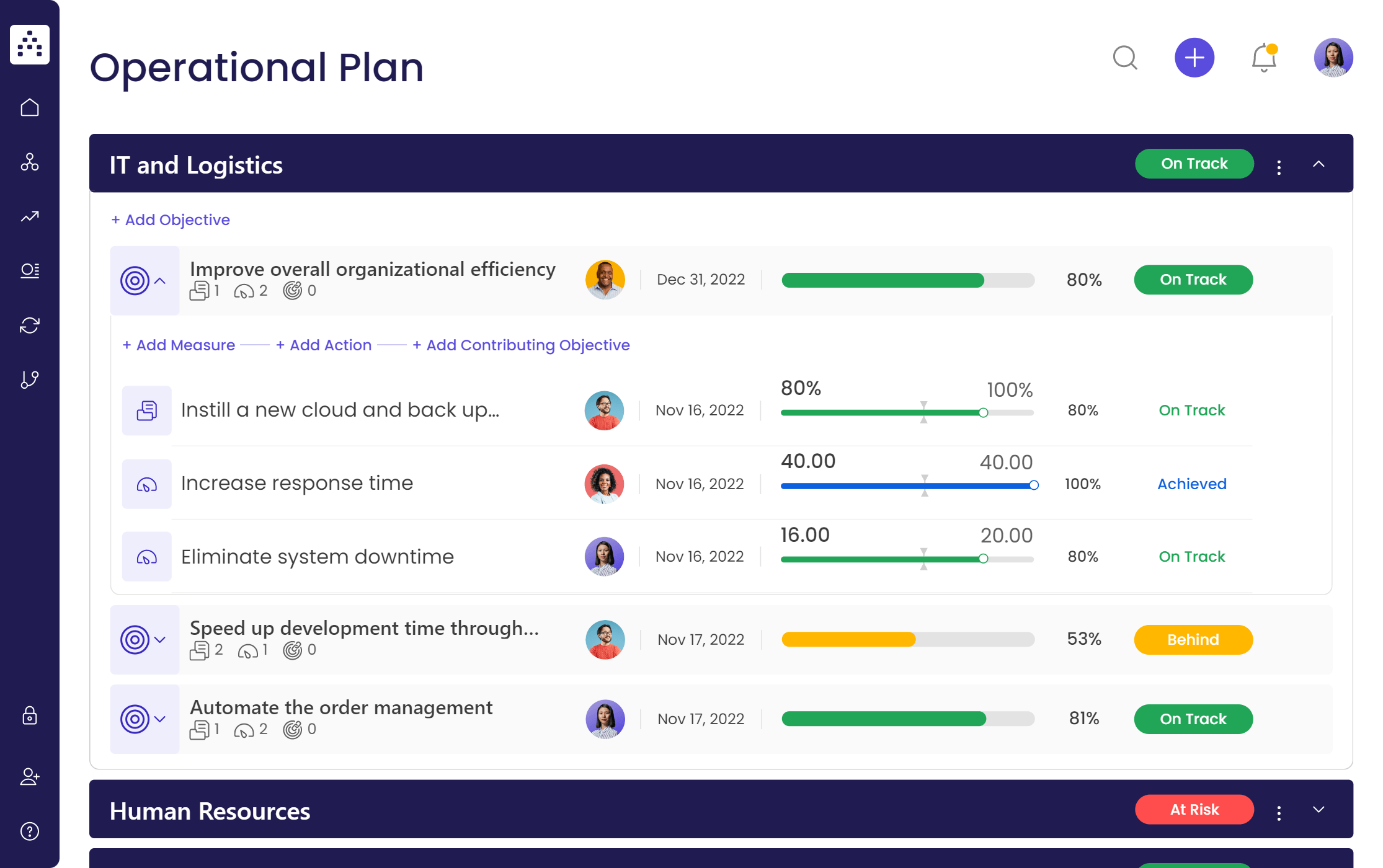
Cascade’s Operational Strategy Template is suitable for organizations of all sizes, and you can use it for free.
This template comes with pre-filled fields to guide you on where to enter your data so you can quickly set it up within minutes. You can choose your focus areas and write down the objectives. Then you can set the KPIs that will be measured and tracked as you progress with the plan.
Once set, designate responsible team members and use Cascade's real-time dashboard for monitoring.
It’s a tried and tested template that aligns your employees with the business strategy and provides clear guidelines on how to execute it.
Execute Your Annual Operating Plan With Cascade 🚀
You can’t simply make an AOP without tying it to the larger picture. Executing a plan without clear alignment to the overall business strategy is futile. Yes, your company is busy, but you’re getting nowhere.
With Cascade , you can centralize your strategy. By doing so, you can easily see how the execution aligns with your business strategy.
With its dynamic dashboards, real-time reports, and various other features, you can create seamless plans, execute them, and not worry that they’re being completed in silos. Every action your teams take, and every small goal they achieve, is connected to a bigger strategy that helps achieve your organization’s long-term vision.
Want to give it a try? Sign up today for free or book a 1:1 product tour with one of Cascade’s strategy experts.
Annual Operating Plan FAQ
What should be included in an annual operating plan .
A well-structured annual operating plan should include:
- A clear set of strategic objectives
- Detailed action plans
- Performance metrics
- Resource allocation
- Risk mitigation plans
What is the difference between annual operating plans and budgets?
Annual operating plans and budgets are both financial planning tools used to manage performance. An AOP is a comprehensive blueprint that includes your overarching goals and the details to execute them, including the financial and human resources needed.
On the other hand, CFOs use budgets to focus mostly on the financial aspect of the organization’s plan and are highly numbers-driven. They provide detailed projections of revenue, expenses, and cash flows but lack the strategic depth of AOPs. Unlike AOPs, they’re also less flexible once approved and are primarily intended for financial and accounting teams.
Popular articles
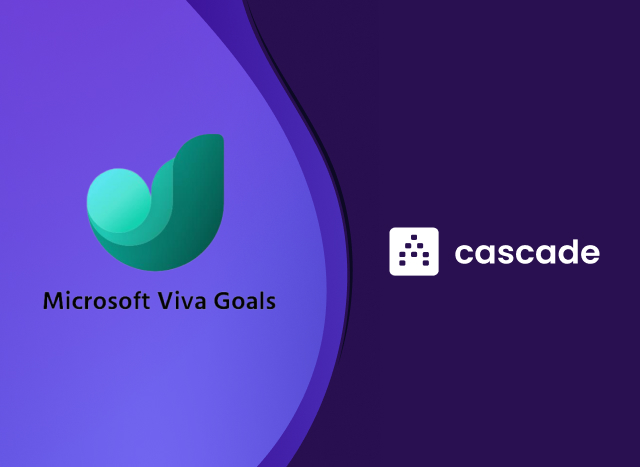
Viva Goals Vs. Cascade: Goal Management Vs. Strategy Execution
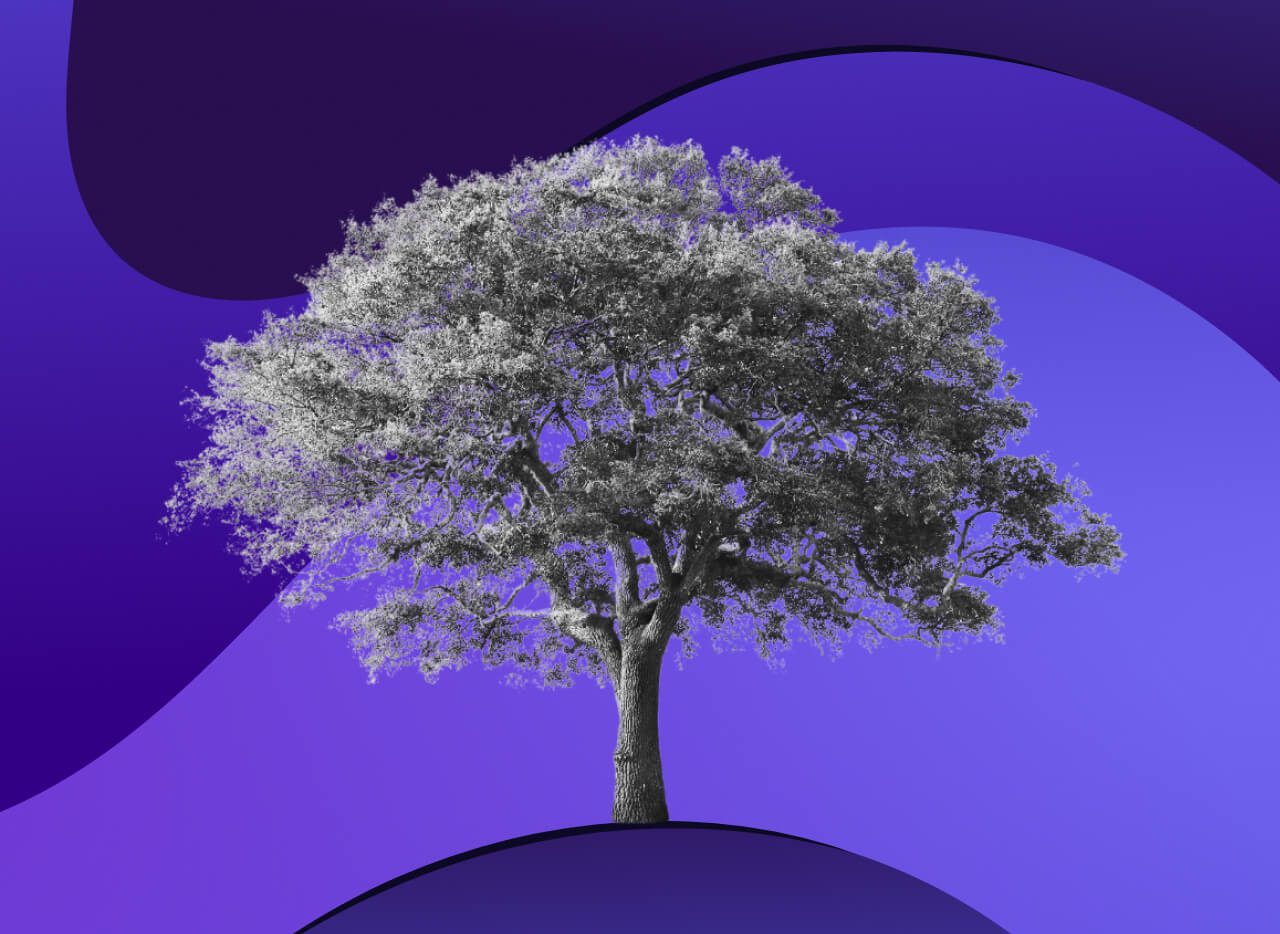
What Is A Maturity Model? Overview, Examples + Free Assessment
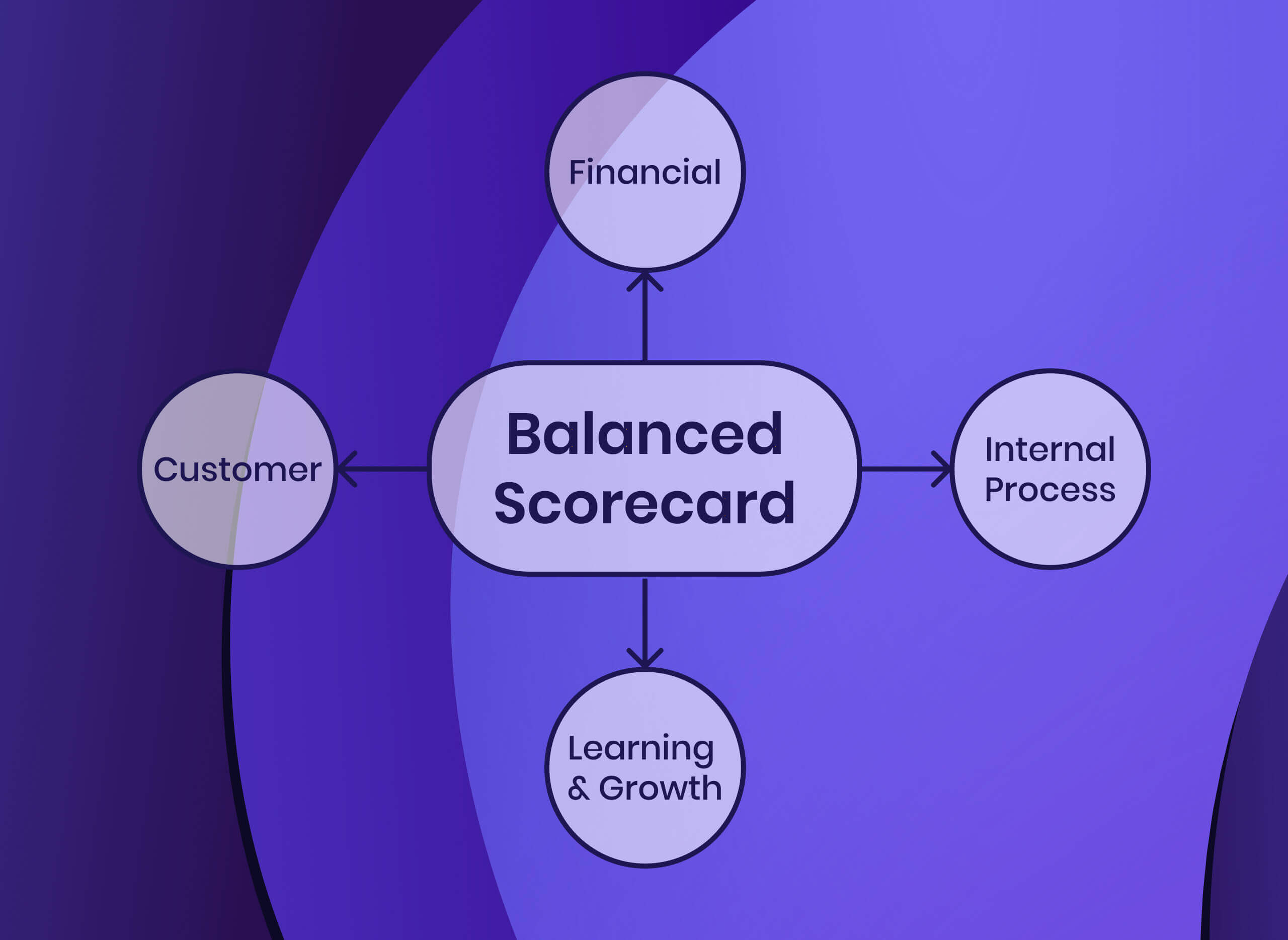
How To Implement The Balanced Scorecard Framework (With Examples)

The Best Management Reporting Software For Strategy Officers (2024 Guide)
Your toolkit for strategy success.

- Frontline Copilot™️
- Integrations
- Governance & Change Management
- Integrated Validation
- Data & Analytics
- Computer Vision
- Automations
- Edge Connectivity
- Machine Connectivity
- Edge Devices
- Machine Kit
- Device Library
- Composable MES
- Connected Worker
- Electronic History Records (eBR/eDHR)
- Visual Quality Inspection
- Digital Work Instructions
- Manufacturing Training Software
- Production Tracking Software
- Manufacturing Dashboards
- Order & Material Tracking
- Quality Management
- Compliance & Audits
- Machine Monitoring & Management
- Continuous Improvement
- Industrial Products
- Consumer Products
- Luxury Goods
- Electronics
- Automotive & Specialty Vehicle
- Aerospace & Defense
- Food & Beverage
- Pharmaceutical Manufacturing
- Biotech Manufacturing
- Cell & Gene Therapy
- Medical Devices & Diagnostics
- High-Mix Discrete Assembly
- Additive Manufacturing
- Batch and Hybrid Batch
- Contract Manufacturing
- New Product Introduction (NPI)
- Case Studies
- Augmented Ops Podcast
- Augmented Lean
- 30-Day Free Trial
- Tulip University
- Knowledge Base
- Attend Operations Calling 2024
- Tulip Experience Center
- Trust Center
- Website Terms of Use
- Privacy Policy
- Terms of Service
- Support Policy
- Acceptable Use Policy
Quality Assurance Plan – 5 Steps to Improve Production Quality
Jump to section
What is a Quality Assurance Plan?
Difference between quality assurance and quality control, benefits of a quality assurance plan, how to improve production quality, share on social.
- Share on Twitter
- Share on LinkedIn
Manufacturers need to ensure that they provide quality products to their end customers. Not only does this increase customer satisfaction, but it also enhances a manufacturing company’s reputation in their respective industry.
A defined quality assurance plan helps manufacturers bring this goal to fruition. A quality assurance plan sets out the standards, resources, and practices that personnel across the organization should use to ensure that the final product ticks all boxes spanning customer satisfaction and regulatory compliance.
However, in some instances, manufacturers might find that industry standards might not satisfy their business objectives due to complex manufacturing processes. Therefore, such manufacturers – for example, in the automotive industry – develop an advanced quality plan ( advanced product quality planning ) to ensure that they meet their superior quality standards.
Read on to learn how a quality assurance plan can help you improve production quality across your operations.
[Free Resource] Download our Ultimate Guide to Quality Management Systems →
Consistent quality is a sought-after factor in the vast majority of manufacturing operations. And with the advent of Industry 4.0, more quality requirements have sprung forth, necessitating manufacturers to develop more comprehensive quality management systems . As such, quality assurance plans have come to the fore.
A quality assurance plan is a document that highlights the standards a given manufactured product should adhere to. Furthermore, this plan also contains the practices that need to be executed to ensure that the product meets the set requirements.
Additionally, the quality assurance plan also outlines personnel responsible and the resources that will go into the manufacturing process so that the product never falls short of the standards set. Also, this plan sets out the quality control measures necessary to ensure that the product meets specifications.
In doing all this, the plan covers all aspects of production quality before an end-product is shipped and delivered to the customer.
Eliminate the source of quality defects with Tulip
View pending events, defect unit trends, defective Pareto chart, and pending actions in one centralized location.
Although sometimes used interchangeably, quality assurance (QA) and quality control (QC) are quite distinct . However, both of these are features of the broader quality management system.
Quality assurance tends to be used more broadly and begins defining quality standards even before the manufacturing process kicks off. In other words, QA is integrated into the entire process to predict and prevent defective items from being produced.
On the other hand, quality control later identifies if any defective products have come off the line. As such, QC is seen as a last line of defense, ensuring that unsatisfactory and nonconforming products don’t make it into the customers’ hands.
A quality assurance plan provides several benefits to manufacturing businesses.
These include:
Improved production efficiency : A quality assurance plan details the production process to ensure that all necessary standards are met. This includes identifying and preventing possible bottlenecks that may hamper production.
Additionally, a QA plan assigns responsibility to various individuals at different stages of production the production process. This ensures that all personnel know their specific duties and how to execute them.
Lower production costs: Because a QA plan examines the manufacturing processes even before production begins, it identifies areas of potential failure that can significantly impact manufacturing costs .
This allows the relevant personnel to execute preventive actions, ensuring that the line operates optimally when production kicks off.
Gaining and maintaining customer trust: Customers expect only the best when they purchase products from a business. Therefore, manufacturers need to ensure that their production processes provide customers with goods that meet their needs and exceed their expectations.
That’s where a well-thought-out quality assurance plan comes in. The program points out standards that products must adhere to before being put in the hands of customers. Consequently, manufacturers gain trust and repeat business from customers satisfied with their purchases.
Better work environment for employees: Quality assurance plans include employees in assessing the totality of a manufacturing operation. After all, operators are the ones actually doing the work and have direct input into the production processes.
As such, a QA plan insists on workers operating in ideal work conditions. The plan identifies potential work hazards and recommends relevant solutions. Consequently, satisfied employees are more motivated to execute their tasks, driving other quality assurance goals like efficient production and lower costs.
Compliance with regulations and standards: Manufacturers need to conform to various standards and regulations to compete favorably in the market. As discussed earlier, quality assurance plans allow businesses to comply with workplace and product safety regulations.
Furthermore, QA plans can outline industry standards governing the quality of raw materials used in product manufacturing. Using raw materials that meet these standards and specifications can be imperative for the business, allowing it to pass regulatory audits.
Manufacturers should consider the following steps to improve production quality.
Consider the customers’ needs: Quality assurance aims to prevent defects and other problems from cropping up in the production process. One way to ensure that the final product ticks all boxes is to incorporate the customer’s needs in the planning process.
With this in mind, manufacturers can design processes that ensure the customer gets exactly what they need.
Vet suppliers thoroughly: Even with top-notch production processes, a manufacturing business can struggle if it utilizes poor-quality raw materials.
As such, manufacturers need to extend their quality assurance plan to cover suppliers as well. It pays to conduct due diligence before taking on a supplier to ensure that they, too, comply with standards and regulations connected to the materials.
Develop a quality-centered culture: Because quality doesn’t start and end with the quality management department, it’s prudent for manufacturing businesses to involve all personnel in quality assurance efforts.
Therefore, top management should consult all departments to understand better how different areas can impact quality across the operations.
Continuous worker skill development: As quality standards evolve due to the constantly changing business environment, so do the skill requirements needed .
Consequently, manufacturers need to continuously upskill their employees so that the operation doesn’t lag when it comes to offering quality products.
Leveraging Quality 4.0: As the manufacturing landscape has changed due to Industry 4.0 , so has the level of quality management required. Industries like automotive manufacturing have embraced smart factories , with many crafting an advanced quality plan to take advantage of Quality 4.0 .
Connected devices collect data that is subjected to modern analytics to provide more comprehensive insights into quality management across the production cycle.
If you're interested in learning how Tulip can help improve your quality management practices, reach out to a member of our team today!
Streamline your quality management efforts with Tulip
Learn how leading manufacturers are using Tulip to capture real-time data, track production, and improve quality.

An official website of the United States government
Here's how you know
Official websites use .gov A .gov website belongs to an official government organization in the United States.
Secure .gov websites use HTTPS A lock ( ) or https:// means you’ve safely connected to the .gov website. Share sensitive information only on official, secure websites.
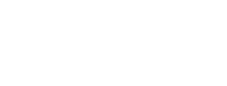
- Digg
Latest Earthquakes | Chat Share Social Media
Quality Assurance Plans: Recommended Practices and Examples
Yes, you can plan ahead for high-quality data! A Quality Assurance Plan (QAP) is used to define the criteria and processes that will ensure and verify that data meet specific data-quality objectives throughout the Data Lifecycle.
<< Back to Manage Quality
Quality Assurance Plans: Recommended Practices
With a focus on quality goals, criteria, assessment, and validation methods, a QAP covers the full data lifecycle, from Acquisition through Publication, and can:
- Identify data quality objectives for your data or project
- Staff skills and training
- Field and lab methods and equipment that meet data-collection standards
- Software and file types to use for data handling and analysis that support data quality goals
- Data standards, structure, and domains consistent with community conventions for other data in the same subject area
- Periodic data-quality assessment using defined quality metrics
- Describe a structure for data storage that can also facilitate checking for errors and help to document data quality
- Describe approved data entry tools and procedures, when applicable
- Establish data-quality criteria and data-screening processes for all of the data you will collect
- Include quality metrics that can determine current data-quality status
- Establish a plan for 'data quality assessments' as part of the data flow
- Contain a process for handling data corrections
- Contain a process for data users to dispute and correct data
Quality Assurance Plans: Examples
USGS Examples
- USGS Quality Assurance Plan for Digital Aerial Imagery (PDF)
- U.S. Geological Survey quality-assurance plan for surface-water activities in Kansas, 2015
- Quality-assurance plan for the analysis of fluvial sediment by the U.S. Geological Survey Kentucky Water Science Center Sediment Laboratory
- USGS National Water Quality Laboratory: NWQL Quality Links, including Quality Assurance Plan
Other Agency Examples
- National Atmospheric Deposition Program (NADP): Quality Assurance Plans
- U.S. EPA Guidance on preparing a QA Project Plan
This website uses cookies. to enhance your browsing experience, serve personalized ads or content, and analyze our traffic. By clicking “Accept & Close”, you consent to our use of cookies. Read our Privacy Policy to learn more.
Quality: Keys to Your Quality Program’s Annual Review
By: Jeanine Watson, MSN, RN, CNOR(E), CASC
Published: 11/21/2023
Tips to help time-strapped administrators with a critical task.
W here has this year gone? As our lives get increasingly hectic with all the excitement and stress of the holidays, don’t forget to wrap up your quality plan. Although it’s a bit late to start a full quality program, it’s a great time for a quick review.
Preventing gaps
ASC leaders know the quality plan encompasses nearly everything that takes place in the facility and should be accurately monitored and documented, including continued improvements. The end of the year can be challenging for ASC leaders to meet the increased volume demands, requests for time off and winter illnesses impacting patients and staff alike. It is easy to overlook an annual requirement, so take a quick look before it is too late.
Ensuring that your surgery center consistently complies with its quality plan is not just a regulatory requirement; it’s a commitment to providing the highest standard of care to your patients. Here are a few tips for reviewing the effectiveness of your quality plan and avoiding gaps in activities or reporting.
Quality plan purpose
The purpose of the Quality Assurance and Performance Improvement (QAPI) plan is to create an environment where safety is prioritized and high-quality healthcare services are provided in accordance with the principles of professional practice and ethical conduct. It must include, but not be limited to, an ongoing program that measures, analyzes, and tracks quality indicators, adverse patient events, infection control and other aspects of performance that include care and services furnished in the ASC.
Authority and responsibility
The Governing Body is ultimately responsible and accountable for the quality of care provided, risk management and performance improvement in the organization. The list below provides a sample overview of the annual requirements of the Governing Body. Evidence of completion should be documented in Governing Body meeting minutes. Designate committees and/or individuals responsible for development, implementation and oversight of the QAPI program.
- Receive, review and approve written reports of quality data and outcomes.
- Receive, review and approve performance improvement activities and results of action plans.
- Receive, review and approve the facility policies and procedures.
- Receive, review and approve the annual review of the effectiveness of the QAPI Plan.
- Receive, review and approve all credentialing and privileging activities during the year.
Goals and objectives
A successful QAPI plan should focus on high-risk, high volume and problem-prone areas. Consider how often and how severe problems in those areas occur and how they affect health outcomes, patient safety and quality of care. The plan should specify the number and scope of distinct improvement projects conducted annually that reflects the scope and complexity of the ASC’s services and operations. It should also note how strategies to prevent adverse events were implemented in ways that ensured all staff were familiar with them.
Data collection
The organization should consistently gather information on the quality of care from the following sources: medical record reviews; SSI/complication physician reports; peer review results; patient satisfaction surveys; results of postoperative phone calls; patient complaints; verbal reports from employees, patients, visitors or physicians; variance reports; pharmacy audits and reviews; incident reports forwarded to risk management officials; financial audits; and results of environment of care rounds.
Performance improvement activities
Facilities must track adverse patient events, examine their causes, implement and ensure that improvements are sustained over time. The performance improvement projects should be conducted throughout the year, align with the goals and objectives of the quality plan, and the results should be evaluated and reported throughout the organization.
The documentation of projects, which must include project type, reason for implementation and results, should be conducted throughout the year.
Annual review
Assessing your QAPI each year is an important step to closing the loop on regulatory and accreditation requirements and a good way to enhance the overall quality of care provided at your facility. Your annual review should determine whether goals and objectives were achieved and provide a thorough review of data collection reports and performance improvement activities and their results. This process should identify opportunities for the following year’s quality plan, which should be included when the review is shared with leadership and employees.
ASC administrators and leaders should consider the annual quality review a well-spent investment of their time. Although it’s a requirement, it’s also an opportunity to reflect on the care provided and whether steps to improve things were successful. In my experience, it is much easier to plan the quality activities and reporting for the entire year and divide them into four quarters. At the end of the year, you can combine the activities of the four quarters to create the annual review. If you need guidance developing and reviewing your ASC Quality Plan, AORN’s ASC Academy: A Guide to Quality and Risk Assessment Management can help you navigate this regulatory requirement. Learn more about AORN Ambulatory Solutions at aorn.org/asc . OSM
Related Articles
How do you handle change.
It takes a concerted effort to not only recognize the need for change in your workplace culture, but also to do something about it....
Keep Connections With Colleagues on Your Radar
Spring is the season for conferences and live events, which can go a very long way toward revitalizing your outlook....
FDA Recommends U.S. Healthcare Facilities Stop Using Plastic Syringes from two Chinese Manufacturers
The U.S. Food and Drug Administration (FDA) announced this week that its ongoing investigation of plastic syringes for potential failures has found that the use of...
Partner With Us!
Connect with 100,000+ outpatient OR leaders through print and digital advertising, custom programs, e-newsletters, event sponsorship, and more!
AORN Enterprise
Quick links.
- Contact sales
Start free trial
Operational Planning: How to Make an Operations Plan

The operations of your business can be defined as the sum of all the daily activities that you and your team execute to create products or services and engage with your customers, among other critical business functions. While organizing these moving parts might sound difficult, it can be easily done by writing a business operational plan. But before we learn how to make one, let’s first understand what’s the relationship between strategic and operational planning.
Operational Planning vs. Strategic Planning
Operational planning and strategic planning are complementary to each other. This is because strategic plans define the business strategy and the long-term goals for your organization, while operational plans define the steps required to achieve them.
What Is a Strategic Plan?
A strategic plan is a business document that describes the business goals of a company as well as the high-level actions that will be taken to achieve them over a time period of 1-3 years.
What Is an Operational Plan?
Operational plans map the daily, weekly or monthly business operations that’ll be executed by the department to complete the goals you’ve previously defined in your strategic plan. Operational plans go deeper into explaining your business operations as they explain roles and responsibilities, timelines and the scope of work.
Operational plans work best when an entire department buys in, assigning due dates for tasks, measuring goals for success, reporting on issues and collaborating effectively. They work even better when there’s a platform like ProjectManager , which facilitates communication across departments to ensure that the machine is running smoothly as each team reaches its benchmark. Get started with ProjectManager for free today.
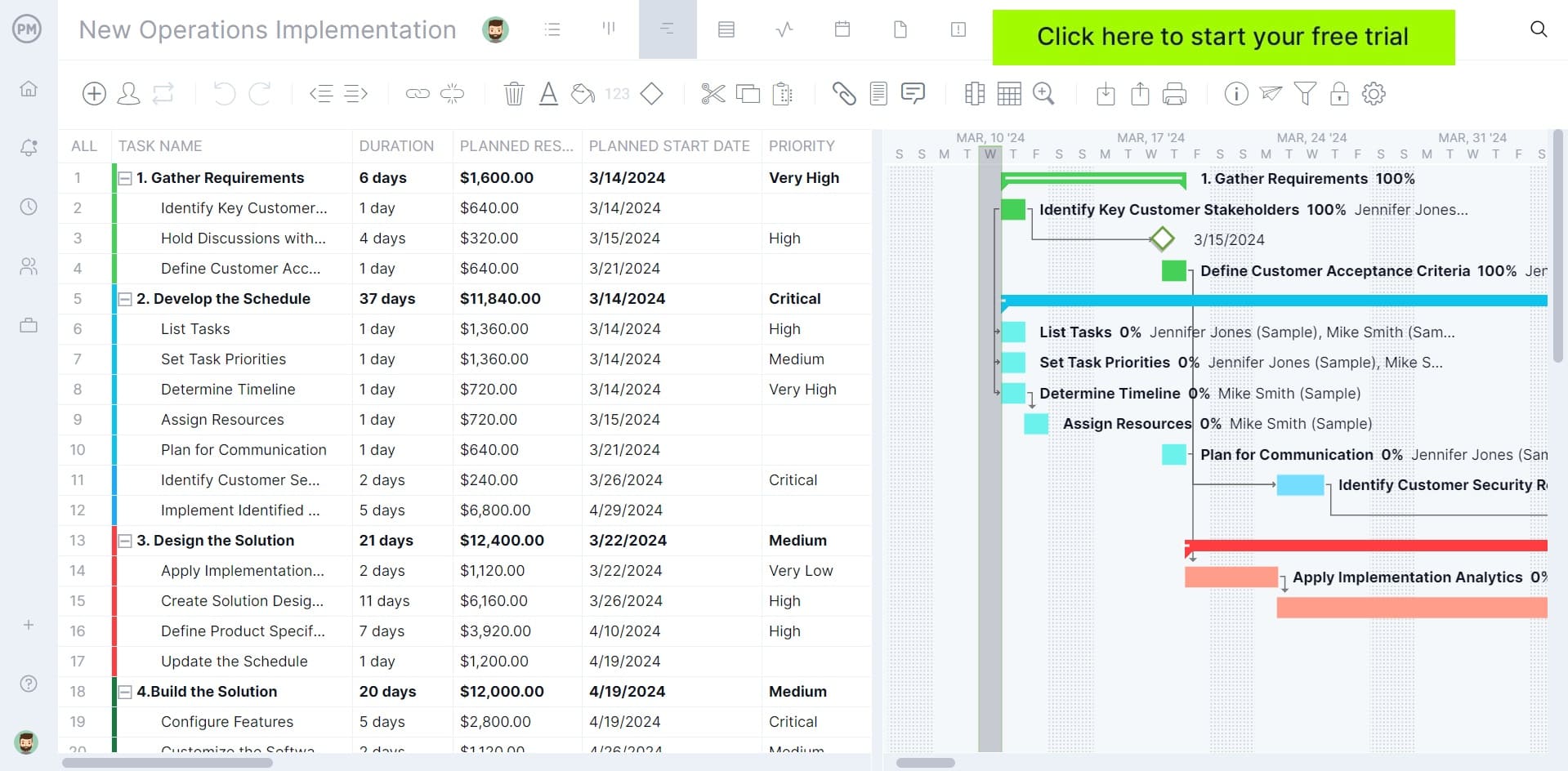
What Is Operational Planning?
Operational planning is the process of turning strategic plans into action plans, which simply means breaking down high-level strategic goals and activities into smaller, actionable steps. The main goal of operational planning is to coordinate different departments and layers of management to ensure the whole organization works towards the same objective, which is achieving the goals set forth in the strategic plan .
How to Make an Operational Plan
There’s no single approach to follow when making an operation plan for your business. However, there’s one golden rule in operations management : your strategic and operational plans must be aligned. Based on that principle, here are seven steps to make an operational plan.
- Map business processes and workflows: What steps need to be taken at the operations level to accomplish long-term strategic goals?
- Set operational-level goals: Describe what operational-level goals contribute to the achievement of larger strategic goals.
- Determine the operational timeline: Is there any time frame for the achievement of the operational plan?
- Define your resource requirements: Estimate what resources are needed for the execution of the operational plan.
- Estimate the operational budget: Based on your resource requirements, estimate costs and define an operational budget.
- Set a hiring plan: Are there any skills gaps that need to be filled in your organization?
- Set key performance indicators: Define metrics and performance tracking procedures to measure your team’s performance.
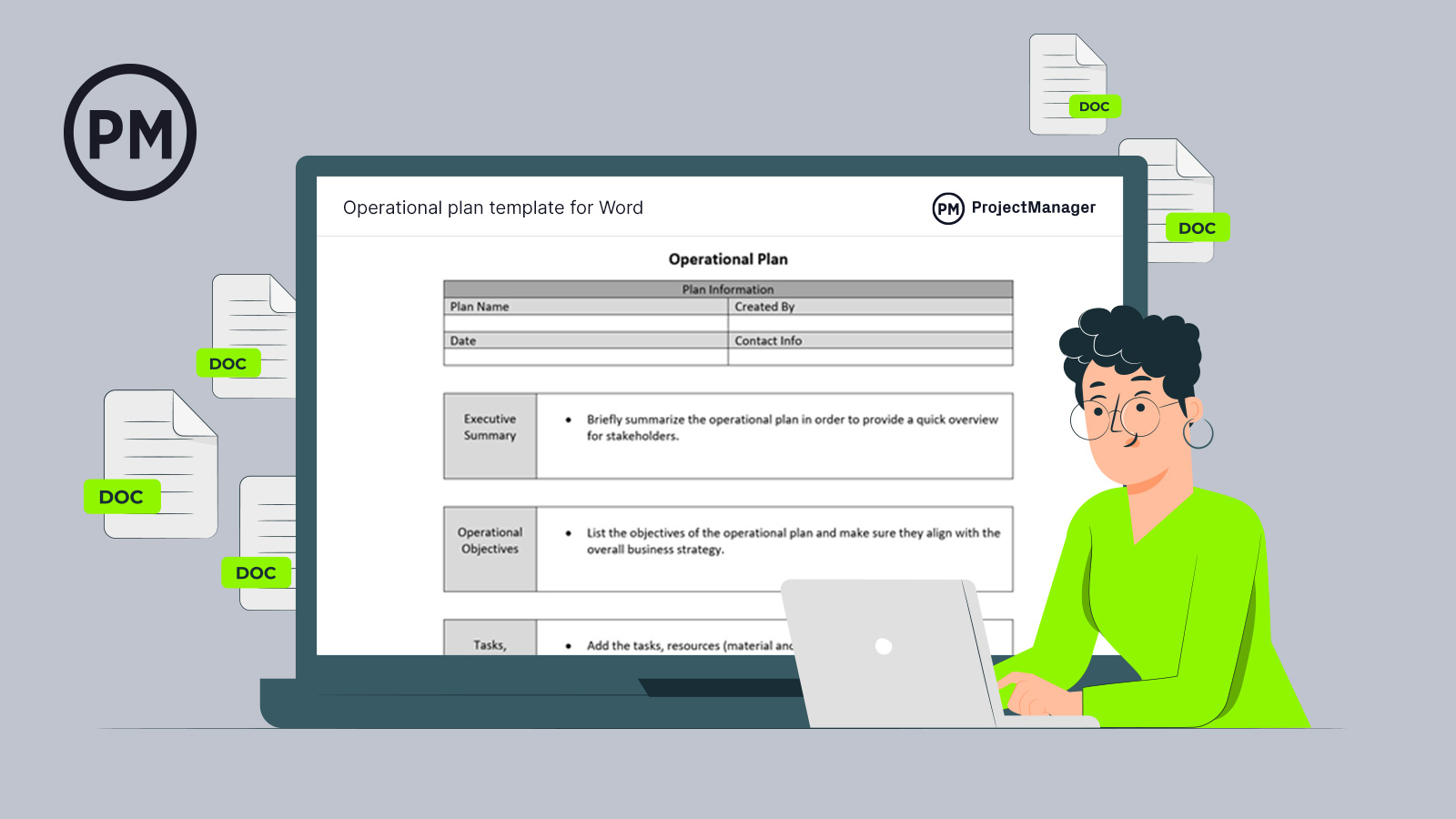
Get your free
Operational Plan Template
Use this free Operational Plan Template for Word to manage your projects better.
What Should be Included in an Operational Plan?
Your operational plan should describe your business operations as accurately as possible so that internal teams know how the company works and how they can help achieve the larger strategic objectives. Here’s a list of some of the key elements that you’ll need to consider when writing an operational plan.
Executive Summary
An executive summary is a brief document that summarizes the content of larger documents like business plans, strategic plans or operation plans. Their main purpose is to provide a quick overview for busy stakeholders.
Operational Budget
An operational budget is an estimation of the expected operating costs and revenues for a given time period. As with other types of budget, the operational budget defines the amount of money that’s available to acquire raw materials, equipment or anything else that’s needed for business operations.
It’s important to limit your spending to stay below your operational budget, otherwise, your company could run out of resources to execute its normal activities. You can use our free operating budget template for Excel to track your operating costs.
Operational Objectives
It’s essential to align your operational objectives with your strategic objectives. For example, if one of your strategic objectives is to increase sales by 25 percent over the next three years, one possible operational objective would be to hire new sales employees. You should always grab your strategic plan objectives and turn them into one or multiple action items .
Processes & Workflows
Explain the various business processes, workflows and tasks that need to be executed to achieve your operational objectives. Make sure to explain what resources are needed, such as raw materials, equipment or human resources.
Operational Timeline
It’s important to establish a timeline for your operational plan. In most cases, your operational plan will have the same length as your strategic plan, but in some scenarios, you might create multiple operational plans for specific purposes. Not all operational plans are equal, so the length of your operational timeline will depend on the duration of your projects , workflows and processes.
Hiring Plan
Find any skills gap there might be in your team. You might need to hire a couple of individuals or even create new departments in order to execute your business processes .
Quality Assurance and Control
Most companies implement quality assurance and control procedures for a variety of reasons such as customer safety and regulatory compliance. In addition, quality assurance issues can cost your business millions, so establishing quality management protocols is a key step in operational planning.
Key Performance Indicators
It’s important to establish key performance indicators (KPIs) to measure the productivity of your business operations. You can define as many KPIs as needed for all your business processes. For example, you can define KPIs for marketing, sales, product development and other key departments in your company. This can include product launch deadlines, number of manufactured goods, number of customer service cases closed, number of 5-star reviews received, number of customers acquired, revenue increased by a certain percentage and so on.
Risks, Assumptions and Constraints
Note any potential risks, assumptions and time or resource constraints that might affect your business operations.
Free Operational Plan Template
Leverage everything you’ve learned today with our template. This free operational plan template for Word will help you define your budget, timeline, KPIs and more. It’s the perfect first step in organizing and improving your operations. Download it today.
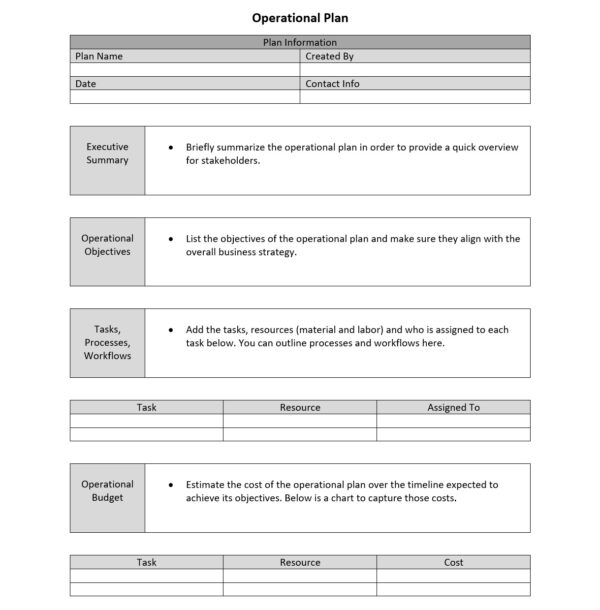
What Are the Benefits of Operational Planning?
Every plan has a massive effect on all team members involved, and those can be to your company’s benefit or to their detriment. If it’s to their detriment, it’s best to find out as soon as possible so you can modify your operational plan and pivot with ease.
But that’s the whole point of operational planning: you get to see the effect of your operations on the business’s bottom line in real time, or at every benchmark, so you know exactly when to pivot. And with a plan that’s as custom to each department as an operational plan, you know exactly where things go wrong and why.
How ProjectManager Can Help with Operational Planning
Creating and implementing a high-quality operational plan is the best way to ensure that your organization starts out a project on the right foot. ProjectManager has award-winning project management tools to help you craft and execute such a plan.
Gantt charts are essential to create and monitor operational plans effectively. ProjectManager helps you access your Gantt chart online so you can add benchmarks for operational performance reviews. You can also create tasks along with dependencies to make the operation a surefire success.
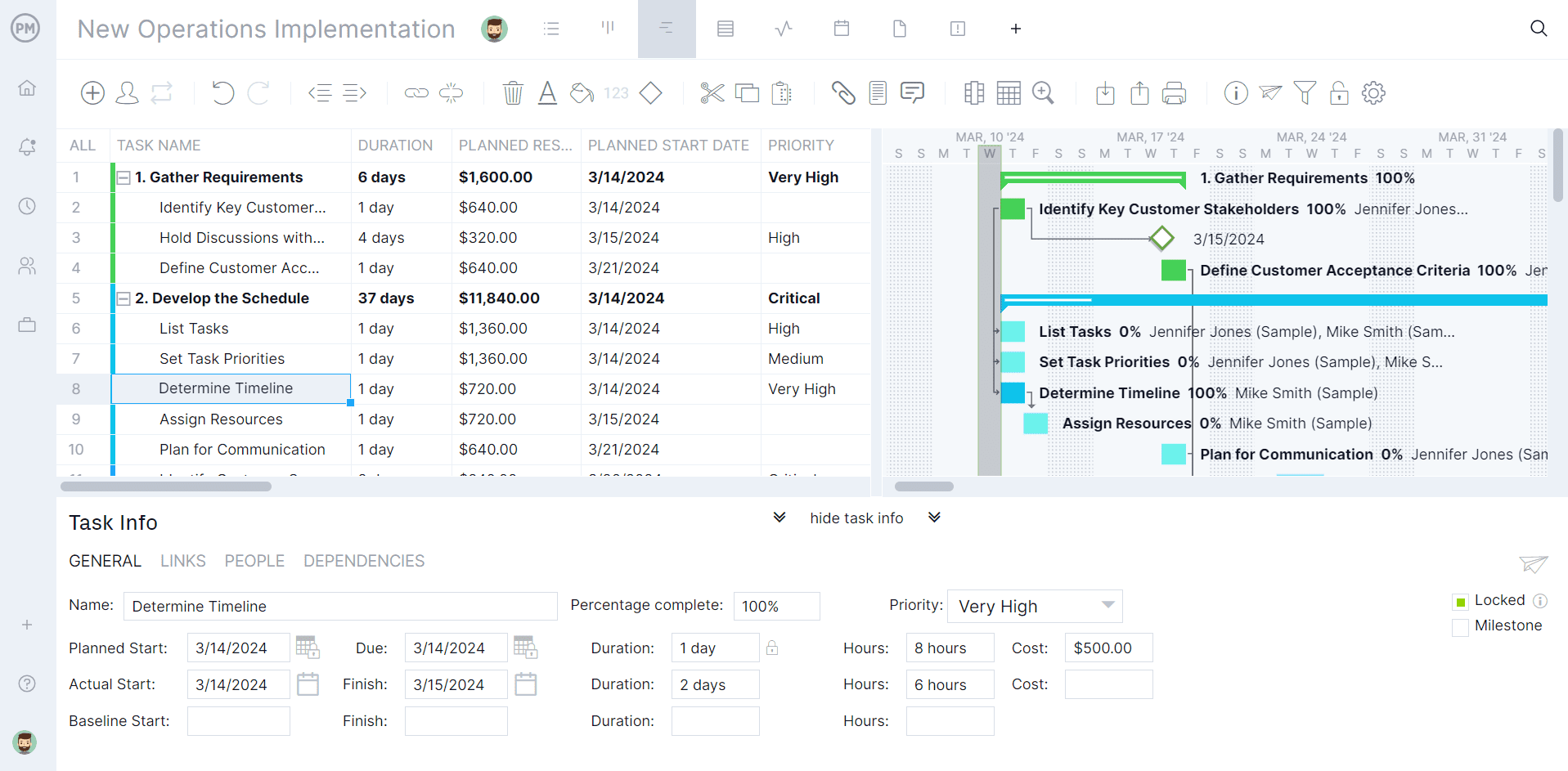
Whether you’re a team of IT system administrators, marketing experts, or engineers, ProjectManager includes robust planning and reporting tools. Plan in sprints, assign due dates, collaborate with team members and track everything with just the click of a button. Plus, we have numerous ready-made project reports that can be generated instantly, including status reports, variance reports, timesheet reports and more.

Related Operations Management Content
- Operational Strategy: A Quick Guide
- Operations Management: Key Functions, Roles and Skills
- Operational Efficiency: A Quick Guide
- Using Operational Excellence to Be More Productive
Operational planning isn’t done in a silo, and it doesn’t work without the full weight of the team backing it up. Ensure that your department is successful at each benchmark. ProjectManager is an award-winning pm software dedicated to helping businesses smooth out their operational plans for a better year ahead. Sign up for our free 30-day trial today.

Deliver your projects on time and under budget
Start planning your projects.
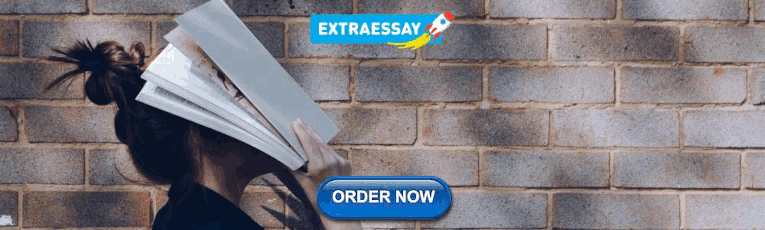
IMAGES
VIDEO
COMMENTS
Using a quality assurance plan template is an effective way to make it adaptable depending on the company's needs. For example, it can be adapted to be specifically for product or software quality assurance. Whether the organizational focus is on growth or customer care, each QAP focuses on those defined areas. ...
The plan includes the overall objectives, scope, timeline, and budget. This phase also includes creating a quality assurance plan. The quality assurance plan outlines how the project will be monitored and controlled. The second phase of documentation is the execution phase. This is when the actual work of the project is carried out.
Use these Top 10 Quality Assurance Plan Templates for peak performance and dependability. These templates will help you self-assess and ensure that your work meets set criteria. The 100% customizable nature of the templates allows you to edit your presentations. The content-ready slides give you the much-needed structure.
A documented procedure for changes and modifications to a quality plan as a process is improved. A method for measuring the achievement of the quality objectives. Other actions necessary to meet the objectives. At the highest level, quality goals and plans should be integrated with overall strategic plans of the organization.
Develop Quality Assurance Plan. Identify the role and responsibilities of the SQA team-. List of the work products the SQA auditor will review and audit-. Create the schedule to perform the SQA tasks-. Define the standards/methodology: Review the process. Things To Remember While Creating A Quality Assurance Plan (Best Practices)
All Agency organizations subject to the requirements of EPA Order 5360.1 A2 shall submit a Quality Assurance Annual Report and Work Plan (QAARWP) annually. The QAARWP shall summarize the results of having implemented the quality system the previous fiscal year and describe QA activities planned for the fiscal year beginning in October.
ISO 10005:2018 , Quality management - Guidelines for quality plans, gives guidelines for establishing and applying quality plans, and it has just been updated to provide more guidance and more examples to be relevant to organizations of all shapes and sizes. Roy Ackema, Convener of the working group that updated the standard, said that while ...
Step 1: Do the initial research and analysis. To kick off the planning process, assess the current state of your organization. Review the previous year's performance, considering various data sources, including financial statements and operational reports . By doing a thorough business review, you ensure that your annual operating plan for next ...
A quality assurance plan provides several benefits to manufacturing businesses. These include: Improved production efficiency: A quality assurance plan details the production process to ensure that all necessary standards are met. This includes identifying and preventing possible bottlenecks that may hamper production.
Furthermore, it's important to understand that QA is distinct from quality control (QC). 1. Define your business's standards and objectives. Envision what you want your customer support ...
USGS Examples. USGS Quality Assurance Plan for Digital Aerial Imagery (PDF) U.S. Geological Survey quality-assurance plan for surface-water activities in Kansas, 2015. Quality-assurance plan for the analysis of fluvial sediment by the U.S. Geological Survey Kentucky Water Science Center Sediment Laboratory.
The Quality Plan is an integral part of any project management plan. The purpose of the Quality Plan is to describe how quality will be managed throughout the lifecycle of the project. It also includes the processes and procedures for ensuring quality planning, assurance, and control are all conducted.
The Quality Assurance and Improvement Plan (QA/QI Plan) is a guide designed to assess, enhance, measure, and improve the quality of services, programs, and agency operations within the available resources and achievable goals of Community Services for Every1. The Agency believes that a strong commitment to Quality Assurance and Quality ...
ally. This provides an annual basis for assurance that the internal audit activity continues to operate in a manner consistent with requirements of the Standards and the Code of Ethics. This is especially important during periods of change in the Standards or in the organization. Quality Assessment Manual for the Internal Audit Activity 24
Quality Management Plan. Prepared for: U.S. Environmental Protection Agency Office of Air Quality Planning and Standards Research Triangle Park, NC 27711. EPA Contract No. EP-D-15-020. Prepared by: Air Quality Research Center University of California Davis, CA 95616. August 31, 2021.
As a collective, set up parameters to measure and track the success of your goals. 7. Bring it to the board. An annual operating plan is a helpful way for boards to review the business goals of any company. It creates an established tangible timeline, addresses resources, and opens the door for strategic feedback. 8.
The purpose of the Quality Assurance and Performance Improvement (QAPI) plan is to create an environment where safety is prioritized and high-quality healthcare services are provided in accordance with the principles of professional practice and ethical conduct. It must include, but not be limited to, an ongoing program that measures, analyzes ...
Operating Plan 414.1-1C, Quality Assurance Program Plan Page 6 of 20 to the environment and human health, impacting the safety of personnel, and affecting the reliability of research and critical data. (3) Quality improvement is a management principle that is carried out to improve a process that results in the production of critical data.
The student union is requested to provide its comments on the business plan and the quality assurance report in the annual report. The university college management is in constant contact with the student union regarding quality assurance and enhancement. 3.3 Course evaluations Responsible: Course coordinators
Quality Assurance and Control. Most companies implement quality assurance and control procedures for a variety of reasons such as customer safety and regulatory compliance. In addition, quality assurance issues can cost your business millions, so establishing quality management protocols is a key step in operational planning. Key Performance ...
A Quality Management Plan documents how an organization will plan, implement, and assess the effectiveness of its quality assurance and quality control operations. Specifically, it describes how an organization structures its. quality program, the quality policies and procedures, areas of application, and roles, responsibilities, and authorities.
− D6.01 Internal Quality Plan (IQP): o due in M2, December 2017 o defines the quality assurance methodology o establishes the quality assurance indicators with regards to the project procedures and deliverables o outlines the monitoring and evaluation mechanisms and tools to be used in the quality assurance process
QUALITY ASSURANCE AND ACADEMIC ACCREDITATION OPERATIONAL PLAN 2017-2022 QUALITY ASSURANCE AND ACADEMIC ACCREDITATION OPERATIONAL PLAN 2017-2022 KING SAUD BIN ABDULAZIZ UNIVERSITY FOR HEALTH SCIENCE (KSAU-HS) ... annual survey final year students). 3.2 Proportion of courses in which student evaluations were conducted during the year. ...