Join TheConstructor to ask questions, answer questions, write articles, and connect with other people. When you join you get additional benefits.
Confirm Password *
First Name *
Last Name *
Country Select a country… Åland Islands Afghanistan Albania Algeria Andorra Angola Anguilla Antarctica Antigua and Barbuda Argentina Armenia Aruba Australia Austria Azerbaijan Bahamas Bahrain Bangladesh Barbados Belarus Belau Belgium Belize Benin Bermuda Bhutan Bolivia Bonaire, Saint Eustatius and Saba Bosnia and Herzegovina Botswana Bouvet Island Brazil British Indian Ocean Territory British Virgin Islands Brunei Bulgaria Burkina Faso Burundi Cambodia Cameroon Canada Cape Verde Cayman Islands Central African Republic Chad Chile China Christmas Island Cocos (Keeling) Islands Colombia Comoros Congo (Brazzaville) Congo (Kinshasa) Cook Islands Costa Rica Croatia Cuba CuraÇao Cyprus Czech Republic Denmark Djibouti Dominica Dominican Republic Ecuador Egypt El Salvador Equatorial Guinea Eritrea Estonia Ethiopia Falkland Islands Faroe Islands Fiji Finland France French Guiana French Polynesia French Southern Territories Gabon Gambia Georgia Germany Ghana Gibraltar Greece Greenland Grenada Guadeloupe Guatemala Guernsey Guinea Guinea-Bissau Guyana Haiti Heard Island and McDonald Islands Honduras Hong Kong Hungary Iceland India Indonesia Iran Iraq Isle of Man Israel Italy Ivory Coast Jamaica Japan Jersey Jordan Kazakhstan Kenya Kiribati Kuwait Kyrgyzstan Laos Latvia Lebanon Lesotho Liberia Libya Liechtenstein Lithuania Luxembourg Macao S.A.R., China Macedonia Madagascar Malawi Malaysia Maldives Mali Malta Marshall Islands Martinique Mauritania Mauritius Mayotte Mexico Micronesia Moldova Monaco Mongolia Montenegro Montserrat Morocco Mozambique Myanmar Namibia Nauru Nepal Netherlands Netherlands Antilles New Caledonia New Zealand Nicaragua Niger Nigeria Niue Norfolk Island North Korea Norway Oman Pakistan Palestinian Territory Panama Papua New Guinea Paraguay Peru Philippines Pitcairn Poland Portugal Qatar Republic of Ireland Reunion Romania Russia Rwanda São Tomé and Príncipe Saint Barthélemy Saint Helena Saint Kitts and Nevis Saint Lucia Saint Martin (Dutch part) Saint Martin (French part) Saint Pierre and Miquelon Saint Vincent and the Grenadines San Marino Saudi Arabia Senegal Serbia Seychelles Sierra Leone Singapore Slovakia Slovenia Solomon Islands Somalia South Africa South Georgia/Sandwich Islands South Korea South Sudan Spain Sri Lanka Sudan Suriname Svalbard and Jan Mayen Swaziland Sweden Switzerland Syria Taiwan Tajikistan Tanzania Thailand Timor-Leste Togo Tokelau Tonga Trinidad and Tobago Tunisia Turkey Turkmenistan Turks and Caicos Islands Tuvalu Uganda Ukraine United Arab Emirates United Kingdom (UK) United States (US) Uruguay Uzbekistan Vanuatu Vatican Venezuela Vietnam Wallis and Futuna Western Sahara Western Samoa Yemen Zambia Zimbabwe
By registering, you agree to the Terms of Service and Privacy Policy . *
Log in to TheConstructor to ask questions, answer people’s questions, write articles & connect with other people. When you join you get additional benefits.
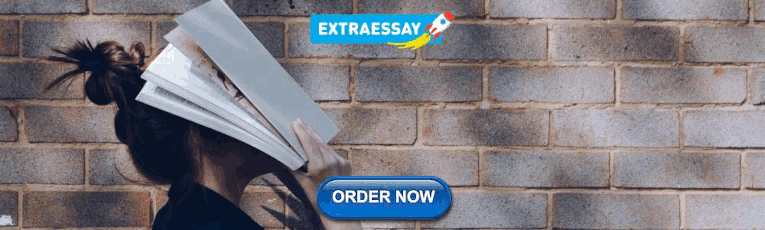
Join for free or log in to continue reading...
Username or email *
Forgot Password
Lost your password? Please enter your email address. You will receive a link and will create a new password via email.
Sorry, you do not have permission to ask a question, You must log in to ask a question. Join now!

The Constructor
Delays in construction projects, its types, effects and management.
Do you need to remove the ads? Join now!
🕑 Reading time: 1 minute

Processes in Construction Project Management
Types of delays in construction projects.
- One must determine whether the delay is critical or non-critical.
- Additionally, all delays are either excusable or non-excusable.
- Both excusable and non-excusable delays can be defined as either concurrent or non-concurrent.
- Delays can be further broken down into compensable or non-compensable delays.
A) Critical or non-critical Delays:
- Extended Field Overhead
- Unabsorbed home office overhead
- Liquidated Damage
- Idle labor & equipment cost
- Labor & Material Cost Escalation and many more.
B) Excusable & non-excusable Delay
- Force Measure Clause
- Natural Calamities
- Political/Social Unrest
- Terrorist Attacks
- Delay from Client (Approvals, Decisions, etc.), etc.
- Delayed Mobilization
- Delayed Procurement
- Delayed submission of important documents
- Planning & Scheduling
- Critical events that were not highlighted to client on right time, etc.
C) Concurrent Delays in Construction Projects
D) compensable or non-compensable delays in in construction projects, related posts.

Best Practices in Construction

16 Types of Pipelines and their Construction Method
- Parkville, MO
- Gilbert, AZ
- Campus Centers
- Current Students
- Park University Email
- Information Technology Services
- Faculty Center for Innovation
- News & Events
- Ways to Give
- Park Spirit Store
- Apply To Park
- Request Info
- Plan a Visit
Managing Construction Delays: Strategies and Techniques
Published on: November 3, 2023
Delays during the construction process are inevitable. The most successful construction managers anticipate delays in advance, apply construction delay analysis techniques, mitigate risk to the extent possible, and adjust their plan to limit downstream impacts when unexpected delays occur.
Expected Reasons for Construction Project Delays
In 2022 alone, 91% of construction managers surveyed indicated that they were involved in projects that experienced delays. Most of those delays were related to an unrealistic project plan (31%) and resource issues (19%).
Many of the delays in construction are expected; that is, they happen on enough construction projects that you can expect to face these risks on yours and should plan in advance to prevent them from stalling your project. The delays we categorize as expected are those due to lack of funding, increased costs, labor shortages, and poor planning or communication.
Lack of Funding or Investing
One of the most common causes for delays both early on and later in the project is lack of funding, and in most cases the greatest delay occurs because of insufficient initial funding. If the construction project is dependent upon loans, investments, or government grants, delays can ensue as the construction manager or project team navigates negotiations, paperwork, and potential alternative funding options.
Increased Costs or Spending
Going over budget can lead to construction delays for several reasons:
- It might be necessary to revisit the initial plans and designs to find cost-saving alternatives
- The team may need to seek additional funding to cover the difference
- Contracts may need to be renegotiated with the client, contractor, subcontractor, suppliers, or others
- The team might elect to purchase different materials than originally plan or delay the purchase of materials to ensure adequate funding, both of which can affect the timeline
Additionally, budget overages can increase project complexity, put strain on relationships with suppliers and contractors, change the availability of contractors and materials, and reduce the overall morale of the team, all of which can lead to delays in the delivery of your project.
Shortage of Available Labor
Construction is like a choreographed dance; each step in the construction process is dependent on the step before and likewise, is foundational to the step that follows. The timing of each resource’s contributions is critical and must be carefully orchestrated to ensure the drywallers come before the painters, for example.
When there’s a shortage of available labor, it can influence the entire project plan. If the project is ready for drywall installation on June 5th, but resources aren’t available to do the work until June 15th, all the steps that are dependent on drywall installation are also pushed out 10 days.
Lack of Communication and Planning
Lack of communication and careful planning is the single most prevalent cause of project delays in construction. Here are some examples:
- A crew arrives with excavators and backhoes to break ground on a new addition, only to find that utilities crews haven’t flagged the lot yet
- An oversight leads to a 10-day delay between completion of plumbing and scheduling the inspection, delaying drywall, trim, etc.
- The client elects to change the color of the hardware early in the project, but the designer fails to notify the construction manager and the wrong hardware is purchased and installed
These kinds of delays can lead to days, weeks, or even months of lost time and are preventable with adequate communication and planning.
How to Handle Expected Delays
The best way you can handle expected delays in your project is to anticipate those that can’t be prevented and prevent those that can with proper time management, planning, communication, and guidelines.
Time Management and Planning
There are several steps you can take to help anticipate, prevent, and adapt to delays as a construction manager:
- Always use a detailed project schedule that clearly identifies dependencies and estimates realistic timelines
- Build contingencies into your budget so unexpected costs become expected and anticipated
- Identify which activities in your project plan have more flexible timelines and which are rigid and will determine the overall project timeline
- Monitor progress daily to stay ahead of any action items, delays, or issues that arise and ensure timely handoff and communication
It’s also important to conduct a lesson learned session at the conclusion of each project to identify what you learned during that project and how you can apply it to future projects to prevent delays and improve outcomes. Review lessons learned before starting each new project to ensure continuous improvement.
Proper Communication and Realistic Guidelines
Proper communication is a valuable tool for construction managers as they prevent and navigate construction delays.
First, proper communication can help you prevent expected delays in the first place. Ensuring that all team members know the role they play in the project plan, including the timeline and the components of the project that are dependent on their work, can help facilitate communication and prevent delays.
Second, clear communication with both clients and contractors can help you set realistic guidelines around the construction process, including the likelihood that delays will arise.
Unexpected Delay Reasons
While most delays in construction are related to the expected problems we discussed above, including lack of funding, increased costs, labor shortages, and poor communication, delays can also be caused by unforeseen circumstances. These situations are less common, but when they do occur, they can be more catastrophic and lead to more extensive delays and other downstream impacts to your construction project, like damaged equipment, injuries, and additional costs.
Weather and Climate
Adverse weather conditions can directly impact your construction project. Rain and snow can make the site muddy and waterlogged, making it difficult to perform excavation, foundation work, or concrete pouring. Extreme heat can pose potential challenges for the health and productivity of workers and affect the curing of concrete and other materials. High winds can sometimes lead to safety concerns and pauses in work as well.
Freak and Uncommon Accidents
Sometimes unexpected and uncommon accidents can delay your project. These include equipment failures, natural disasters, hazardous material spills, unforeseen geological or site conditions, theft, vandalism, and worksite injuries. These situations can rarely be predicted or prevented – except in the case of worksite injuries – and require a different approach when they occur.
How to Handle Unexpected Delays
In some ways, you’ll do the same things during unexpected delays as you do during expected delays:
- Have realistic expectations about how much time it will take to get the issue resolved and get the project moving again
- Communicate with all involved as soon, as transparently, and as frequently as possible to avoid frustration and ensure alignment (especially when there’s a change from prior communication)
- Monitor the situation daily so you’re ready to set the project in motion when the pieces fall into place, avoiding any additional delays due to unpreparedness
However, in addition to these measures, unexpected delays require additional empathy, understanding, flexibility, and patience.
Consider how COVID-19 likely impacted construction projects. Although it doesn’t fit into the most common culprits, it’s certainly unexpected. Staff couldn’t work within six feet of one another. Employees and contractors who were exposed had to quarantine and those who were symptomatic or who tested positive had to isolate. Childcare facilities were closing down without notice, leaving workers unable to fulfill their obligations at work. Clients who had already secured financing faced unexpected job loss and financial changes at the last minute, halting projects mid-construction. Building materials were in short supply and in some cases, on backorder for months at a time. While realistic project expectations, communication, and monitoring helped, compassion and, in most cases, a new plan were also required.
Flexibility and Understanding
Unexpected delays require flexibility and understanding. In most cases, the chances that the project will get back on schedule are low. Instead of working to get the project back on schedule, focus on addressing the issue at hand, showing empathy for those affected, and translating that empathy to the client to bridge the gap. Set realistic expectations with all involved around how long it will take to be up and running again, how the unexpected delay will affect the project budget and timeline, and what you’re doing to help.
Patience During Delay
The single most important trait you can display during catastrophe is patience. When illness, loss, injury, or another catastrophe has delayed a project, it’s important to give your stakeholders the time they need to recover. Pressuring the team to get back to work before they’re ready can lead to disengagement, reducing the quality of work, increasing the likelihood of injury, and ultimately driving costs and extending the timeline even further.
On the opposite site of that coin, patience and empathy can build camaraderie that drives stakeholders to deliver as soon as feasible, supporting a successful project.
Creating and Executing a New Plan
Finally, be proactive in recognizing when it’s time to go back to the drawing board. Sometimes the original plan can’t be adjusted to accommodate catastrophe and you have to start over. In these cases, sit down with all stakeholders, facilitate an honest conversation about the risks and barriers, and draft a new project plan that takes into consideration the resources that are available. Consider whether the same issues are likely to arise again and take steps to mitigate risk. Be realistic when you estimate timelines – even if it means the project will take longer to complete – to prevent delays and coordinate teams this time around. Ensure you have buy-in from the entire team before you move forward.
Your Story in Construction Management Starts Here
Whether you’re nearing high school graduation or considering a career change well into adulthood, it’s never too late to explore a career in construction management. Construction management can be a great way to put your communication and strategic thinking skills to work to propel major projects that excite you and improve your community.
Take the first step toward your career in construction management today! Join Park University’s respected Construction Management program to prepare yourself for a rewarding career in the construction industry. Gain the knowledge, skills, and hands-on experience you need to excel in this exciting and challenging field.
Enroll now to begin learning from industry experts, engaging in real-world projects, and build a strong professional network.
Park University is accredited by the Higher Learning Commission .
Park University is a private, non-profit, institution of higher learning since 1875.
- Share full article

Years of Delays, Billions in Overruns: The Dismal History of Big Infrastructure
The nation’s most ambitious engineering projects are mired in postponements and skyrocketing costs. Delivering $1.2 trillion in new infrastructure will be tough.
When completed, the Cedar Viaduct project that runs through the Central Valley in Fresno, Calif., will carry high-speed rail over State Route 99. Credit... Patrick T. Fallon/Agence France-Presse — Getty Images
Supported by
By Ralph Vartabedian
- Nov. 28, 2021
As Honolulu sprawled into new suburbs west of Pearl Harbor over the last two decades, city planners proposed an ambitious rail transit line that would sweep riders 20 miles into downtown. The $4 billion estimate in 2006 was hardly cheap, amounting to $200 million per mile.
The cost escalation since then has been an engineering marvel all its own. Concerns over Native Hawaiian burial grounds stalled early construction, then problems with welding and cracks in the tracks appeared. Earlier this year, engineers realized that in some sections, the wheels were a half-inch narrower than the rails. Order new wheels? Tear up the tracks?
The launch dates slipped forward and the cost estimates crept upward — at latest count, $11.4 billion, with a target completion date of 2031.
Honolulu’s tribulations are far from a lone cautionary tale. To the contrary, they signal the kind of cost overruns, engineering challenges and political obstacles that have made it all but impossible to complete a major, multibillion-dollar infrastructure project in the United States on budget and on schedule over the past decade.
As the nation sets out on a national spending spree fueled by the $1.2 trillion infrastructure bill signed by President Biden this month, the job ahead carries enormous risks that the projects will face the same kind of cost, schedule and technical problems that have hobbled ambitious efforts from New York to Seattle, delaying benefits to the public and driving up the price tag that taxpayers ultimately will bear.

American cities and states were long renowned for some of the greatest bridges, water systems and freeways in the world, but challenges have grown more potent. Agencies have less internal technical talent. Legal challenges have grown stronger under state and federal environmental laws. And spending on infrastructure as a fraction of the economy has shrunk, giving local agencies less experience in modern practices.
The $1.2 trillion package has bold goals, directing the majority of $500 billion to highways, $39 billion to urban transit, $65 billion to broadband projects and $73 billion to electrical grids, among other items. The nation’s busiest passenger rail line, Amtrak’s Boston-to-Washington corridor, would get the biggest slice of a $66 billion rail package. The infrastructure spending plan is unlikely to rescue some existing infrastructure projects that are bogged down with problems.
And even with the new infusion of money, analysts say it will be tough to ramp up infrastructure progress as swiftly as envisioned in the current timetable.
The construction industry is facing sharply growing costs for steel products, up by 142 percent in the last 12 months, and other key materials. Shortages of skilled labor are worsening, exacerbated by Covid-induced retirements.
“A lot of people would like to see the money quickly spent,” said Anirban Basu, chief economist of Associated Builders and Contractors, a construction industry trade group. “They are going to look at the costs they are facing and extend out the projects because of constraints.”
Bent Flyvbjerg, a professor at the University of Oxford who has studied scores of projects around the world, found that 92 percent of them overran their original cost and schedule estimates, often by large margins — in part, he said, because cost estimates are “ systematically and significantly deceptive .”
“A lot of projects are not delivering what they promised to deliver,” he said.
In Baltimore this month, Mr. Biden lamented that U.S. infrastructure was once rated the world’s best and now, “You know what we rank in infrastructure? Thirteenth in the world. ”
In some cases, U.S. construction costs are higher than those in Western Europe and democratic nations in Asia, according to an upcoming University of California, Berkeley, analysis, said Ethan Elkind, a law professor and director of the school’s climate program.
“It is a lot harder to build projects here, and we are not as skilled at doing it,” he said.
When California voters approved a bond in 2008 for a high-speed rail system from Los Angeles to San Francisco , the project was supposed to cost $33 billion and be completed by 2020 . The job is now projected to finish in 2033 for $100 billion, though those estimates are dated and there is an $80 billion funding gap.
The ambitious project, the nation’s most serious effort to build a full-scale bullet train, has encountered serious delays because of land acquisition issues, environmental litigation, permit setbacks, employee turnover and significant design changes. The problems have triggered political infighting even with the Democratic supermajority in California.
Lengthy delays have also affected New York’s East Side Access extension of the Long Island Rail Road, which is supposed to cut up to 40 minutes off commuter time on the last segment, from Queens to Grand Central Terminal, with up to 24 trains per hour at peak times.
Conceived more than a half century ago, with a construction contract awarded in 2006, that project was supposed to be completed by 2011. Early estimates put the cost at $2.2 billion, then $4.3 billion in 2006 and $6.4 billion in 2008. The Metropolitan Transportation Authority now envisions completion in December 2022 at a cost of $11.1 billion. Design changes, underground tunneling problems and coordination with other agencies were some of the factors in the delays and cost increases.
One of the nation’s most important environmental infrastructure projects, and perhaps the most technically difficult one, has been underway in Central Washington State for decades at the former Hanford nuclear weapons site. Since 2013, major construction has been stopped at two partially built plants to treat and vitrify 56 million gallons of radioactive sludge.
When an independent review in 2015 found 362 significant design problems, the Energy Department announced a 17-year delay and estimated the system would become fully operational in 2036.
The problems included the failure to anticipate the potential for an earthquake to damage equipment and the possibility that the chemical processes to separate high-level radioactive materials could cause explosive hydrogen gas to form.
The delays have pushed the Energy Department to adopt an alternative that would start treating low-level waste by the end of 2023, Washington State officials said. The last cost estimate for the plant was $17 billion, up from $12.3 billion in 2013 and about $4 billion 20 years ago.
The rail project in Hawaii was intended to relieve congestion on a par with Los Angeles along the urban band from East Kapolei to the core of Honolulu.
The Honolulu Authority for Rapid Transportation believes it can address the latest track problems by welding certain sections of track and later replacing wheels to match the track size, said a spokesman, Harry Cho.
The setbacks that resulted in delays — archaeological surveys, labor costs, utility relocations and land acquisition — are the kind of challenges that plague nearly all major infrastructure projects; the common mistake is in not planning and budgeting for them, said Joseph Schofer, a Northwestern University civil engineer and originator of the “Infrastructure Show” podcast.
“You can’t say these were an accident,” he said of most cost overruns. “We could do better. We haven’t gotten honest estimates in a lot of cases.”
Mr. Schofer said many projects are justified by estimating that future benefits will exceed costs, but when the costs go up astronomically, no one recalculates the ratio.
In a candid admission of how the political world operates, Willie Brown, the former mayor of San Francisco, once dismissed cost overruns on a transportation hub intended for the bullet train.
“In the world of civic projects, the first budget is really just a down payment,” he wrote in a guest newspaper column in 2013 . “If people knew the real cost from the start, nothing would ever be approved. The idea is to get going. Start digging a hole and make it so big there’s no alternative to coming up with the money to fill it in.”
U.S. Transportation Department officials declined to comment for this article, but Biden administration officials have said the new infrastructure package will redress decades of neglect and will boost the efficiency of the American economy, address climate change and provide immediate jobs in construction.
“We’re going to reduce congestion,” Mr. Biden said. “We’re going to address repair and maintenance backlogs, deploy state-of-the-art technologies and make our ports cleaner and more efficient.”
Mr. Flyvbjerg, the Oxford professor, said infrastructure keeps getting more expensive at a time when many products, such as televisions, refrigerators and computers, get cheaper or better each year.
“Big infrastructure is becoming cost prohibitive,” he said, a problem he blames on institutional sclerosis at government agencies that keep repeating mistakes and choose infrastructure projects that are unlikely to succeed.
The mistakes, he said, include a lack of transparency to the public, flawed contracts that put government agencies at the mercy of contractors and a failure to attract enough private investment to bear some of the project’s risk.
The new infrastructure law, he said, does little to change the outlook.
Ronald N. Tutor, chief executive of Tutor Perini, a California firm that is building some of the nation’s largest projects, said the industry has done a good job of advancing and completing projects that by their nature are complex and unpredictable.
“All the major projects have cost and schedule issues,” he acknowledged. “The truth is these are very high-risk and difficult projects. Conditions change. It is impossible to estimate it accurately. That is naïve.”
The infrastructure law takes some initial steps at reforms, including codifying a Trump executive order to name a lead federal agency for each project, reducing the number of chefs in the kitchen, said Diana Furchtgott-Roth, who formerly oversaw Transportation Department research and technology and now is a George Washington University adjunct professor.
A key factor is the amount of time federal agencies spend to review environmental reports and issue records of decision, she said. In many cases, she said, projects are put on hold for years, while agencies review voluminous documents.
Mr. Biden also named a task force to carry out the infrastructure program with an aim to “invest public dollars efficiently, avoid waste and focus on measurable outcomes for the American people.”
The environmental review process has become so complex, in part to defend against inevitable lawsuits, that neither state agencies nor federal departments can write and review the documents without teams of outside consultants.
Most of the spending under the $1.2 trillion infrastructure plan has been previously authorized, but the law includes $550 billion of new money to be spent in as little as five years.
Federal, state and local agencies were working their way through $270 billion a year in authorized spending in 2019, before the pandemic hit. An attempt to bump that up by an additional $100 billion annually, as envisioned, represents a 37 percent jump that may not be possible to achieve, industry analysts warn.
“It is a very big bump,” said Ken Simonson, chief economist at Associated General Contractors of America, which represents major infrastructure builders. “My guess is that we are not going to see $550 billion spent in the first five years.”
Advertisement

Upcoming Webinar: Overview of ScheduleReader and ScheduleCleaner | 27 June, 10 - 11 AM GMT

Top 8 Reasons for Delays in Construction Projects
Construction projects are one-off strives with many distinctive features like a long period, abominable environment, complicated processes, financial intensity, and such technological and organizational complexity creates enormous risks which resulted in the form of delays in construction projects in completion and cost overrun.
In construction, the delay can be defined as the extra time required or incurred either beyond the stipulated completion date or beyond the date that the project stakeholders agreed upon for the completion of the project.
Successful completion of the project on time is an indication of the efficiency of all stakeholders involved in the project but the construction process is subject to many variables and unpredictable factors, which result from many sources.
The following are the main reasons for delays in construction projects. With proper management, technical knowledge, and techniques these delays can be reduced to a minimal level.
1. Change In Project Scope
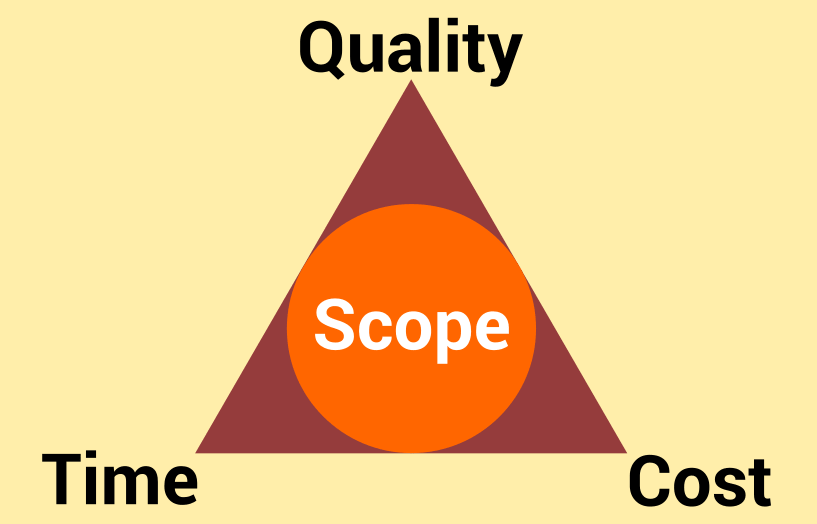
The scope of work in a construction project defines as the deliverables that are expected at the end of a project.
Poor scope definition at the start can be a result of cost overrun and time delay of any construction project. Therefore all the project plans, schedule, cost, and quantity estimation, procurement and quality mechanism are usually calculated from the initial project scope.
Change in project scope could be due to poor initial project scope definition, miscalculation of inherent risks and uncertainties, project funding issues, change in the interest of the client or force majeure, etc.
This could result in variation order that successively could lead on to vary in project deliverables, budget and/or even the entire project team.
Thus, any modification/change within the project scope throughout execution will cause the whole initial project set up to be revised the i.e revised budget, construction methodologies, construction schedule, procurement plan, quality assurance plans, etc which will lead to more time, resources and cost against the initial baseline to complete the works.
To attain the proper control on change in project scope, it is necessary to first identify the fact that change is inevitable in the project and could equally be beneficial to the entire project’s success. Thus the foremost necessary factor to try and do is to integrate a correct change in scope management set up such a proactive approach that might be adopted involving the project stakeholders and incorporating their needs throughout the project lifecycle.
During the initial planning phase of the project, it is important to identify the key success factor in conjunction with the client and establish key performance indicators in the form of milestones that will calculate the success for achieving the project scope.
Similarly, to avoid disputes, it’s necessary to perpetually ask for approval for changes from the sponsor and communicate changes in an exceedingly timely manner and for extremely evolving modification in the project during construction, the scope might be frozen to focus on the expected future deliverables.
2. Project Complexity

Complexity might be outlined in terms of the scale of the project, most mega construction projects i.e dams, motorways, skyscrapers, nuclear power stations, etc. tend to possess a comparatively long implementation duration in comparison to the small construction project i.e residential houses, shops, non-commercial buildings, etc.
This might result in a change in material prices, changes in exchange rates, and inflation rates such that the initial proposed/allocated budget needs to be supplemented for the project to be completed.
The result might be an increased cost and long chains of negotiation which eventually will cause a delay in the overall duration of the construction project.
Similarly, projects with a high degree of complexity usually result in complex plans, schedules, and estimations.
If proper care is not taken the ability to exclude these complex aspects of the project, it would lead to the variation orders, resultantly would lead to time delay and cost overrun.
This could lead to delays and costs.
Also, project quality might even be outlined in terms of the variety of stakeholders with totally different interests and an extended chain of communicating with slow feedbacks. Therefore desegregation of their interest might take plenty of valuable time and resources that once unnoted might lead to conflicts and disputes, thus affecting the project in the context of delay and cost overrun.
Extensive planning is required to eliminate or reduce the impact of time delay and cost overrun by calculating/incorporating every major aspect of the project, detailed WBS, major milestones, project stakeholders, the methodology to be adopted, and delivery time to the client.
Managing complex projects need experience, expertise, and exposure. Thus Project needs its goals and scope to be defined, based on the client requirements. To keep the project on track and ensures doing solely the task that’s aimed. It is thus vital to create an honest team with project success interest inside to attain this.
3. Inadequate Planning

The term planning is being used in many ways and different contexts but it can be explained as planning the human and machinery inputs in a way that to avail the maximum output is called planning.
To plan a project means to identify/distinguish the tasks or work activities to be performed to obtain the desired outcome in minimum time and cost, this starts the day the idea to put up a project is conceived.
There are several professionals and workmanship involved in the construction process, so a planner has to make sure that every aspect of these is already incorporated in the planning process to obtain the maximum outcomes and best results.
During the construction phase, the planning means calculating all the plants, types of equipment, materials, suppliers, human resources, time, and cost required to complete the curtain phase of the construction.
During the construction process, there are certain activities/tasks which require time to settle or to perform the successor activity i.e concrete curing time, the time required for laying the other layer of concrete, prime coat required to settle, etc.
A planner or responsible person should have adequate knowledge of these settling times to ensure while planning.
With proposed planning deliverables and inadequate planning outcomes in delayed project completion, cost overruns, and poor quality work among other things.
It is so necessary that the team responsible for the project accurately and plans before the execution of activities to confirm the sleek flow of works, the value of money, and timely completion.
4. Impropriate Project Schedule

Scheduling is a method in which the work activities are arranged in a sequential logical order to achieve the project within the stipulated time frame.
Scheduling shows not only the logical order in which the activities are intended to be carried out, but also enables the participants of that project to monitor progress. In addition, the schedule depicts the project’s future work while providing historical data that could be useful in analyzing the past.
This most common type of scheduling to the portrayal of bar chart; either hand-drawn or, more likely nowadays, computer- generated using commercially available project planning software i.e Oracle Primavera P6, Microsoft Project, Asana, Ceiton, EnQuire, and Huddle, etc.
To properly lead and work on a project the scheduling is an integral part to maximally utilize the available manpower and resources.
Scheduling requires immense technical knowledge, the sequential order of construction activities, accurate logical relation between the activities and resources required for each activity.
With impropriate project schedule the precious project resources will be diverted to the activities which are not critical and as a result, the critical activities will suffer and the delay will occur in over the construction time frame.
To mitigate the scheduling problems the scheduler should have the technical knowledge base that is relevant to the project, the scheduler should be able to accurately understand the scope of the job and work around this in an effective manner.
He should have strong knowledge and grip to properly identify how each event within the project should pan out. Strong knowledge of Contracts, Engineering Estimates, Bill of Quantities, Engineering Drawings, Project Scope, Nature of the Works, Clients requirements, and relevant documents enables the scheduler to develop a comprehensive Work Break Down Structure (WBS) with all the activities, resources, costs, constraints and risks involved in the project.
A scheduler should have hands-on experience in a variety of modern project management software i.e Oracle Primavera P6, Microsoft Project, Asana, Ceiton, EnQuire, etc. Knowledge of Oracle Primavera P6 is preferred as it is being used in most industries as an effective project management tool.
The Oracle Primavera P6 is a comprehensive/broad, scalable, project planning, scheduling, and monitoring software, built on Oracle or Microsoft SQL databases for organization-wise comprehensive project management.
Primavera required trained experienced experts to operate as it’s not user-friendly software. But if someone wants to share Primavera P6 information with all the project stakeholders or team members and make it accessible to view and print or analyze the Primavera file (.xer) I strongly suggest ScheduleReader software.
ScheduleReader is an easy-to-use project viewer that gives the liberty to view, print, and analyze the direct Primavera P6 (.xer) files dynamically without going through the tedious process of generating the .pdf report from a Primavera professional. This software is also available to download in a 15-day free of charge, trial period.
It also allows you to see through the .xer file which makes it more accessible to all the stakeholders of the project and saves countless hours for the consumers. ScheduleReader interface looks very similar to Primavera but it’s clean and more user-friendly with all the tabs on top of the screen are aligned with Primavera’s default screen.
The Gantt charts look more stylish like Microsoft Project with a smooth display of activities, WBS, Milestones, and relations, etc. In ScheduleReader one can update the progress of activities and it will generate .xlxs file which directly can be imported in Primavera P6 software and upon scheduling it will schedule the work plan automatically.
Furthermore, one can also compare the progress with baseline by directly importing the .xer file in SchduleReader, and similarly like Primavera P6, four (4) baseline files can be added and compare to check the deviations if any in the work plan for better monitoring of the works.
5. Design Variation

Design variation/error is a major factor for delay and cost overrun in a construction project.
It is vital to notice that accurate representation of the employer’s demand and therefore the blueprint to achieving better technical input to project execution are typically sorted out base on project designs and specifications.
A faulty design means insufficient or inaccurate project deliverables during the execution of the project.
This will lead to the incorrect application of techniques in achieving successful results, such as because the actual execution section of the project unfolds these design errors in the later stage, attempts to correct it will cause a time delay and value cost overrun.
Secondly, all project costs, time, and quality estimation based upon these designs and changes in the design in a later stage will eventually cause the cost and time variation orders.
Achieving accurate design entails properly documented communication with the design teams of all stakeholders and integration of a design method that’s accurately planned, giving sufficient time for modifications, corrections, extensive investigation, reviews, and final approvals.
Similarly, effective project planning, controlling, and monitoring should be established to enhance project performance throughout the project life cycle.
6. Inaccurate Engineering Estimate

Before the execution of any project, the Employer assesses the initial size of the investment required to incur in the project by an Engineer estimate.
Based upon the Engineer Estimate all economic benefits and calculations are done that’s why the engineer estimate needs realistic cost figures.
A detailed investigation study, extensive design expertise, a clear scope of work, accurate quantity calculations, and proper planning with complete modus operandi is required to obtain the Engineer estimate.
Inaccurate/error in estimation will cause the cost overrun and subsequently will result in a delay in the duration of the project.
Achieving the accurate Engineering estimate required the quantity take-off engineer to extensively approach all the stakeholders of the project to obtain all the relevant information required to calculate the cost.
Similarly, effective communication with design sections and the Client is required to enhance the chances of the most accurate engineering estimation.
7. Inefficient Material and Equipment Management

Material and equipment management is also an integral component during the execution of the project.
Both represent a major cost expense in any construction project and material accounts for 60% to 70% of the direct cost of a building project.
So minimizing the total procurement/purchase or rental cost can hugely influence the overall cost of the project.
The materials and equipment management system commits to make sure that the appropriate quality and quantity are selected, purchased, transported, delivered, and handled on-site in a timely manner and at a reasonable cost.
Poor management can also result in large and avoidable costs during construction and delay in the completion of the critical works due to the non-availability of the material and equipment at a crucial time.
Good management in construction must vigorously pursue the efficient utilization of the material and equipment.
Material and equipment handling, which includes procurement, inventory, shop fabrication, and field servicing, requires special attention for time-saving and cost reduction.
The use of modern technologies and innovative ways has created potential wholesale changes in construction technologies.
With the right coordinated planning, evaluating the quantities and requirements, sourcing, purchasing, transporting, storing, operation, and maintenance of the equipment, minimizing the wastage and optimizing the profitableness by reducing the price and saving them valuable time.
8. Improper Post Execution Phase Management

Finally, the closure or post-execution phase of any construction project is an extremely crucial stage that contains several potential factors that can ultimately lead to cost overrun and delay.
As it’s the last phase of any project life cycle and often ignored or less valued by even large organizations.
Slow closure can lead to dragging the final handing over of several milestones by unresolved disputes/claims linked with client’s final approval, variation order issues, acceptance of final payment certificate, issuance of retention money, issuance of performance security/bond, and failing to close out these works will cause unexpected delay and extra cost to all stakeholders of the project.
To avoid delay due to improper closure one must make sure the project is 100% completed with detailed documentation readily available. All the necessary information and documents required by all the stakeholders have been submitted to avoid doubt and conflicts in the future.
In conclusion, although time delay and cost overrun are very common in construction projects but it can be reduced or eliminated by adopting a proper performance monitoring mechanism and control system that will be integrated with all the key aspects and activities of each phase of the construction project .
Better communication among all the stakeholders of the projects with a clear understanding of the project success criteria and KPI will lead to the successful completion of the project without delay and cost overrun but by providing the best quality.
About the Author:
Vivien Goldstrong is a Consultant, Author, and Planning Manager with 22 years of experience and expertise in implementation and consultancy related to Oracle Primavera P6.
Privacy Overview
- Google Analytics
- LinkedIn tag
- Facebook pixel
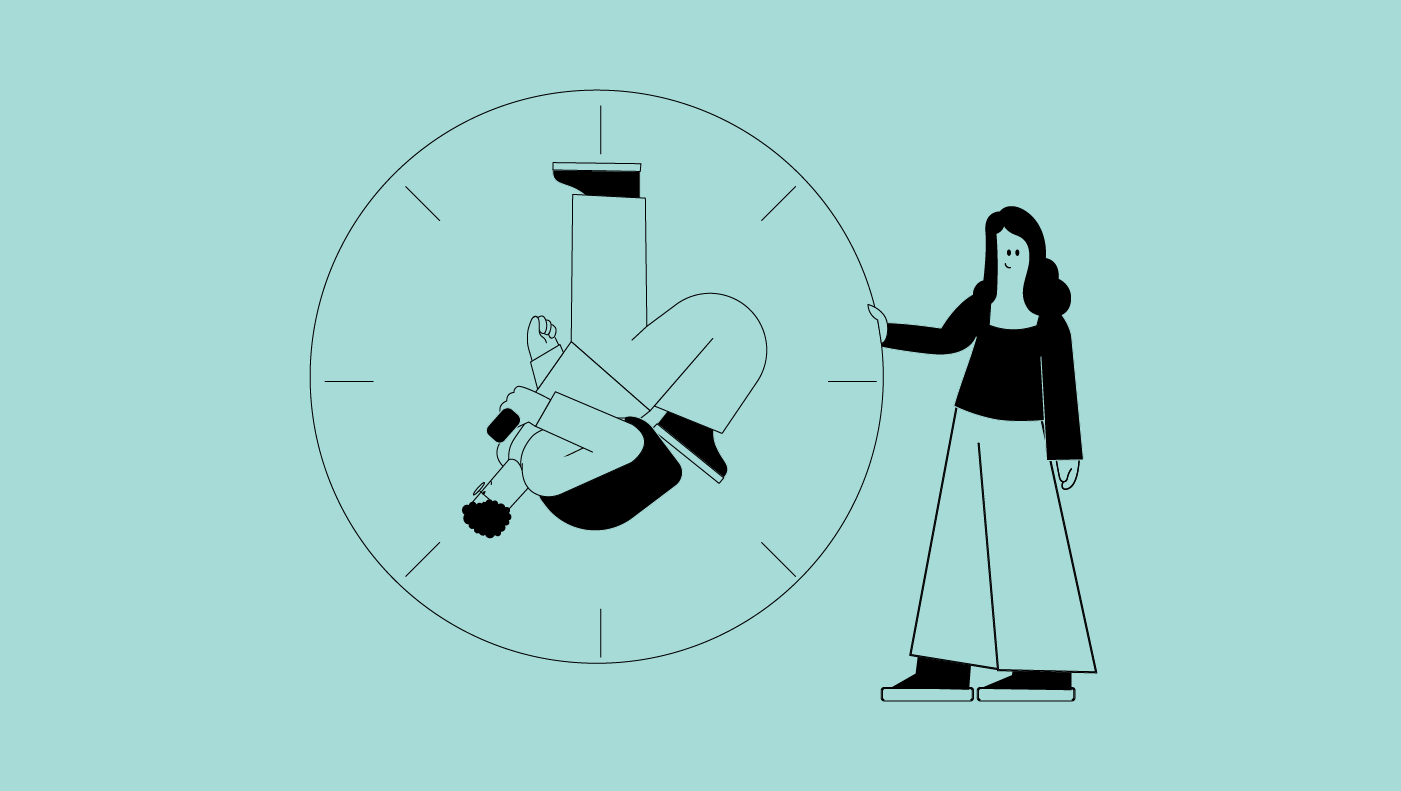
10 Causes of Projects Delays and How to Manage Them
In the dynamic world of project management, delays can often become an unwelcome yet recurrent reality. These unexpected hiccups not only disrupt timelines but can also have a significant impact on overall productivity and profitability. This article aims to delve into the complex issue of project delays, unraveling their causes, implications, and potential solutions.
By understanding these delays comprehensively, we aim to equip project managers and team members with the knowledge and strategies needed to anticipate, mitigate, and effectively manage any roadblocks that might emerge in the execution of their projects. Join us as we embark on this insightful exploration of project delays, a crucial aspect often overlooked in project management literature.
What Causes a Project to Get Delayed?
A project delay refers to an unforeseen circumstance that causes a setback in the planned schedule of a project. This could mean tasks and milestones are not completed within the established deadlines, leading to an overall extension of the project's timeline beyond what was originally forecasted.
Identifying these delays early is crucial for several reasons:
- Minimize Cost Overruns
- Maintain Reputation
- Efficient Resource Allocation
- Risk Management
- Stakeholder Communication
Causes of Project Delays
Poor planning.
This occurs when a project's objectives, resources, and timelines are not clearly defined or realistic. Projects can easily veer off course without proper planning, leading to delays and cost overruns.
Scope Creep
Scope creep refers to uncontrolled changes or continuous growth in a project's scope. This can happen when the project is poorly defined, documented, or controlled. It often leads to extended deadlines as more tasks are added to the project.
Resource Constraints
This includes limitations on personnel, equipment, or materials. If adequate resources are unavailable when needed, the project's progress can slow down.
Poor Communication
Inadequate communication among team members can lead to misunderstandings, confusion, and mistakes, resulting in project delays.
Risk Management Issues
If potential risks aren't identified and planned for in advance, they can cause significant disruptions when they occur.
Task Dependencies
Task dependencies are tasks that rely on each other to be completed. If one task is delayed, it can delay all other dependent tasks, causing a chain reaction of delays throughout the project.
Project management tools such as ActiveCollab have finish-to-start task dependencies, where a parent task must end before the child task can begin.
Task Complexity
The more complex a task, the more time it typically takes to complete. If the complexity of certain tasks is underestimated, it can lead to delays.
Lack of Skills or Training
If team members lack the necessary skills or training to complete their tasks efficiently and effectively, it can slow down the project's progress.
Changes in the Project Team
Changes in the project team, such as key team members leaving or new members joining, can disrupt the workflow and cause delays.
External Factors
These are events outside the project's control, such as market changes, changes in laws, or economic shifts. These factors can influence a project's timeline and cause unexpected delays.
Identifying Project Delays
Identifying project delays early is crucial for effective project management. Strategies and tools aid in this process. Use project tracking and reporting features, monitor your KPIs, set notifications and reminders, and regularly communicate with your team.
- Project Tracking: This involves regularly monitoring the project's progress against its planned schedule . Tracking can reveal if tasks take longer than expected, signaling a potential delay.
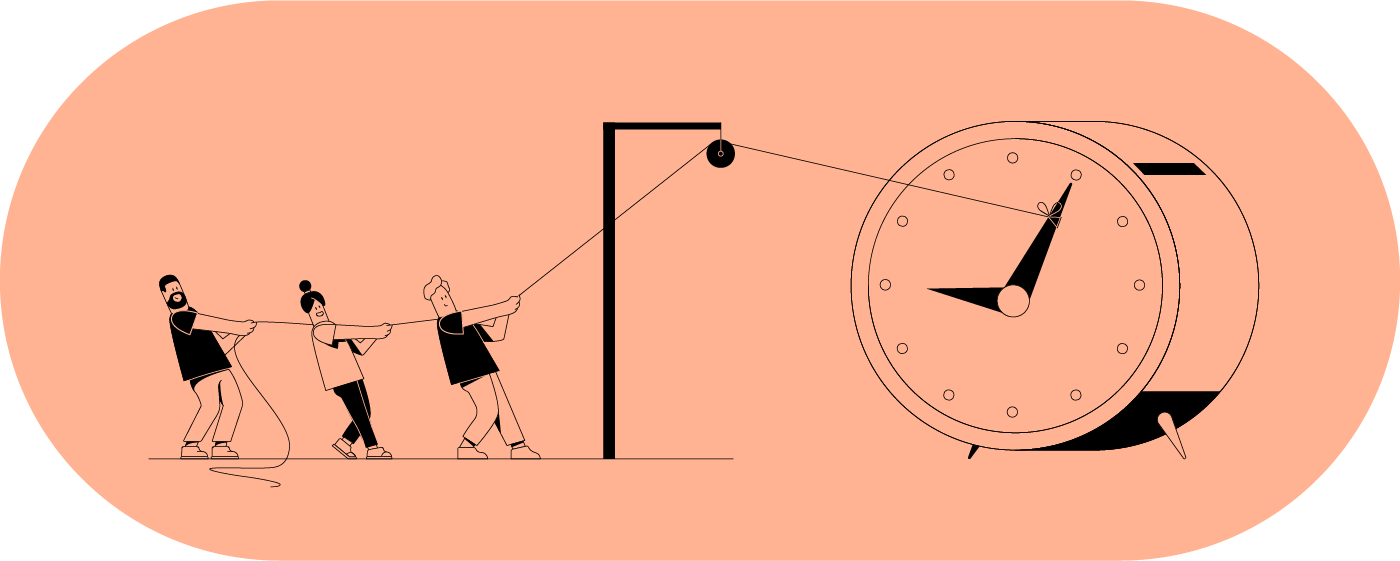
ActiveCollab's timeline view visually represents your project schedule, allowing you to see which tasks are on track and which are falling behind. It's an excellent tool for identifying potential delays before they become a problem.
- Reporting Features: ActiveCollab, like many project management tools, offers reporting features that can generate detailed reports on project progress, resource allocation, and more. These reports can highlight areas of concern that may lead to delays.
- Monitoring KPIs (Key Performance Indicators): KPIs help measure the efficiency of project execution. By monitoring KPIs such as task completion rate, time to task completion, and resource utilization, you can identify any deviations from the plan that could result in delays.
- Notifications and Reminders: Most project management tools have built-in notification systems that alert team members about upcoming deadlines. If a deadline is approaching and the task is not close to completion, it can serve as an early warning sign of a potential delay.
- Regular Team Meetings/Check-ins: Regular communication with your team can help identify any challenges or roadblocks they might face, providing an opportunity to address these issues before they cause significant delays.
Managing Project Delays
When a project delay is identified, managing it effectively to minimize its impact is crucial. Here are some steps to take to get a delayed project back on track:
- Acknowledge the Delay: The first step is acknowledging the delay and understanding its cause. This involves identifying which tasks are delayed and why.
- Reassess Project Timeline and Schedule: Once a delay has been identified, reassess the project timeline and schedule. Determine how the delay will affect the overall project timeline and whether any adjustments or modifications need to be made to the schedule.
- Use Project Management Software to Communicate Delays: Communication is key when managing project delays. Use your project management software to inform all stakeholders about the delay and the revised plans. Transparency helps manage expectations and keeps everyone on the same page.
- Develop a Recovery Plan: This could involve reallocating resources, reprioritizing tasks, or outsourcing certain activities. The goal is to devise a plan to help you catch up and get back on track.
- Implement Changes and Monitor Progress: After developing a recovery plan, implement the changes and closely monitor progress. Use your project management software to track whether the new measures are helping to reduce the delay.
- Learn from the Experience: Use every project delay as a learning opportunity. Analyze what went wrong and how it was handled to improve your project management processes in the future.
Mitigating Project Delays
To proactively avoid project delays, use strategies like comprehensive planning, risk management, regular monitoring, and clear communication with stakeholders. It's important to manage resources efficiently, assess changes in project scope carefully, and set realistic deadlines. Utilizing project management software can aid in scheduling, task management, and communication while actively engaging stakeholders throughout the project can provide valuable insights to prevent delays.
- Comprehensive Planning: Spend adequate time in the planning phase to outline clear objectives, scope, and timelines. A well-crafted plan can serve as a roadmap, helping to prevent delays.
- Risk Management: Identify potential risks and develop contingency plans to deal with them if they occur. This proactive approach can help reduce the impact of unexpected issues.
- Regular Monitoring and Tracking: Use project management software to monitor progress regularly. This helps identify any potential delays early, allowing for timely intervention.
- Effective Communication: Maintain open lines of communication with all stakeholders. Regular updates can ensure everyone is aligned on expectations and progress, reducing the chances of miscommunication-related delays.
- Resource Management: Ensure that you have adequate resources (both human and material) to complete the project on time. This may involve hiring additional staff, outsourcing certain tasks, or procuring necessary equipment in advance.
- Manage Scope Creep: Be vigilant about changes to the project scope. Any changes should be carefully assessed for their impact on the project timeline and approved only if necessary and manageable.
- Training and Skills Development: Equip your team with the necessary skills and knowledge to complete their tasks efficiently. This might involve providing training or investing in tools that can increase productivity.
- Set Realistic Deadlines: While it's important to be ambitious, unrealistic deadlines can lead to stress and eventual delays. Set achievable deadlines for tasks and milestones.
- Use Project Management Software: Tools like ActiveCollab can help with scheduling, task management, communication, and more, making it easier to manage projects and avoid delays.
- Stakeholder Engagement: Engage stakeholders throughout the project. Their input and feedback can provide valuable insights that can help avoid potential delays.
Learning from Project Delays
Project delays, while frustrating, can provide valuable lessons for improving future project planning and execution. Learn from these experiences and use them to improve and minimize future project delays.
- Analyze the Causes: The first step is to understand what caused the delay. Was it due to poor planning, resource constraints, unexpected changes, or something else? Identifying the root cause can help prevent similar issues in future projects.
- Post-Project Reviews - using Project Management Software like ActiveCollab to conduct post-project reviews. These reviews allow you to analyze various aspects of the project, including what went well, what didn't, and why.
- Document Lessons Learned: Document the lessons learned from the project delay. This could be a report or a database entry that can be referred back to when planning future projects.
- Incorporate Lessons into Future Planning and Execution: Use insights from analyzing project delays to improve your project management processes. This might involve enhancing your planning process, improving communication, investing in training, or better managing project risks.
- Share Insights with the Team: It's important to share the lessons learned with the entire project team. This ensures everyone is aware of what caused the delay and how to avoid similar issues in the future.
- Continuous Improvement: Consider project delays as part of a continuous improvement process. Regularly update your project management practices based on the lessons learned from past projects.
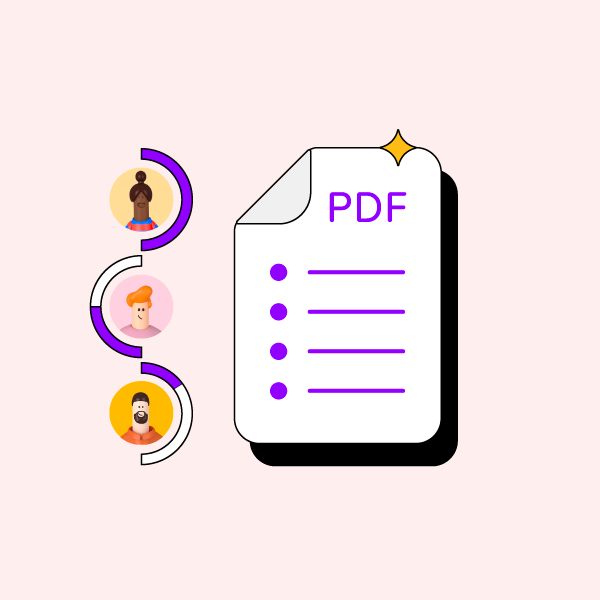
Types of Teams Cheat Sheet
All Newsletter subscribers can download this (and other) ActiveCollab Project Management Guides.
*Enter your email address and subscribe to our newsletter to get your hands on this, as well as many other free project management guides.
Sorry, we could not subscribe you at this moment. please double check your email address. If issue still persist, please let us know by sending an email to [email protected]
Make Real Work Happen!
Start your trial today, free for 14 days! Onboard your team, plan, collaborate, organize your work, and get paid.
By signing up you are agreeing to the ActiveCollab Terms of Service & Privacy Policy .
Great, just a few seconds and you're in.
We detected that you already have an ActiveCollab account
You can log in to existing account or you may start a new one
Great, your account has been created!
You will be redirected to your new account in a couple of seconds.
Sorry, we could not create an account for you at this moment.
Please double check your email address. If the issue still persists, please let us know by sending an email to [email protected]
Sign up for ActiveCollab newsletter!
Choose your favorite topics and we'll send our stories from the tech front lines straight to your inbox.
Unsubscribe at any time * Privacy Policy
Just a second
Thank you for subscribing to our newsletter.
Oops, something went wrong! Please try again later.
Related Articles
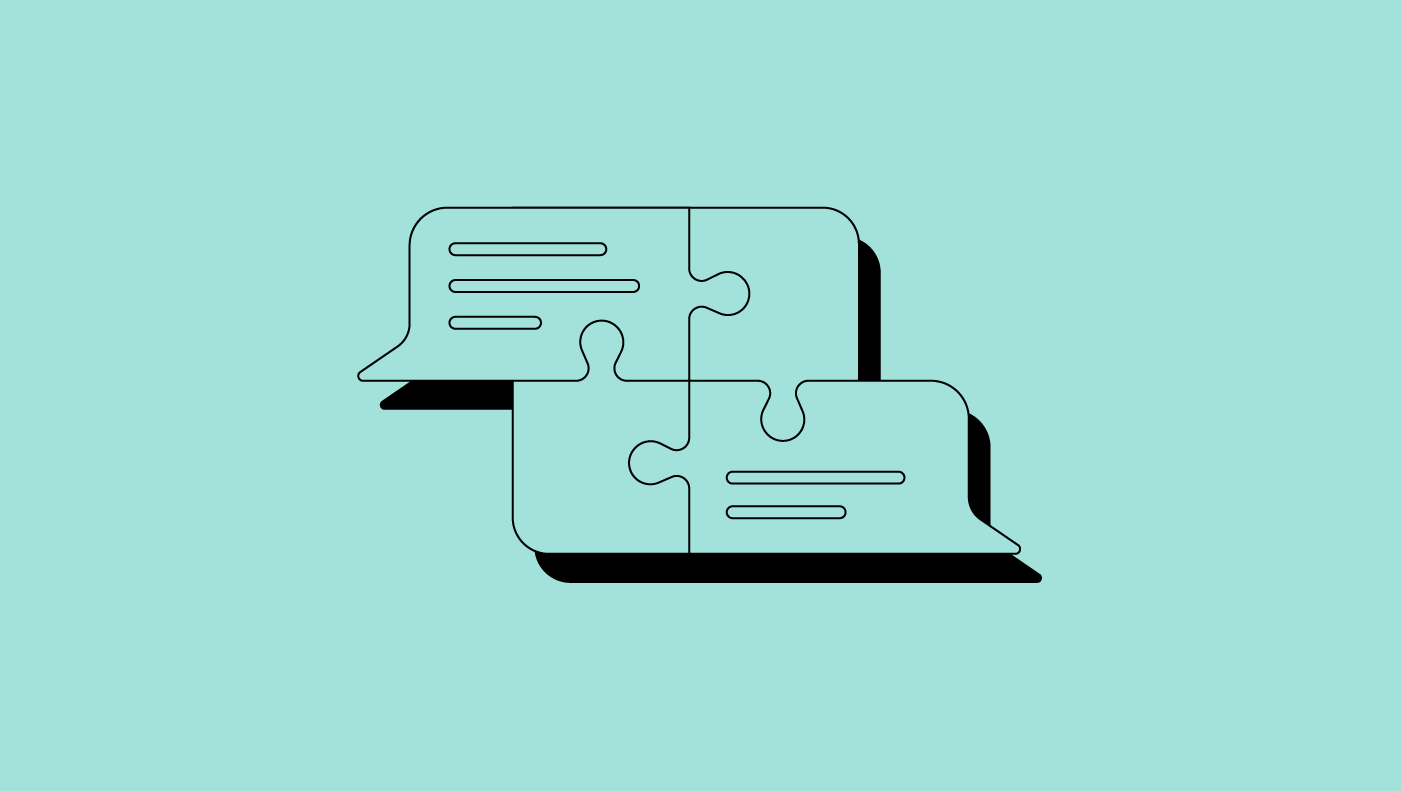
Key Points of Effective Team Communication - Teamwork
Start your free trial.
Enter your email to get 14 days of ActiveCollab absolutely free, without any limitations.
Mark as disposable account.
ActiveCollab Is Using Cookies
By accepting all cookies you are giving us permission to use our tracking technologies to personalize your content and provide you the best possible experience on our website. Essential cookies are always on as we need them to make sure our website is working properly.
Read more about our cookie policy.
Behind Schedule: Unravelling the Common Causes of Construction Delays
by Bart Kolosowski | Jun 15, 2023 | 0 comments
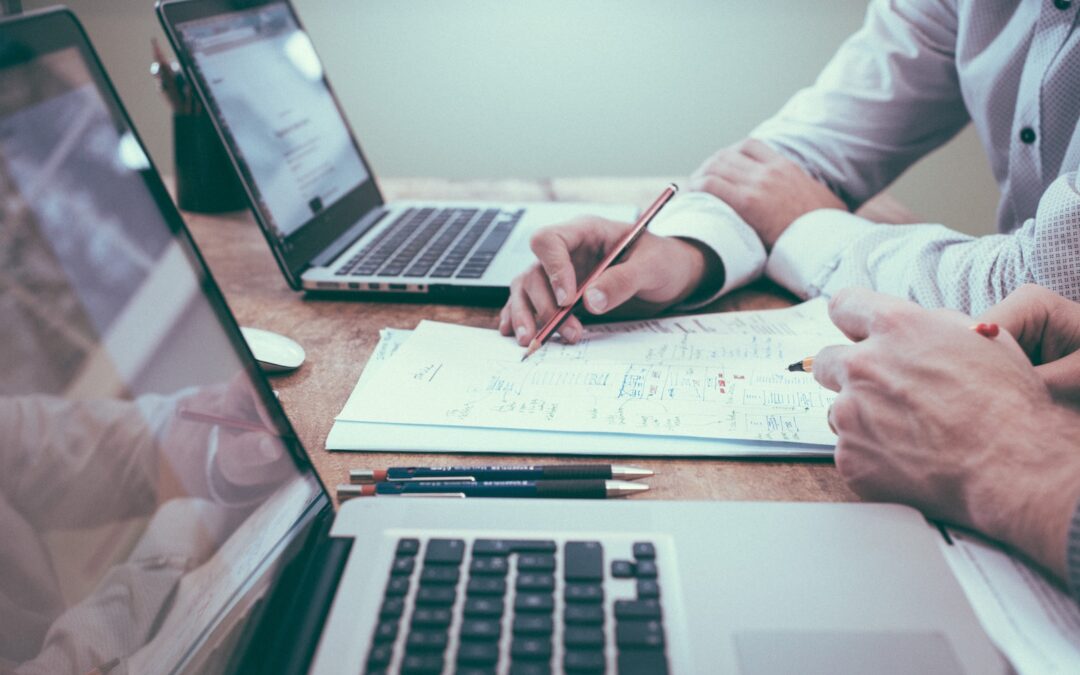
Welcome to our exploration of the timely delivery of construction projects in our blog post, “Behind Schedule: Unravelling the Common Causes of Construction Delays.” This article unpacks the importance of on-schedule project completion and delves into the common causes of construction delays, dividing them into those stemming from the client and their team and those caused by contractors. We then focus on strategies to mitigate the impacts of these delays, from a client’s perspective. By the end of this discussion, you’ll be equipped with a greater understanding of how to better navigate and manage construction delays, thereby ensuring a smoother path to project completion
Understanding the Significance of Timely Project Completion in Construction
Timely project completion plays a vital role in the construction industry, a fact that is keenly felt by clients and their professional teams. A construction project is a significant undertaking that involves a sizeable investment in time, resources, and funds. It is a dynamic process, carefully choreographed to complete a complex task within the constraints of time, budget, and quality.
The success of a construction project often hinges on a well-planned schedule. It’s important to note that there are two distinct types of schedules in the industry – those prepared by the contractors responsible for the physical execution of the work and those devised by the client’s team. The contractor’s programme focuses primarily on the sequence and timing of the build, while the client’s schedule takes a broader view, factoring in the planning, design and procurement activities, as well as milestones for funders and occupants. This multifaceted approach ensures that all parties are aligned and that the project advances smoothly towards its completion date.
The economic implications of project delays are far-reaching and can significantly impact the project’s viability. When construction lags, it often incurs additional costs and can decrease the projected return on investment (ROI). If the project is funded externally, delays could potentially lead to hefty penalties. Therefore, sticking to the planned schedule is not just about ticking boxes; it’s about protecting the financial health of the project.
Delays in construction projects ripple through all stakeholders. Clients may face extended periods of inconvenience or lost revenue, contractors may encounter increased costs or reputational damage, and workers and suppliers could suffer from disrupted schedules and payment issues.
Moreover, delays can directly affect the quality of the finished project and the safety of workers. Rushing to catch up to the original schedule might encourage corner-cutting or overworking, which can lead to inferior workmanship or an increase in on-site accidents.
Understanding the significance of timely project completion underscores the importance of efficient project management. Proactive management involves foreseeing potential bottlenecks, managing risks effectively, and having a robust plan to handle any unexpected delays. In this way, construction delays can be minimised or prevented, ensuring a more successful project outcome for all involved.
Unveiling the Common Construction Delays: An In-Depth Analysis
In order to develop a comprehensive understanding of the common construction delays, it is crucial to analyse them from two distinct perspectives – that of the client and their professional team, and the contractor. Each plays a crucial role in the construction process and, correspondingly, each has its unique set of potential delay causes.
Client and their team-related delays
Firstly, delays in the construction industry can frequently originate from design-related issues. Incomplete or unclear initial design briefs can cause confusion and miscommunication, leading to a slowdown of work as clarifications are sought. Further, late or frequent design changes, often stemming from evolving client requirements, can disrupt the workflow, requiring costly and time-consuming revisions. Moreover, errors or discrepancies in design documents can lead to incorrect work being undertaken and need to be rectified, adding to the project timeline.
Secondly, changes in the project scope, primarily initiated by the client or their professional team, are another significant contributor to construction delays. These alterations can necessitate a complete revision of the existing schedule, pushing back the completion date.
Thirdly, delays in decision-making by the client or their team can have a cascading effect on the project timeline. Approvals related to design, material choices, and other key project components often need to be given in a time-sensitive manner. Any delay in these decisions stalls the subsequent steps, thereby delaying the overall project.
The timely provision of necessary information or permissions can also influence the project schedule. For instance, delays in granting site access, obtaining requisite permissions, or providing essential project information can halt project progress and push the timeline out further.
Inadequate project management on the client’s side can cause significant delays in the construction process. Poor planning, ineffective communication, and a lack of coordination between different parties can disrupt the project workflow, leading to avoidable delays.
Lastly, financial issues also feature prominently in the common causes of construction delays. Delays in payments, underestimation of budgets, and any form of financial instability can disrupt the project timeline, leading to potential delays in project completion.
Contractor side-related delays
On the contractor side, supply chain delays are a prevalent issue. Late delivery of materials, unavailability of required materials, or issues with suppliers can stall project execution, causing significant delays.
Workforce-related delays also play a significant part in construction delays. The unavailability of skilled labour, low productivity levels, and internal disputes can disrupt the work schedule, delaying the overall project.
Unforeseen circumstances, including adverse weather conditions, accidents, or changes in regulations, can bring work to a sudden halt, pushing the completion date out further.
Finally, just like on the client’s side, financial issues can also lead to construction delays. The financial instability of contractors can cause interruptions in the workflow, further affecting project timelines.
In the next sections, we will explore the consequences of these common construction delays and discuss strategies to prevent them.
Mitigating the Impact of Common Construction Delays: A Client-Centric Approach
In the fast-paced world of construction, time is of the essence and delays can have a significant impact on the overall project outcome, both financially and operationally. Consequently, adopting a proactive approach, particularly from the client’s perspective, can make a substantial difference in mitigating common construction delays.
The foundation of successful project execution lies in the early engagement of the professional team. An experienced team, brought together at the start of the project, can navigate potential pitfalls and bring their collective knowledge to preemptively address common causes of delay. This not only enhances the project’s chances of success but also facilitates informed decision-making at every stage of the project.
Undoubtedly, one of the essential elements in preventing delays is a clear and thorough project brief. A well-articulated vision and specific objectives, underpinned by detailed site investigations and design strategies, create a robust framework within which the project can evolve. A clear brief also aligns expectations, thus ensuring the design aligns with the client’s budget and project aspirations.
Transparent and regular communication acts as the lifeblood of a well-executed project. It’s pivotal in anticipating potential issues and addressing them promptly. Regular design team meetings and client consultations encourage collaborative problem-solving, promote swift resolution of design issues, and keep everyone apprised of project developments.
Equally important is the emphasis on continual cost and project management from the project’s inception. The practice of preparing and maintaining a realistic budget and a detailed project programme, along with diligent tracking of design changes and their implications, not only aids in managing costs but also assists in identifying potential causes of delay before they escalate.
When it comes to preventing delays during the construction phase, the value of a well-organised pre-tender process is not to be underestimated. Detailed tender documents set clear expectations and provide the basis for an accurate contract sum, eliminating ambiguities that might later result in disputes and delays. A rushed tendering process, on the other hand, can lead to numerous issues down the line, from incomplete construction information to unrealistically low tender returns, both causing significant delays in project execution.
While much of this discussion has centred on client-side delays, it is important to note that clients also have a role to play in mitigating contractor-side delays. A thorough tender process, diligent contract administration, prompt issuing of instructions and addressing site queries can go a long way in preventing unnecessary delays on site.
In conclusion, mitigating the impact of common construction delays requires a blend of meticulous planning, regular monitoring, effective communication and competent contract management. By adopting a proactive and client-centric approach, it is possible to minimise disruptions, maintain project momentum, and ultimately ensure the successful and timely completion of your construction project.
Submit a Comment Cancel reply
Your email address will not be published. Required fields are marked *
Save my name, email, and website in this browser for the next time I comment.
This site is protected by reCAPTCHA and the Google Privacy Policy and Terms of Service apply.
Recent Posts
- Top 10 Costly Mistakes to Avoid in Construction Projects
- What do the limitations of the government’s plan to reach net zero mean for the construction industry?
- The rate of inflation in the construction industry
- How cloud computing is transforming the construction industry
- What the latest government budget means for you
Recent Comments
- Our Services
- Learning Centre
- Supercharge My Project
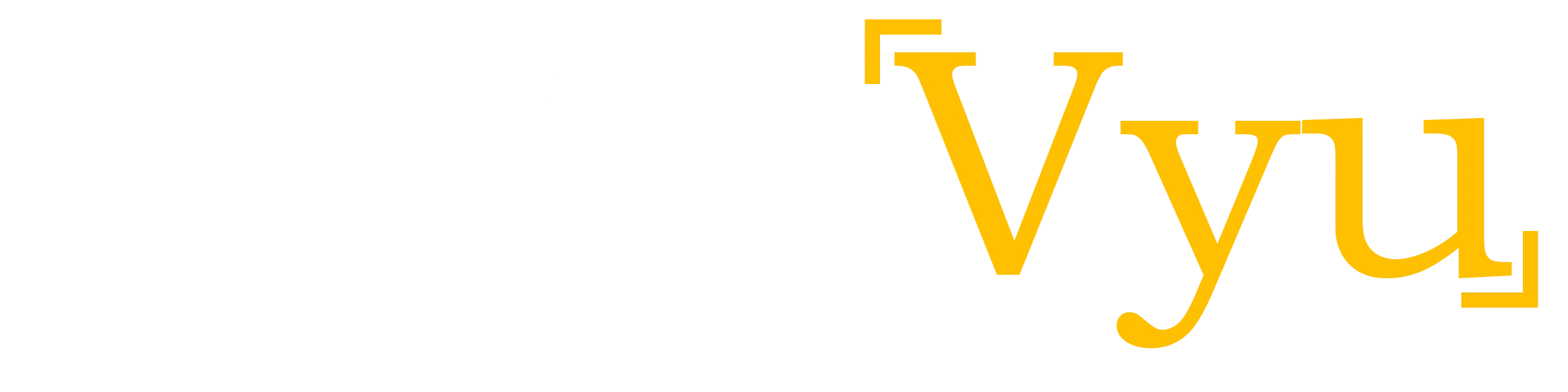
- April 13, 2023
- Construction Planning / Construction Project / Construction Technology
Top 10 Reasons & Causes of Delay in Construction Projects
According to a survey conducted by KPMG , 70% of construction projects experience cost overruns and delays. In addition, the same study found that 60% of construction projects exceed their planned timelines. These delays and cost overruns can have a significant impact on the project budget, schedule, and overall success.
To address these issues, many construction companies are turning to technology and data-driven solutions to improve project management and mitigate delays and cost overruns. With the help of artificial intelligence, machine learning, and other tools, construction companies can improve scheduling, resource allocation, and risk management, leading to more successful and efficient projects.
Delay In Construction Projects
Delay in construction projects is a significant issue faced by the industry. A delay can be defined as any event that extends the project’s original completion date beyond the expected or planned time. Construction delays can result from various factors such as design changes, unforeseen site conditions, weather conditions, labor shortage and availability, equipment breakdowns, and maintenance, permitting and regulatory issues, communication breakdowns, and contractor and subcontractor disputes.
The impact of delays can be severe, leading to cost overruns, lost revenue, and damage to reputation. According to a report by McKinsey, construction projects often take 20% longer to complete than scheduled, and around 80% of projects experience some delay. These delays can add up to significant costs for the industry, with the same report estimating that the global construction industry could save up to $1.6 trillion annually by reducing project delays and improving productivity.
What are the Types of Construction Project Delays?
Before going deep into the causes of construction project delays, understand the type of construction project delays
- Delays resulting from natural causes
- Delays that are the fault of the client
- Delays that are the fault of the contractor
Causes of Delays in Construction Projects
Knowing the cause of project delay can help build a counter strategy. Here are some most common causes of delay in construction projects.
- Inadequate Planning
- Lack of Communication Between Team Members
- Inefficient Material Management
- Equipment Failure
- Poor Weather
- Project Complexity
- Design Variation
- Ineffective Resource Management & Labor Challenges
- Construction Implementation Failure
- Use of obsolete project management tools and technologies.
1. Inadequate Planning and Site Management
Planning help define the goals of a project clearly and impacts its outcome. As construction is a long process and involves the contribution of many professionals, a project manager has to plan everything smoothly to get the maximum result. The project manager is responsible for all the professionals working together and resources readily available to avoid delays.
2. Lack of Communication Between Team Members
Unrelated to the contractor, the client may instruct to stop working because of their design change, unsafe working conditions, or to allow their work, or their contractor’s work, to continue. If the contractor is compliant, they can claim an extension of time unless they can prove that the client (or their representative) was wrong to stop the work.
3. Inefficient Material Management
Shortage or improper supply of materials plays a significant role in construction project delay. Inefficient material management either results in supply shortage or oversupply. The scarcity of materials can negatively impact the construction process, causing lengthy delays and additional costs. Also, other issues are related to reordering the material, such as color inconsistency and size tolerance.
4. Equipment Failure
Construction firms are incorporating technologically advanced equipment for faster completion of work. Such equipment equally increases the importance of maintenance planning for onsite machinery and technology. Equipment failure or improper equipment management directly causes construction delays.
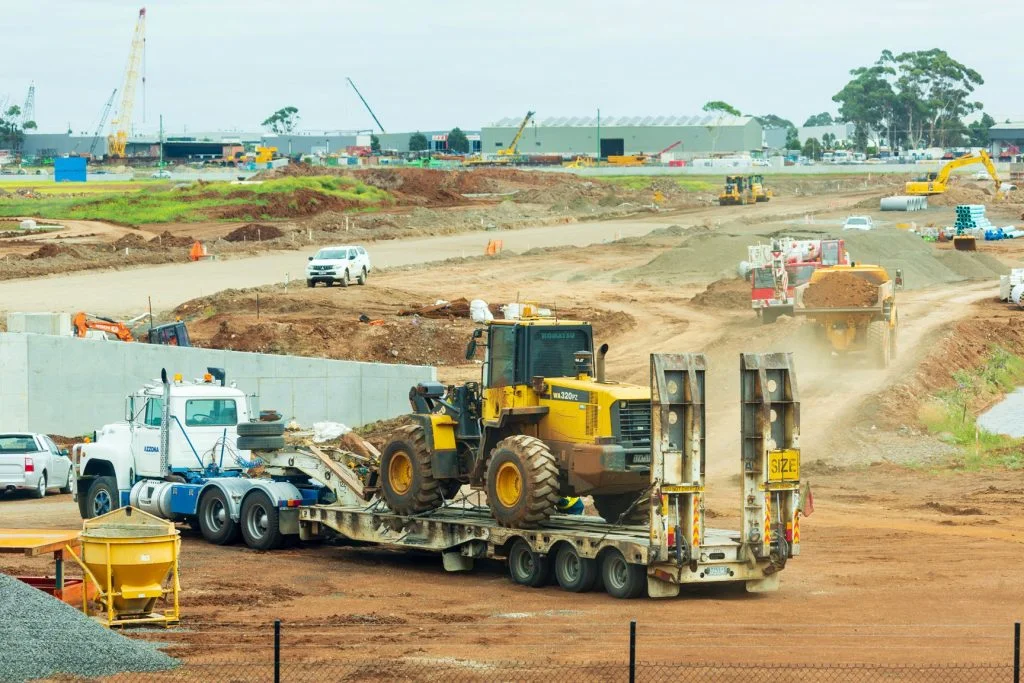
5. Poor Weather
The delay caused by poor weather conditions is outside the control of the contractor and project team. This natural delay has a deep impact on project management and delivery. Responsibilities for construction delay due to poor weather depends on project to project and contract to contract. Typically, contractors will be granted an extension of time and, in some cases, loss and expense if construction delays are caused by exceptionally adverse weather.
6. Project Complexity
The project complexity is generally related to the scale of the project. Most mega construction projects (nuclear power stations, skyscrapers, etc.) have a comparatively lengthy execution duration compared to small construction projects.
Consequently, the initial budget proposed/allocated may need to be supplemented because of changes in material prices, exchange rates, and inflation rates.
The construction project might take longer as a result of increased costs and long negotiations.
Complex projects also require complex plans, schedules, and estimations.
7. Design Variation
The blueprint to obtain an accurate representation of the employer’s demand and better technical input for project execution is usually resolved based on the project design and specifications.
During the project’s execution, faulty designs lead to inaccurate or insufficient deliverables.
Faulty design/design variation will lead to the incorrect technique application to achieve successful results. Attempts to correct these design errors later in the project will result in a time delay and a cost overrun during the execution section.
Secondly, if the design is changed at a later stage, all costs, time, and quality estimates will be affected.
8. Ineffective Resource Management & Labor Challenges
The construction project is the long duration careful coordination of a lot of resources toward the timely completion of the project. Tracking and managing the people and equipment can be difficult. When a single resource is not in place or on time will result in a lack of productivity and project delay. It is the main reason why resource management issues cause a delay to the company.
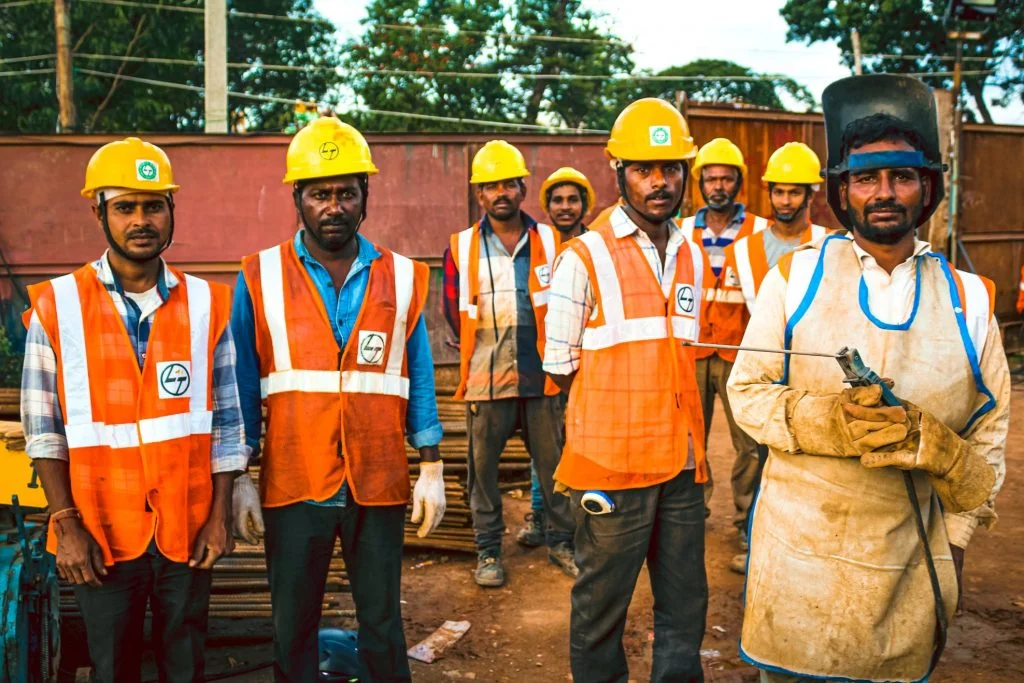
9. Construction Implementation Failure
Here, construction project failure is fine with construction implementation failure. Construction implementation failure includes procedure implementation failure. Not only planning but execution is also equally important. Failure to execute a process/activity also causes a delay to the project timeline as it needs more time to redo the work. Implementation failure may be caused by the communication gap, non-skilled/less skilled workers, or resource availability.
10. Use of obsolete project management tools and technologies
The expanding size and complexity of the project are still the project manager’s concern. Determining the main causes of delays in large construction projects is difficult and often results in disputes over responsibility. One of the main causes of such delays is using obsolete project management tools and technologies. Old technology and tools are not efficient enough to complete such large construction projects on the scheduled time.
Impact of OpticVyu Technology
OpticVyu is pleased to help hundreds of companies in multiple countries to mitigate the causes of delays in construction projects. OpticVyu has developed a monitoring solution that any type and size of the firm can use to monitor construction projects. The below statements can help you understand how OpticVyu is effective in mitigating the causes of construction project delays:
- Pre-construction planning involves surveying land and other activities. Drone mapping and surveying by OpticVyu is the best alternative to old surveying techniques. Also, time-lapse camera monitoring can aid your pre-construction planning with ease, precision, and in economical way.
- The communication gap between the project manager, team, and stakeholders directly results in project delay. OpticVyu’s multi-user access, time-lapse & reports sharing option allows the project managers to keep everyone updated on the project’s progress and send details to the team for an update before it is late.
- Delays due to inefficient material handling are the common cause and can only be resolved with an effective material management technique or tool. OpticVyu offers free material tracking and management solution with a time-lapse monitoring solution.
- Project delays are often associated with a lack of transparency in the interior work. The interior works can be efficiently managed by the OpticVyu 360° Interior Monitoring Solution which enables not only capturing the 360° images & mapping them on layouts but also creating the snag list & task list assigned to respective team members thereby creating a project collaboration center for everyone to act fast & reduce delays.
- Poor working conditions like air pollution keep pushing the project schedule dates. Stakeholders only stretch the project deadlines if the delay is non-resolvable (weather conditions). OpticVyu’s Air Quality Detection module provides the proper AQI reports, which you can use as evidence of non-resolvable delays.
- BIM integration with the dashboard allows you to compare the project progress with the planned design. It is a helpful tool to define and rectify variations in the actual progress & planned progress.
- OpticVyu has also created an AI-based image processing module to minimize safety hazards, track vehicles & see active working durations that eventually reduce project delay.
Causes of Delay in Construction Completion – [Infographic]
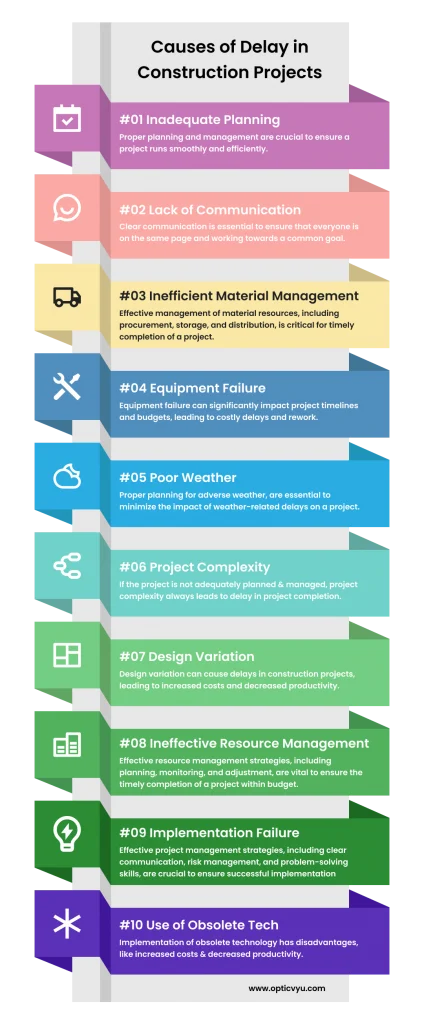
Are you a project owner/project manager? Want to monitor your project site with more ease remotely from your desk? Contact our experts today.
Newsletter: Exclusive Updates
Enter your email address below and subscribe to our newsletter
Related Posts
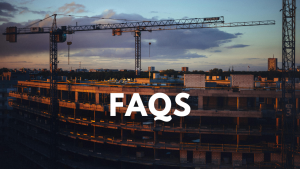
Answering Time-lapse Construction Camera Questions with OpticVyu
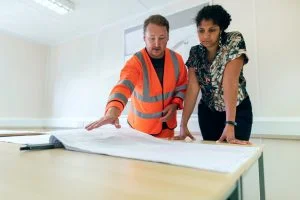
Top 10 Construction Project Management Challenges
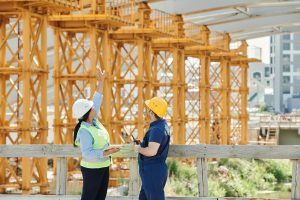
Future Trends in Construction Monitoring: What to Expect
Trending now.
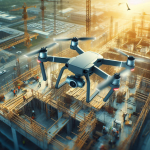
- Received a document?
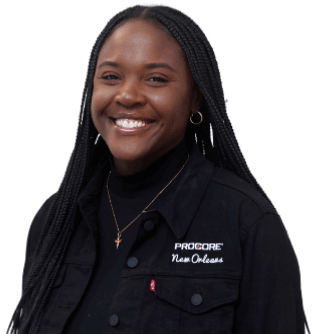
Schedule Delay: How to Assess & Reduce Impact in Construction
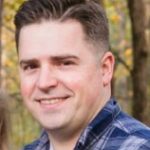
162 articles
Change Orders , Construction Contract
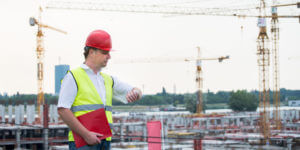
Anyone in the construction trade knows that schedule delays are part of the gig. In fact, 80 percent of construction businesses expect delays on at least some, if not all, of their projects. The Levelset 2020 Report states that one out of every three contractors finishes their projects on time.
While a career batting average of 0.333 will secure your spot in the baseball hall of fame, it’s not so great when it comes to delivering construction projects on time .
The ironic part about project delays is, according to the Levelset 2020 Report, 70 percent of contractors blame poor jobsite coordination for these schedule delays. If that’s true, it means that many delays are avoidable, and affected parties should receive compensation, right?
Let’s take a look at what the different types of schedule delays are, as well as how you can handle them.
Table of Contents
The 4 types of schedule delays
There are essentially four types of scheduling delays, and they affect the project and parties on the project differently. The approach to handling them can also vary.
When a delay occurs, you need to determine what type of delay it is and how it will affect the project. While a situation might seem like one type of delay, it could actually fall under two or three. So, don’t underestimate how complex or disruptive a delay can be.
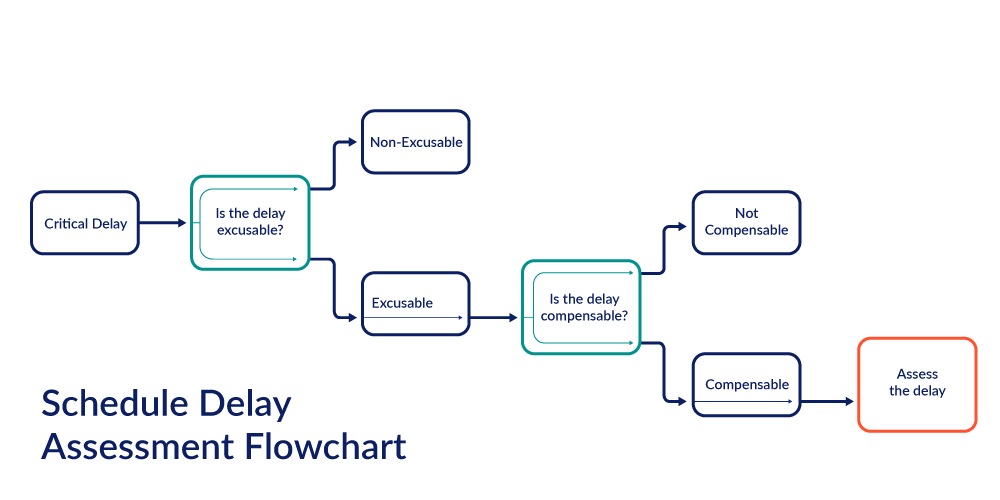
Critical delays
When determining the type of delay you’re dealing with, the first thing you need to consider is if it’s a critical delay.
If a delay affects the project’s completion date, it’s a critical delay . A delay that affects important milestones on the project (which always have the potential to affect the project completion date) can also be a critical delay.
By their nature, you can’t make up for critical delays. Skilled management can minimize the long-term effects, but you can’t completely absorb the delay elsewhere in the project.
The main factor determining whether a delay is critical is if it affects any of the waypoints set by the Critical Path Method (CPM). If a delay prevents or delays reaching any of the CPM milestones, you’ve got a critical delay on your hands.
If you compare your schedule delay against the CPM and there are no changes, you’re dealing with a non-critical delay .
Excusable delays
Once you determine the effect that the delay will have on the project’s timeline, it’s time to assign some blame (well, not really). Rather than jumping straight to laying blame, you need to determine whether the delay is excusable or not.
If your new timeline results from something outside of the contractor’s scope or control, it’s excusable . You can’t hold someone responsible for an aspect of the project that they simply cannot control.
Excusable delays can include things like dangerous or impending weather conditions, customer or owner change orders , hidden issues with the property, or errors in the project specs.
If your analysis determines the delay to be excusable, there should be some compensation or allowance. The deadline might extend to absorb the delay’s effects, or additional funds might be in order — you can’t expect someone to work for free.
On the other hand, inexcusable delays are a whole other animal: These delays are definitely someone’s fault. Whether it’s a sub’s fault for not ordering materials on time, poor planning on the part of the GC, or faulty craftsmanship somewhere in the project, someone specific is to blame.
Compensable delays
While you’re sorting through the delay, you have to determine if someone should receive compensation. Compensation can come in the form of more time, more money, or both.
If the delay affects a party, and that party has nothing to do with causing the delay, it’s likely compensable for that specific party . If the drywallers have to wait because the subcontractor responsible for order insulation made a mistake, the drywallers should receive compensation in the form of a longer deadline (at the least).
In this case, the drywaller’s delay is compensable, but the delay of the sub responsible for the insulation is not — the delay of the sub responsible is also inexcusable.
So what’s the takeaway here? If a delay is excusable, it’s likely compensable too . If it’s inexcusable, it’s probably not compensable.
Concurrent delays
Concurrent delays and their effects are where things get particularly cloudy. Concurrent delays occur when two or more delays occur on a project. These two delays don’t need to occur at exactly the same time but instead happen within a particular window, overlapping each other. They can even be a defense against delay claims .
Think about it this way:
There are two delays, Delay A and Delay B. They’re both critical delays, so they both affect the scheduled completion date. If Delay A occurs and sees resolution, and then Delay B occurs, then they are separate delays. However, if Delay B occurs before Delay A sees resolution, they are concurrent delays.
In this case, the resolution would mean that the delay’s effects are already determined and accounted for.
Concurrent delays can compound the issue, and they’re very difficult to sort through. Determining if either, or both, are compensable or excusable can be extremely challenging.
The good news is, that CSI marathon you binged on over the weekend might not be a complete waste: You’ll probably have to conduct an in-depth analysis to determine what’s what.
Examples of schedule delays
Schedule delays are a lot like snowflakes: No two are exactly alike. There are many ways that a project’s schedule can go sideways.
However, there are some common delays to familiarize yourself with.
Weather delays
Avoiding bad jokes about weathermen always being wrong, the reality is that you simply cannot plan for the weather. Sure, you can tailor your project to start in the spring and end in the fall, but a lot of bad weather that can result in long construction delays can happen in that window.
According to census.gov , the average time to build a single-family home in 2019 was 11.1 months. Just a week of bad weather can throw a project’s entire timeline off — that’s only seven bad days out of over 300.
Budget delays
Budget delays can bring a project to a complete standstill. Whether it’s because the contractor misquoted the estimate, or the owner can’t secure financing, there can be major delays.
Labor scheduling
Construction coordination isn’t always straightforward. A subcontractor managing several projects at once can lead to light crews and delayed timelines.
Lack of communication
Communication is crucial to any construction project . Communication between subs, site management, and the owner is absolutely key for a successful project. Without the proper channels to follow, issues that come up can go unreported or unnoticed. They’ll compound into much larger problems that cause delays.
Site coordination
54 percent of contractors blame delays on poor coordination between subcontractors. The reality is that at some point, most subs’ time on a project consists of sitting around, waiting for another contractor to finish their job — or, worse, waiting on the GC for an approval — before they can proceed.
This downtime adds up into an inefficiency-snowball, tacking days and weeks onto the project. Better coordination and communication can lead to less downtime and faster approvals.
Pandemics
Some delays are entirely out of everyone’s hands, and pandemics are one of them. COVID-19’s effect on the construction industry continues to mount.
At one point, the majority of projects were on hold in some parts of the country. Once sites reopened, labor and materials shortages continue to plague projects, extending their schedules.
5 tips to minimize the effect of construction delays
Regardless of the type of delay you’re dealing with and who’s to “blame,” a delay needs a resolution. Handling schedule delays correctly can make the difference between minimizing their effect and letting the schedule spiral out of control.
1. Set realistic expectations
Setting an unrealistic deadline or budget doesn’t do anyone any good. While no one will fault you for being a go-getter, setting a deadline you know will be difficult to meet is setting your project up for failure (or at least a missed deadline).
When you’re running full speed, the slightest slip can cost you your footing. Instead of pushing yourself and your crews at redline, set up realistic goals and timelines that you can both reach , allowing some room to absorb small delays along the way.
2. Update the construction contract
Your contract can help or hurt you in the event of a schedule delay. Be sure to set it up to help by including the common excusable delays in your contract. Be sure they include a force majeure clause , as so many have realized the benefits of one recently.
If there’s one thing to avoid in your contract, it’s a No Damage for Delay clause , which can mean you won’t see any compensation for any delay, excusable or otherwise .
Also, you should outline any changes along the way in by using change orders . A change order essentially acts as the new contract after a change like a delay.
3. Watch your lien & notice deadlines
Schedule delays don’t just affect the flow of work; they can very easily impact payments to contractors, subs, and suppliers on the job, too. If a project delay is causing a payment delay, keep a close eye on your state’s mechanics lien rules .
Each state has deadlines for sending notice and/or filing a mechanics lien . Miss the deadline and you could lose one of the most powerful tools in your payment toolbox.

Protect & speed up every payment
Learn how Levelset can help you easily manage your lien rights on every project to ensure your payments are always protected.
4. Encourage collaboration and transparency
Creating a jobsite atmosphere where subcontractors are comfortable reporting issues to site management can go a long way toward avoiding significant project delays. By creating channels for communication, you’ll create a collaborative and transparent environment where everyone works together to address problems.
The opposite of this environment is a scenario where subs feel like they need to hide issues or handle issues by themselves. This can lead to bigger problems that fall outside of their limited scope, becoming widespread delays.
5. Negotiate
We’ve already established that delays will probably happen on a project. Once you accept that, you can think objectively and come to a creative resolution. Sometimes that creative resolution requires a scheduling adjustment. Other times, creativity might mean adjusting payment terms or amounts.
When you’re willing to negotiate over the terms of a delay, you’re able to minimize its effects on the project and solve it quickly.
Ask an expert for free
I’m a contractor that was hired to do a remodel. I completed most of the work then the owner saw that the project still needed more work so they requested a change order. Work was done they didn’t want to pay change orders. I have emails and text...
I was working a residential bathroom remodel, the contract was for 22627.01, including tile cost when selected and with change orders and additional work, verified through emails and verbal change orders the total became 27752.78, I was paid intermittently total of 13000. when it came to 1 more...
I am a subcontractor, we have completed our scope of work per the contract signed. The GC held 10% as retention. I need to bill the retention, I have $23,000 in extra work that hasn't been billed because the GC has to issue a written change order first....
Tom Scalisi
View Profile
About the author
Recommended for you
Lien waiver vs. lien release: what’s the difference.
Lien waivers and lien releases are completely different documents (even though they are often confused by the construction industry). Read...
What Is a Work in Progress Schedule? | Construction Accounting
The Work In Progress (WIP) schedule is an accounting schedule that's a component of a company's balance sheet. It's calculated...
What are the Certified Payroll Requirements for Federal Construction Jobs?
What does Certified Payroll mean? This post covers the certified payroll requirements for contractors working on federal construction projects.
6 Construction Project Delivery Methods Compared
The steps required in a project’s journey to completion are importation to how successful the project will be. That’s why...
What Are “Back Charges” in Construction?
Back charges can be tricky if you're not careful! It's incredibly important to prioritize communication and documentation when back charges...
What Is a Notice of Completion?
What is a Notice of Completion? As anyone reading this surely knows, the construction industry loves its documents! There's a...
Guide to Alternative Dispute Resolution (ADR) in Construction
With a proper dispute resolution clause in place, contractors, subs, and suppliers can avoid taking their disputes into litigation.
What Is Underbilling? | Construction Industry Accounting
Underbilling occurs when a contractor does not bill for all the labor and materials delivered in a billing cycle. It...
- Login / Register
- Subscribe -->
- You are here: Latest
Delays to large-scale construction projects more than double since start of pandemic
12 Jan, 2022 By Rob Horgan
Delays to large-scale construction projects have more than doubled during the Covid-19 pandemic, according to new data released today by nPlan.
Research by machine learning startup nPlan found that the median delay for projects completed before the pandemic was approximately 100 days, while pandemic-era projects have a median delay of more than 200 days.
These figures have been compiled by amassing a dataset of more than 500,000 construction schedules provided by clients and contractors including Network Rail, Shell, Kier and Google.
Analysis of pre- and mid-pandemic projects in the nPlan schedule dataset suggests that nearly nine in 10 large-scale construction projects (85.5%) are delivered late; nearly two-thirds of them (59.4%) by at least two months.
Meanwhile, nearly a quarter of projects (22.7%) are delivered more than 250 days late, and more than one in 10 (13.4%) are delayed by at least a year.
nPlan chief executive Dev Amratia said: “In construction, as in so many other sectors and areas of public life, the pandemic hasn’t just created new problems, it has highlighted and exacerbated existing problems - in this case the costly project overruns which are endemic to the industry.
“Because this issue was not dealt with before the pandemic, we are now in a situation where projects have suddenly become much riskier.
“This will pile pressure on contractors and may mean clients bring forward fewer projects. On the other hand, the salience the pandemic has given this issue means we now have an unparalleled opportunity to get better at anticipating and preventing project overruns using advanced forecasting and risk management techniques.”
Cost hikes and time overruns have been recorded on some of the country’s biggest construction and engineering projects in the last two years.
Earlier this week, Crossrail Ltd revealed that shutting down construction sites during the first lockdown cost £13M.
Meanwhile, Speaking at NCE’s Tunnelling Festival in December, Tideway chief executive Andy Mitchell revealed that decisions made in the first three months of the Covid-19 pandemic cost the Super Sewer project promoter around £100M.
According to Amratia, the majority of construction projects that fail to complete on time have been hampered by poor forecasting and risk management.
He claims that one of the most effective ways to solve these problems is to remove human bias from the planning process:
“Time and time again we see forecasts marked by optimism bias, and risk management skewed by availability bias - that’s why we’ve developed a machine learning engine which turns our customers’ historical schedule data into a model which reflects the way they actually deliver projects.
“This unbiased model is then used to create super-accurate forecasts and discover risks and opportunities which would have remained hidden during the traditional planning process. This leaves planners free to get on with the important work of actually mitigating the risks and seizing the opportunities flagged by our system.”
Like what you've read? To receive New Civil Engineer's daily and weekly newsletters click here.
- Add to Bookmarks
Tagged with: nPlan
Related articles
Have your say.
Sign in or Register a new account to join the discussion.
VERTEX uses cookies to make our website work properly and to provide the most relevant content and services to our clients and site visitors. View our Privacy Policy .
At VERTEX, We Care
Learn why our culture, projects and people attract and retain the best in the industry.
About VERTEX
- Our Affiliate Companies
- VERTEX Gives Back
- Lifetime of Learning
- Diversity, Equity, & Inclusion
- Health and Safety
- Awards & Accolades
Featured Article
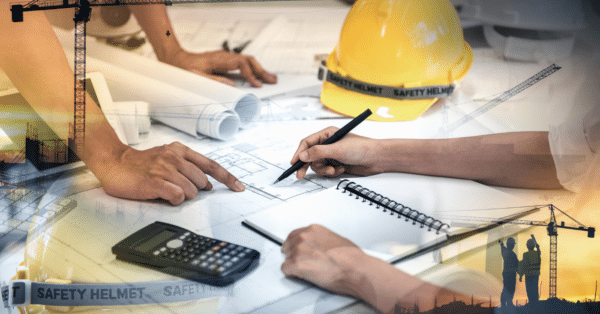
VERTEX Begins Project #90,000
VERTEX has Experts that Talk the Talk and Walk the Walk.
Unlike others, VERTEX provides forensic consulting alongside traditional AEC services which allows for a 360 degree view of your project.
VERTEX Services
- Expert Witness & Dispute Resolution
- Engineering
- Environmental
- Project Advisory
- Structural & Building Design
- Civil & Land Development
- Transportation & Infrastructure
- Building Envelope Consulting
- Building Assessment
- Building Commissioning
- Landscape Architecture
- Fire Protection and Life Safety
- Construction Management
- Owner’s Representation
- Owner’s Project Management
- Program Management
- Construction Monitoring
- Distressed Project Services
- Cost Management & Cost Estimating
- Construction Inspections
- Restoration and Tenant Improvements (RTI)
- Market Research & Real Estate Economics
- Due Diligence & PCA
- Industrial Hygiene & Building Sciences
- Environmental, Social & Governance (ESG)
- Environmental Compliance & Engineering Design
- Remediation Management & Development Consulting
- Environmental Loss Control Consulting
- Environmental Health & Safety
- Surety Claims Consulting
Construction Claims Consulting
- Environmental Claims Consulting
- Forensic Engineering
- Forensic Cost Engineering
- Forensic Architecture
- Forensic Accounting and Fraud Investigations
- Forensic Fire & Life Safety Claims
- Insurance Appraisal Consulting
- Builder’s Risk and Delay in Start Up (DSU) Insurance Consulting
- Subcontractor Default Insurance Claims Consulting
- Standard of Care
- Commercial Damages
- Construction Damages
- Government Contracts
- Property Condition Assessments
- Balcony Assurance
- Energy Disclosure Services
- Construction Quality Assurance
- Construction Loss Control Consulting
- Construction Health & Safety
- Contractor Termination
- Architectural & Building Envelope
- Heavy Civil
- Geotechnical
- Construction Safety
- CPM Scheduling Expert
- Acceleration
- Productivity
- Intellectual Property
- Business Valuation
- Class Actions
- Insurance Disputes
- Business Interruption & Lost Profits
- Cost of Repair and Fault Allocation
- DSC – Changed Conditions
- Added Scope
- Air Quality
- Demolition/Abatement
- Hazardous Waste
- Building Safety
- Design and Fire Protection Modeling
- Emergency Response Plans
- State of the Industry 2023
- State of the Industry 2022
- State of the Industry 2021
- State of the Industry 2020
- State of the Industry 2019
- State of the Industry 2018
CLIENTS & INDUSTRIES SERVED
VERTEX delivers innovative solutions on complex projects globally.
We work for a multitude of industries and markets, always providing value-added solutions and urgently responsive service.
VERTEX Clients & Industries
- Attorneys & Law Firms
- Aviation and Airports
- Commercial Tenants
- Financial Institutions
- Higher Education Institutional Investors & Owners
- Hospitals and Healthcare Industry
- Industrials
- Insurance Carriers & TPAs
- Oil and Gas
- Property Managers and HOAs
- Public Agencies
- Power Generation
- Real Estate Owners & REITs
- Surety Providers
Featured Project
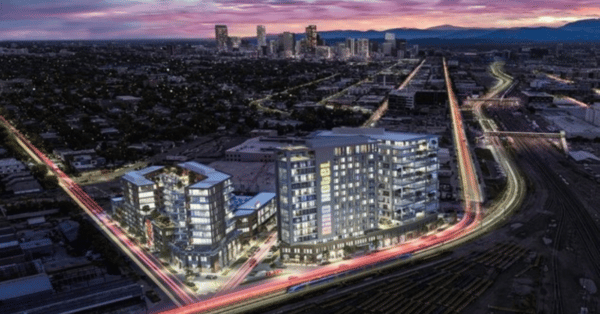
Environmental Consulting during Redevelopment of Commercial-Industrial Property in Denver
Need an expert for your case?
Our forensics experts work alongside AEC specialists which enhances our skills and bolsters the credibility of our expert consultants.
Find an Expert
- Expert Witness & Dispute Resolution Services
- Forensic Consulting Services
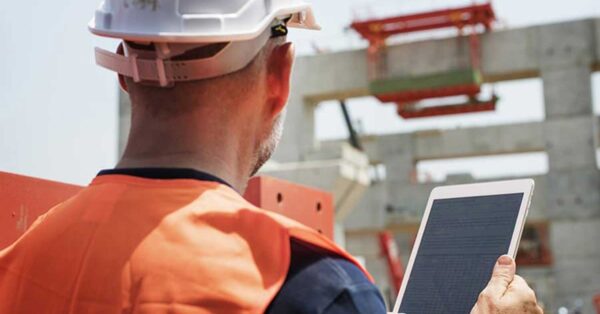
Best Documentation Practices to Mitigate Risk
Since 1995, VERTEX has completed over 90,000 projects.
View Portfolio
- Forensic Consulting
- Construction Project Advisory
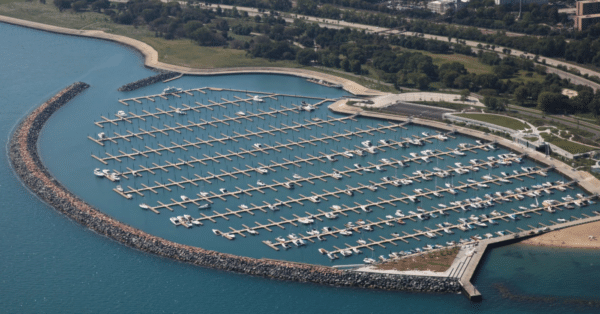
Breakwater and Other Harbor Improvements
VERTEX believes in a Lifetime of Learning philosophy.
Stay current with our industry experts as they share their insights and knowledge on the built environment.
View Insights
- Economic Analysis
- Education / Training
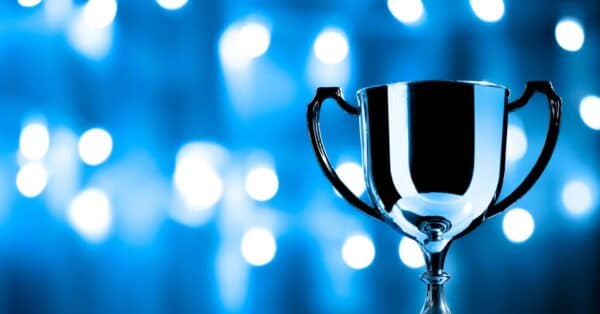
VERTEX Receives Award by Environmental Business Journal
Grow Your Career
Join Our Team
VERTEX is looking for talented individuals to join a highly technical team of forensic consultants, design engineers, construction managers, and environmental scientists.
- View Open Positions
Career Progression Program
- Meet the People Behind Our Success
Why VERTEX?
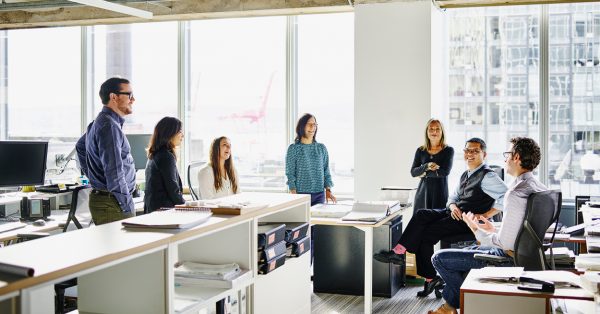
Have a question or want to speak with a technical professional?
VERTEX is a multi-discipline firm with global coverage. Our international network of resources enables us to provide multi-national clients with the most qualified local professionals who understand the culture, language, and regulatory framework.
Call Us: 888.298.5162
- General Inquiry
- Work Request
- Need an Expert?
Call us at 888.298.5162 .

Mitigating Construction Delays: Acceleration and Recovery Schedules
May 6, 2021.
When construction delays to the anticipated pace and progress of a project occur, it can become necessary to counteract the negative impacts to the schedule and “recover” time lost. Likewise, a schedule may need to be shortened to achieve completion at an earlier date. In both scenarios, acceleration – an initiative to increase efforts to complete performance at a faster pace than originally anticipated, despite excusable delay – may be applied.
In this article, we will look at:
- Acceleration scenarios
- Cost recovery options
- Application methods
- Key factors in using acceleration methods successfully
Three Acceleration Scenarios
Acceleration may happen on a construction project under three basic scenarios:
1. Voluntary Acceleration
This occurs when the contractor makes up for time lost due to non-excusable critical path delays for which they are responsible. Consequently, voluntary acceleration is rarely the subject of construction claims or disputes as almost all contracts include a “time is of the essence” clause. Thus, the increased cost and risk of acceleration are generally used to offset the risk of a larger financial impact – and the costs are absorbed by the contractor.
2. Directed Acceleration
Directed acceleration occurs when it can be demonstrated in the project record that the contractor is ordered – typically by the owner – to accelerate a scope of work. Ideally, there is an understanding that, with direction, compensation will be made for these efforts in the form of a change order. However, the responsibility for the acceleration may come into dispute when pursuing the costs from the directing party. For example, the owner may believe that the contractor experienced production delays and should accelerate, while the contractor may believe that the delays were, in fact, owner-caused by issues such as site access, delayed review of submittals, or changes to the design, so it could not execute its work in the time planned. Such disputes will be resolved through an acceleration claim.
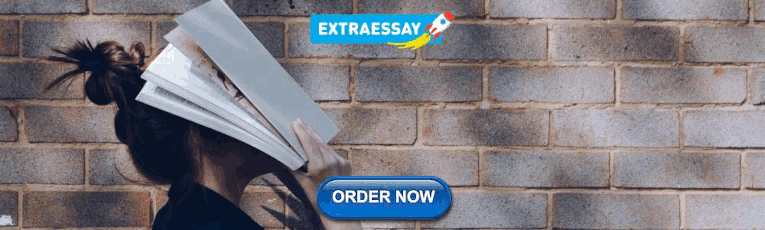
3. Constructive Acceleration
This type of acceleration is more complex and heavily dependent on the situation. More commonly, constructive acceleration is seen in cases where the contractor incurs excusable delays and submits a request for an extension, but the owner rejects the request and continues to hold the contractor to contractual deadlines. Thus, the contractor’s only option is to accelerate work to meet the schedule. To distinguish constructive acceleration from voluntary acceleration, the contractor must demonstrate and prove five conditions established by the General Services Board of Contract Appeals: [1]
- the contractor has experienced a period of excusable delay under the contract;
- the contractor requested an extension of the contract schedule in a timely and sufficient manner;
- the owner denied the contractor’s request or did not respond within a reasonable time;
- the owner’s demand for completion within the original performance period (or earlier than the entitled period of excusable delay); and
- the contractor incurred additional costs for acceleration efforts.
Note that delays need not be compensable, only excusable, to serve as the basis of the contractor’s constructive acceleration claim to recover additional costs.
Risks of Schedule Recovery and Acceleration Methods
A contractor can accelerate a schedule using one of two general methods:
- Activity crashing: shortening the duration of a task by adding more resources or costs.
- Activity overlapping: performing activities in parallel instead of in sequence, as planned.
While crashing the activities naturally increases the direct cost due to the cost of extra resources, higher overtime rates, and any other methods needed to reduce task duration, there are other less direct costs to be considered.
Additional crews on a regular shift, overtime rates, and multiple shifts may result in higher costs since they tend to reduce productivity. Studies on the effects of overtime on construction labor productivity have consistently demonstrated an inverse relationship between the amount of overtime work and labor productivity, as shown below.
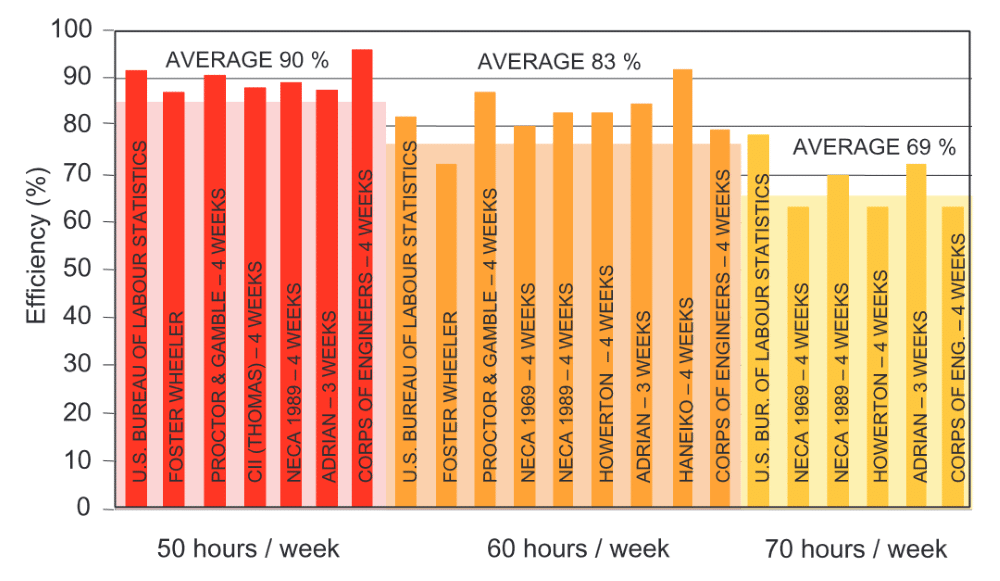
Furthermore, the longer that overtime schedules are relied upon to recover from delays, the more likely it is that further reductions in worker productivity will be observed. As overtime continues, crew exhaustion may further reduce overall productivity rates by as much as 30-40% within 10 weeks. [3]
According to a National Research Council of Canada Institute for Research in Construction guidebook on productivity, overstaffing and crowding of work areas both negatively affect productivity as shown below. [4]
Overstaffed crews
- dilute supervision
- increase strain on equipment/material demands
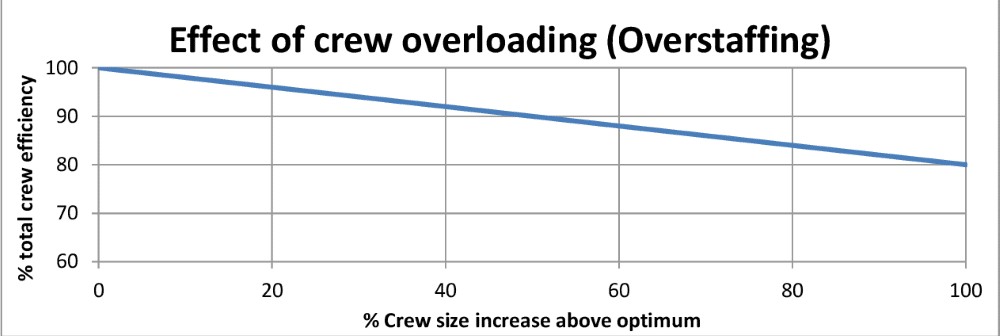
Overcrowding of spaces
- prevents workers from having adequate space to work effectively
- reduces morale
- interferes with the movement of materials and equipment
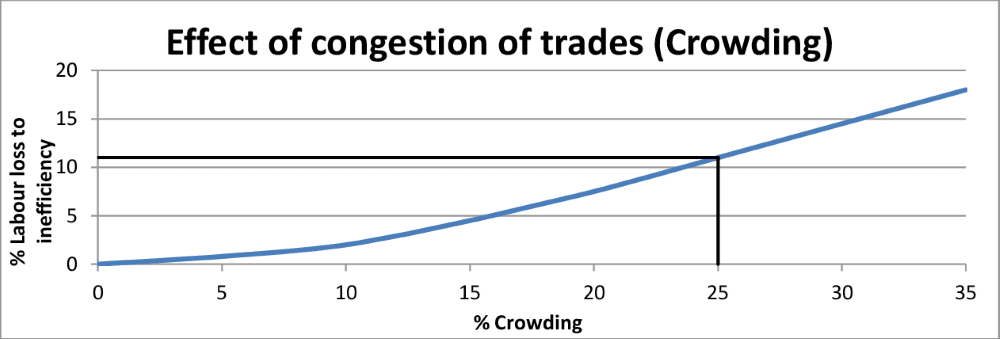
Activity overlapping, on the other hand, does not necessarily add any immediate additional direct costs but often introduces added risk and greater uncertainty to the project plan. For example, starting a successor activity while the predecessor is still in progress increases the likelihood of an impact to the successor activity should a change or rework be required on the predecessor activity. Any changes in the predecessor activity will likely produce rework for the successor task and may prolong the duration of the successor task beyond what would have been necessary had the same rework had been performed as originally scheduled. For example, if a mistake or change was made in the progress of roughing in walls but affected areas have already been enclosed due to activity overlapping, the impact of rework will now include the removal and reinstallation of drywall as well as the correction of the rough-in work. Therefore, overlapping may not ultimately be as efficient as expected because of uncertainties that create additional work and delays.
Furthermore, the overlapping of activities can have the same productivity impacts observed with increasing crew sizes for individual activities. Having activities occur in parallel may result in crowding and congestion in project areas with limited space or access and in turn, decrease productivity. Due to the complexity and uniqueness of each activity on each project, overlapping should be considered deliberately, with a greater focus on preemptive coordination to detect possible issues before they manifest as additional delays.
Regardless of the method, it is important for contractors to understand the implications of acceleration so the potential cost is fully understood and the anticipated productivity is realistic.
Successful Acceleration Claims
Detailed records are the key.
There are several aspects of construction disputes involving acceleration that need to be understood when faced with a potential delay scenario or when pursuing such a claim. Most importantly, acceleration claims can be particularly difficult to pursue. Segregating self-inflicted damages from those solely attributable to the required acceleration efforts requires detailed cost and schedule data as well as sufficient notice documentation among other things. The difficulty demonstrating entitlement and proving damages directly associated with implied acceleration orders reiterates the importance of proper record keeping for schedule updates, communication with the owner, and cost tracking. The level of detail of these records greatly influences the chances of recovery as well as decreases the cost associated with pursuit.
Improving the understanding of acceleration claims, methods of acceleration, as well as their risks, can help contractors and owners efficiently identify and resolve acceleration-related construction delay claims.
To learn more about VERTEX’s Construction Claims services or to speak with a Construction Claims Expert , call 888.298.5162 or submit an inquiry .
Related Services
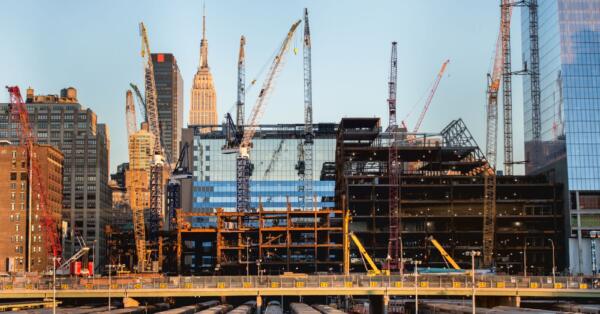
VERTEX's experts help contractors, owners, sureties, and insurance carriers investigate and manage litigated construction claims.
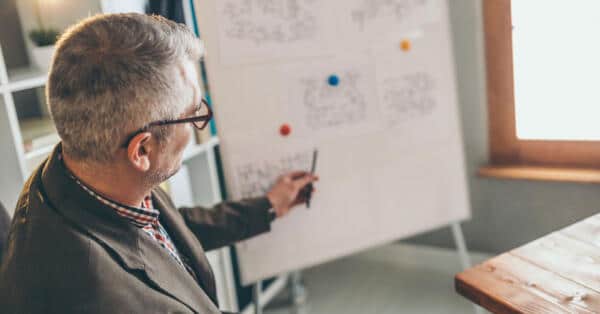
Expert Witness Services
VERTEX offers expert services on megaprojects and high-profile real estate and other property or construction claims throughout the globe.
[1] 6 GSBCA No. 2429, 68-2 BCA 7377 (1968).
[2] Brunies, R., & Emir, Z. (2001). Calculating Loss of Productivity Due to Overtime Using Published Charts – Fact or Fiction. Montreal: Revay and Associates Limited.
[3] Construction Industry Cost Effectiveness Task Force (1980). Scheduled Overtime Effect on Construction Projects
[4] Dozzi, S.P. & AbouRizk, S.M. (1993). Productivity in Construction. Ottawa: National Research Council Canada

Carl Stokley
Senior manager, construction claims.
Carl Stokley is a Senior Manager in VERTEX's Contract Claims group. Mr. Stokley is a professional engineer who has provided consulting and expert services for matters throughout North America.
About Carl Stokley
Sign up for More Insights
Causes of delays in construction industry and comparative delay analysis techniques with SCL protocol
Engineering, Construction and Architectural Management
ISSN : 0969-9988
Article publication date: 21 May 2018
Issue publication date: 21 May 2018
The purpose of this paper is to reveal the main causes of delays in the projects are from the client (relative importance index (RII)=0.716), labor and equipment (RII=0.701) and contractor (RII=0.698). Hence determining the contractual responsibility of delay is the most likely source of dispute in construction projects and many techniques have been used in the courts to demonstrate the criticalities of a delay event on the project schedule. Therefore, authors try to investigate all process-based techniques of delay claims and evaluated and conformed them with principles by Society of Construction Law (SCL) protocol and Association for the Advancement of Cost Engineering International (AACEI) in order to choose the best techniques based on the specific circumstances of each project.
Design/methodology/approach
This section is divided into two distinct parts: refers to the methods used to assess the perceptions of clients, consultants, and contractors on the relative importance of causes of delay in construction industry; and refers to advantages and disadvantages of various techniques used to analyze delays and their conform with SCL protocol. A questionnaire was developed to assess the perceptions of clients, consultants, and contractors on the relative importance of causes of delay in Iranian construction industry. The respondents were asked to indicate their response category on 78 well-recognized construction delay factors identified by authors.
In total, 78 causes of delay were identified through research. The identified causes are combined into seven groups. The field survey included 58 contractors, 55 consultants, and 62 client. Data collected were analyzed by RII and Statistical Package for Social Sciences (SPSS). The authors identified main causes of delay and ten most important causes, according to Table AII, from the perspective of three major groups of participants (clients, consultants and contractors). The ranking of categories of causes of delay, according to Table I, were: client-related causes (RII=0.716); labor and equipment category causes (RII=0.701); contractor-related causes (RII=0.698); material-related causes (RII=0.690); design-related causes (RII=0.666); external causes (RII=0.662); and consultant-related causes (RII=0.662). But according to the discussions and given that determining the contractual responsibility of delay is the most likely source of dispute in construction industry and many techniques have been used in the courts to demonstrate the criticalities of a delay event on the project schedule.
Originality/value
All process-based techniques of delay analysis have been present in this paper and categorized in 11 groups. In order to understand the advantages and disadvantages of them by clients, contractor and consultant, a thorough review conducted to reveal the nature of techniques. In the next step, given that selecting the most appropriate technique based on constraints and specific conditions of each project is one of the most important steps to carry out a successful delay analysis. The authors conformed, all process-based techniques of delay analysis, by SCL protocol and AACEI principles. Finally, the result of this match was brought in order to choose the best technique based on the specific circumstances of each project.
- Project management
Methodology
Shahsavand, P. , Marefat, A. and Parchamijalal, M. (2018), "Causes of delays in construction industry and comparative delay analysis techniques with SCL protocol", Engineering, Construction and Architectural Management , Vol. 25 No. 4, pp. 497-533. https://doi.org/10.1108/ECAM-10-2016-0220
Emerald Publishing Limited
Copyright © 2018, Parvaneh Shahsavand, Akbar Marefat and Majid Parchamijalal
Published by Emerald Publishing Limited. This article is published under the Creative Commons Attribution (CC BY 4.0) licence. Anyone may reproduce, distribute, translate and create derivative works of this article (for both commercial & non-commercial purposes), subject to full attribution to the original publication and authors. The full terms of this licence may be seen at http://creativecommons.org/licences/by/4.0/legalcode
Introduction
In construction, delay could be defined as the time overrun either beyond completion date specified in a contract or beyond the date that the parties agreed upon for delivery of a project. To the owner, delay means loss of revenue through lack of production facilities and rentable space or a dependence on present facilities. In some cases, to the contractor, delay means higher overhead costs because of longer work period, higher material costs through inflation, and due to labor cost increases.
Therefore, completing projects on time is an indicator of efficiency, but the construction process is subject to many variables and unpredictable factors, which result from many sources and it is necessary that a detailed assessment be conducted and calculates the loss resulted from delays on both parties in the projects with time required for the extension of projects time if the project is delayed.
A lot of research efforts have been made to study delay causes in different countries. For example, Odeh and Battaineh (2002) , Vilventhan and Kalidindi (2016) showed that owner interference, inadequate contractor experience, financing and payments, labor productivity, slow decision making, improper planning, and sub-contractors are among ten top most important factors causing delay in Jordan; Maura et al. (2007) discovered that design errors, client liability, project specification and direct change order by the client are the major factors that cause the time and cost overrun in Portuguese; Abdul-Rahman et al. (2006) conducted a study on delay mitigation in the Malaysian construction industry; they proved that a financial problem is confirmed by the survey as the main causes of delay.
Hence, one of the most important problems in the construction industry is delay and it is essential to define the actual causes of delay in any construction project. So choosing an appropriate delay analysis method is an important part of construction industry. The famous process-based methods include the global impact, net impact, adjusted as-built CPM, as-planned expanded, but-for, snapshot, time impact, windows and isolated delay type techniques ( Yang et al. , 2006 ; Yang and Kao, 2007 ). These techniques are applied to prepare the logical basis to persuade their claims concerning the extension of time and financial burden but each delay analysis method adopts a different approach to identify delay impacts and may yield different results.
But in Iran, there is not a comprehensive and practical package for delays analysis techniques to determine which one is appropriate in accordance with the feature of the project. So the authors examine all delay analysis techniques that are frequently used in the construction project in Iran in order to determine which delay analysis techniques is appropriate for each construction project.
In this paper the main causes of delays in Iranian construction projects have been determined and the aim of this study is to operate a method based on which one could select the delay analysis techniques appropriate to the nature of the projects that what is needed to implement this method is to analyze the Society of Construction Law (SCL) protocols and analytical delay techniques and then to implement standards of protocol with delay analysis techniques.
Literature review
Many researchers have studied the causes of delay and delay analysis techniques in the construction industry. We have broken the studies into two parts: studies on causes of delay; and studies on delay analysis techniques.
Studies on causes of delay
Delay in construction is a global phenomenon affecting not only the construction industry but the overall economy of countries as well ( Sambasvian and Soon, 2007 ; Parchamijalal and Shahsavand, 2016 ). Delays in construction are caused by several factors. Ahmed et al. (2003) grouped delays into two categories – internal causes and external causes. Internal causes arise from the parties to the contract (e.g. contractor, client, and consultant). External causes, on the other hand, arise from events beyond the control of the parties. These include the act of God, government action, and material suppliers. Sweis et al. (2008) studied the causes of delay in residential projects in Jordan and concluded that financial difficulties faced by the contractor and too many change orders by the owner are the leading causes of construction delay. Abd El-Razek et al. (2008) in a similar study in Egypt found that the most important causes of delay are financed by contractor during construction, delays in contractor’s payment by owner, design changes by owner or his agent during construction, partial payments during construction, and non-utilization of professional construction/contractual management. Sambasvian and Soon (2007) identified the delay factors and their impact on project completion in the Malaysian construction industry. The results indicated that the ten from a list of 28 different causes of delay were: contractor’s improper planning; contractor’s poor site management; inadequate contractor experience; client’s inadequate financial resources and payments for completed work; problems with subcontractors; shortage in material; labor supply; equipment availability and failure; lack of communication between parties; and mistakes during the construction stage. Assaf and Al Hejji (2006) conducted a survey on time performance of large construction projects in Saudi Arabia. The survey had 73 different causes of delay. He studied the importance of various causes from the viewpoint of contractors, consultants, and owners. The most common cause of delay identified by all the parties was “change order.” He also found that about 70 percent of the projects experienced time overruns.
The previously mentioned studies were generally focused on finding causes of delays. Some of these studies identified very limited (lacking) factors or ignored some important groups. This may be misleading or may result in wrong analysis. In this paper, through a comprehensive literature review and interviews with highly experienced construction professionals, the authors attempted to use the relative importance index (RII) method in the quantification of the relative importance of a comprehensive list of delay factors in construction projects in Iran.
Studies on delay analysis techniques
Project managers and schedule (timing) analysts do often face with the problem of how to analyze the complicated delays and resolve the claims resulted from it. In addition, in most of the contracts of construction, it is not specified which method would be used to evaluate and analyze delays. On the other hand, the contractor and client have different views against analysis and determination of responsibility for delay. As a result, calculating delays and determination of responsibilities of each of the party is an important issue. Therefore, project managers must have a systematic approach for analyzing delays and allocation of responsibilities. Since there are different methods to analyze delays such as: pervasive influence technique, Bar chart or Gant chart technique, collapse technique or (but because), critical path method, time impact technique, global impact technique, net impact technique, impacted as-planned technique, collapsed as-built technique, sectional technique or snapshot technique, isolated delay type technique. So choosing an appropriate delay analysis technique for calculation of the effects of delay on project is a critical decision that is discussed in this paper ( Hoshino and Livengood, 2011 ).
SCL has identified some factors that should be considered in choosing the method of delay analysis that includes the conditions related to the contracts, nature of causal events, value of claims, time in hand, recorded information, information of the existing time plan and planner’s experience on the project ( Braimah, 2013 ; Yangand Kao, 2012 ). SCL protocol is intended to act as an aid to the interpretation of the delay and disruption provisions contained in standard of civil engineering and building contracts and to act as a guide to the manner in which the managers ought to properly prepare delay and disruption claims and how adjudicators, arbitrators and judges ought to properly determine them. The protocol does not fully reflect the provisions concerning delay and disruption contained in certain standard forms and is not intended to have contractual status, it is believed that it is at least a useful guidance document.
Arditi and Pattanakitchamroon (2006) discussed selecting a suitable delay analysis method and concluded that the most appropriate analysis method depends on information available, time of analysis and capabilities of the method, as well as time, funds and effort allocated to the analysis. Bubshait and Cunningham (1998) proposed an approach for selecting one suitable method among the as-planned method, the as-built method, and the modified as-built method. Their approach consists of four scenarios, each comprising various approved schedules (network or bar chart) with different evidence and progress reports. They concluded that method selection depends on the time and resources available, and on the accessibility of project control documentation. Mohan and Al-Gahtani (2006) discussed ten delay analysis techniques in analysis flow and compared them in resolving the issues of real time delay, concurrent delay and pacing delay. Based on study results, Mohan and Al-Gahtani proposed a desirable delay analysis system consisting of 11 requirements, such as the requirement for the project schedule to be updated every day, taking account of all delays and changes in total floats.
This section is divided into two distinct parts: refers to the methods used to assess the perceptions of clients, consultants, and contractors on the relative importance of causes of delay in construction industry; and refers to the nature of process-based techniques used to analyze delays and their conformity with SCL protocol.
Experts’ perception of causes of delay
A questionnaire was developed to assess the perceptions of those in the Iranian construction industry on the relative importance of causes of delays. Then the questionnaire was filled out by highly experienced construction professionals including project managers, site managers, technical office managers, technical office engineers, procurement managers, and technical consultants. The collected data were analyzed through the RII method. RII or weight is a type of relative importance analyses. RII was used for the analysis because it best fits the purpose of this study. The analysis included ranking the different causes according to the relative importance indices. The analysis revealed the factors and groups that contribute most to delays.
The respondents were asked to indicate their response category on 78 well-recognized Construction delay factors identified by authors. These causes were categorized into the following seven major groups. Client-related causes (with 19 factors); contractor-related causes (with 13 factors); consultant-related causes (with 9 factors); design-related causes (with 8 factors); material-related causes (with 8 factors); labor and equipment category causes (with 8 factors); and external causes (with 13 factors). A five-point Likert scale ranging from 1 (very low) to 5 (very high) was adopted to capture the importance of causes of delays. Before distributing the questionnaires, a small interview with industry professionals was conducted that includes a 15 clients, 15 consultants and 15contractors. The basic purpose of this interview was to verify the completeness of the questionnaire in capturing the factors relevant for Iran. All the respondents agreed that the questionnaire was sufficient to capture the causes of delays. We distributed the questionnaires through our co-workers in Public Works Department of Iran, developers, consultants and construction firms. Our co-workers in turn distributed to their friends. This sampling method enabled us to obtain a large number of completed questionnaires quickly and economically. In total, 250 sets of questionnaires were distributed to the potential respondents at all levels in the organizations within the construction industry. In all, 100 sets were distributed to clients, 70 sets to consultants and 80 sets to the contractors. Of the 250 questionnaires, 175 sets (70 percent) were returned and there were 62 sets (62 percent) from clients, 55 sets (79 percent) from consultants and 58 sets (73 percent) from contractors.
The nature of process-based techniques
All process-based techniques of delay analysis have been present in this paper and categorized in 11 groups. In order to understand the pros and cons of them, a thorough review conducted with the participation of clients, contractor and consultant to reveal the nature of these techniques. The results of this review on techniques have been obtained based on several years’ experiences of the client, consultant and contractor and studies that have been done by authors .In the next step, the most appropriate technique has been selected based on constraints and specific conditions of each project, which is one of the most important steps to carry out a successful delay analysis. The authors conformed, all process-based techniques of delay analysis, by SCL protocol and Association for the Advancement of Cost Engineering International (AACEI) principles. The SCL protocol recommends that wherever possible, an appropriate method should be agreed and adopted by the parties before retrospective delay analysis is carried out. The protocol gives guidance on the appropriateness, or otherwise of different types of retrospective delay analysis to different evidential situations. The protocol suggests that if the method is not agreed between the parties, then this failure to agreement should be taken into consideration by the arbitrator, or judge when awarding the costs of the dispute. Finally, the result of this match was brought in order to choose the best technique based on the specific circumstances of each project.
Data analysis
Kometa et al. (1994) and Sambasvian and Soon (2007) used the RII method to determine the relative importance of the various causes of delays. The same method was adopted in this study. RIIs are calculated for each factor as in the following equation: (1) ( RII ) = ∑ w A N = 5 n 5 + 4 n 4 + 3 n 3 + 2 n 2 + 1 n 1 5 N where RII is the relative importance index; W the weighing given to each factor by respondents (ranging from 1 to 5); A the highest weight (i.e. 5 in this case); and N the total number of respondents. The RII value had a range of 0 to 1 (0 not inclusive); the higher the RII, the more important was the cause of delays. The causes were ranked based on RII values. From the ranking assigned to each cause of delays, we were able to identify the most important factors or causes of delays in Iranian construction industry. For more information about the list of causes of delays categorized into seven groups refer to Table AI .
In Table AII , the main causes of delays in each category specified and have been ranked based on RII. For more information on the way of ranking and 78 causes of delays from experts’ views refer to Table AII ( Table I ).
Table II , summarizes RII and ranking of the categories of causes of delay as perceived by all respondents.
Analysis of variance (ANOVA)
ANOVA is used to get the average scores obtained by construction industry experts given to each of the causes of delay (i.e. RII) and every seven fold causes has been rated using these scores and the rate of their being under the effect on the projects has been prioritized.
According to Levene’s test, the significance of this test is more than 0.05 and parametric tests such as ANOVA can be used. ANOVA is a collection of statistical models used to analyze the differences among group means. In the ANOVA setting, the observed variance in a particular variable is partitioned into components attributable to different sources of variation. Factorial ANOVA can be balanced or unbalanced ( Gelman, 2005 ; Armstrong et al. , 2002 ). This is to say, you can have the same number of subjects in each group (balanced) or not (unbalanced). The results shown in Table III indicate that the data were balance and there is no significant difference among respondents’ data, at the community.
Pearson’s correlation
Data normality test (one sample K-S test) clarifies that the calculated p-value is greater than the significant level which is equal to 0.05 ( p -value > 0.05). This in turn denotes that data follows normal distribution and we can use Pearson’s correlation test.
In order to test the degree of agreement between the three groups of respondents, a correlation analysis was done using Pearson’s correlation coefficient. Table IV gives the results of this analysis. Based on this test, view point of clients and contractors are not the same as consultants and have different opinions from each other. On the other hand, view point of Clients and the contractor were nearly identical to rank of delay factors.
So based on the perceptions of clients, consultants, and contractors on the relative importance of causes of delay in Iranian construction industry and data analysis using Statistical Package for Social Sciences (SPSS), we found that clients (with 19 subcategories and RII=0.716); labor and equipment (with 8 subcategories and RII=0.701) and contractors (with 13 subcategories and RII=0.698), respectively, have the highest impact in construction industry.
In this paper, at first all the delays have been identified and ranked and validated from client, contractors and consultants, viewpoint three factors of ten causes that lead to delays and are of main causes have been identified in Table AI . Then, in Table II , based on the opinions of clients, contractors, consultants and all the three, the index of relative importance and ranking have been ranked in seven categories in which delays had been examined. In the following, in order to lower or remove those after interviewing with experts, 40 alternative have been extracted and presented in Table AIII that performing this task could prevent delays emergence in next projects.
Given that delays are an integral part of construction industry. Therefore, the authors in second part of this paper discussed the pros and cons of all process-based techniques of delay claims and compared the versatility of each of them with SCL protocol.
The first level that is shown in Table V (Items 4, 6 and 7), represents a simple method that a major problem in view of the simplification in these techniques is that they do not have a mechanism for exact determination of the types of delays, as a result, those delays that should not be applied in the analysis, are considered and therefore unrealistic and exaggerated results are obtained. In addition, these techniques consider the timing schedule only once (primary schedule) and assume that the critical path is fixed for the entire project. This makes the delays in contrast to what has really happened, potentially be considered as critical and also global impact technique, against two other techniques, has another weakness that has not the ability to consider the delays at the same time.
The second level shows the detailed procedure, which includes the techniques that have been identified with number 2, 5, 8, 9, 10 and 11, in Table V . These techniques offer convenient and reliable methods for analyzing delays. At the same time enhancing and mitigation methods with analysis, define the type of delay. Increasing and decreasing methods while doing the analysis, identify the type of delay, too. Of course, the main problem is that these two techniques are applied only once to the scheduled timing and thus no change in the critical paths during the project implementation is accepted and also, simultaneous delays are not considered, of all the methods, both time impact technique and snapshot technique, because of considering the impact of delays during project and CPM scheduling, are known as systematic and reliable methods for quantifying delays in construction projects. The biggest problem with these techniques is that during the analysis none of them identify the delay type accurately and a series of other analyses to determine the contribution of the employer and the contractor of the delay is necessary. Another disadvantage of time impact technique is that the delay activities has been analyzed and examined separately and the impact of simultaneous delays is not specified during the analysis and due to a number of delayed events in the project, the analysis may be very time consuming. Accuracy of both time impact technique and snapshot technique is a function of the number of intervals between analyses that occur during the project from beginning to end. Isolated delay type technique relying on the strengths of previous techniques, provide a practical method for analyzing delays. The mentioned technique showed that in the case of reliable information and reports available in the project, it is superior to the other techniques. Isolated delay type techniques study the delays during the analysis process and therefore it reduces time needed for delay analysis and so the expense is decreased. This technique considers the simultaneous delays in various activities.
The SCL protocol has been prepared by the SCL for determining extensions of time and compensation for delay and disruption. It exists to provide guidance to all parties in the construction process when dealing with delay and disruption matters. It recognizes that transparency of information and methodology is central to both dispute prevention and dispute resolution.
The object of the protocol is to provide useful guidance on some of the common delays and disruption issues that arise in construction projects. The purpose of the protocol is to provide a means by which the parties can resolve these matters and avoid unnecessary disputes. A focus of the protocol therefore is the provision of practical and principled guidance on proportionate measures for dealing with delay and disruption issues that can be applied in relation to all projects, regardless of complexity or scale, to avoid disputes and where disputes are unavoidable to limit the costs of those disputes. Users of the protocol should apply its recommendations with common sense. The protocol is intended to be a balanced document reflecting equally the interests of all parties to the construction process.
Given that the delays occur in every construction project and the significance of these delays varies considerably from project to project, hence identifying the type of delay analysis techniques and selecting the most appropriate technique based on constraints and specific conditions of each project is one of the most important steps to carry out a successful delay analysis. But unfortunately in Iran, because of the lack of accurate knowledge on a variety of techniques all parties cannot use the most suitable delay analysis techniques for each project and this leads to create a lot of disputes and claims in projects. Hence the delay analysis techniques for further investigation are evaluated and conformed with principles which have been released in Table VI by SCL and (AACEI. Finally, the result of this match, the rate of using each of these techniques in various stages of construction projects, the plausibility of each of these techniques in court, the level of expertise needed to experts analyst delays and the amount of time required for the analysis depends, the use of each of these techniques in large and complex projects, that regarding the mentioned items, each technique could be selected with respect to the kind of project regarding the feature it has. The information needed to be analyzed the delay, etc. have been shown in Table VI .
By examinations carried out and interviews with the experts, the Iranian project have been divided into three groups from magnitude perspective and into 6 categories from delay rates perspective that regarding their features and the results obtained from complete comparison of the methods of delays analysis ( Tables V and VII ) a proper method to examine delay in six above classes are suggested as the following table.
Construction projects often suffer from delays due to a wide variety of reasons, which can have severe financial impact on the project. As a result, delay claims may be filed. But delays can be avoided or minimized when their causes are clearly identified. However, in case of delays the analysis of its impact, the causes, and effects of the delaying activities is one of the most complicated types of claims analysis. The aim of this paper is to identify the delay factors in construction projects and introduction type of delay analysis techniques for applying more reliable and precise techniques in order to reduce the frequency and to mitigate the severity of disputes and litigation due to delay claims because delays are considered to be a serious problem in the construction industry.
Hence through a detailed literature review and interviews with experts from the Iranian construction industry, a total of 78 different delay factors were identified and categorized into seven groups the field survey included 58 contractors, 55 consultants and 62 clients. Data collected were analyzed by RII and SPSS. We identified main causes of delay and ten most important causes, according to Table AI .
According to the discussions and given that determining the contractual responsibility of delay is the most likely source of dispute in construction industry and many techniques have been used in the courts to demonstrate the criticalities of a delay event on the project schedule, the authors discussed the pros and cons of all process-based techniques of delay claims and compared the versatility of each of them with SCL protocol in order to choose the best techniques based on the specific circumstances of each project.
The Iranian projects have been classified from magnitude perspective into three categories and from the perspective of emergence of delays; they have divided into six groups. Several methods of analyzing delays have been compared from different dimension ( Tables V-VII ). So regarding the features of projects one could select the most suitable methods kind based on Table VIII . For example, for those mega projects with many delays, i.e. 6th class, the methods of analysis of delays has been selected as the most suitable method.
In this paper, by providing all the causes of delays in Iranian construction projects, all parties can be familiar with the variety of delays and implementation of solutions which are presented in Table AIII in appendixes, they can decrease the causes of delays in projects. But delay cannot be controlled from time to time and occurs in every construction project and the significance of this delay varies considerably from project to project. Unfortunately in Iran, there is not a comprehensive and practical package for delays analysis techniques to determine which technique is appropriate for each project. So the implications of this paper could be used as a complete package, in order to select the appropriate delays analysis techniques according to the circumstances of each project. Hence, by the use of SCL protocol guidance and according to the circumstances of each project the authors show on which basis choose the best delay analysis technique to reduce the confusion and disputes arising from the delays in construction projects.
Importance of delay causes
RII and ranking of categories of causes of delay
Type of delay analysis techniques and explanation of pros and cons of each method
Factors influencing on choosing a suitable method to analyze delay, according to SCL protocol and AACEI RP-FSA
Accommodation and evaluation of Tables V and VI
The method of choosing the most appropriate technique based on the nature of project and the value of delays
List of causes of delay categorized into seven groups
The main causes of delays in each category specified and have been ranked based on RII
Ranking the causes of delay and the ideas of decreasing and removing it
Abd El-Razek , M.E. , Bassioni , H.A. and Mobarak , A.M. ( 2008 ), “ Causes of delays in building construction projects in Egypt ”, Journal of Construction Engineering and Management , Vol. 134 No. 11 , pp. 831 - 841 .
Abdul-Rahman , H. , Berawi , M.A. , Berawi , A.R. , Mohamed , O. , Othman , M. and Yahya , I.A. ( 2006 ), “ Delay mitigation in the Malaysian construction industry ”, Journal of Construction Engineering and Management , Vol. 132 No. 2 , pp. 125 - 133 .
Ahmed , S.M. , Azhar , S. , Kappagntula , P. and Gollapudil , D. ( 2003 ), “ Delays in construction: a brief study of the Florida construction industry ”, Proceedings of the 39th Annual ASC Conference, Clemson University , Clemson, SC , pp. 257 - 266 .
Alkass , S. , Mazerolle , M. and Harris , F. ( 1996 ), “ Construction delay analysis techniques ”, Construction Management and Economics , Vol. 14 No. 5 , pp. 375 - 394 .
Arditi , D. and Pattanakitchamroon , T. ( 2006 ), “ Selecting a delay analysis method in resolving construction claims ”, International Journal of Project Management , Vol. 24 No. 2 , pp. 145 - 155 .
Armstrong , R.A. , Eperjesi , F. and Gilmartin , B. ( 2002 ), “ The application of analysis of variance (ANOVA) to different experimental designs in optometry ”, Vision Sciences , Vol. 22 , Aston University , Birmingham , pp. 248 - 256 .
Assaf , S.A. and Al Hejji , S. ( 2006 ), “ Causes of delay in large construction projects ”, International Journal of Project Management , Vol. 24 No. 4 , pp. 349 - 357 .
Braimah , N. ( 2013 ), “ Construction delay analysis techniques – a review of application issues and improvement needs ”, Buildings , Vol. 3 No. 3 , pp. 506 - 531 .
Bubshait , A. and Cunningham , M.J. ( 1998 ), “ Comparison of delay analysis methodologies ”, Journal of Construction Engineering and Management , Vol. 124 No. 4 , pp. 315 - 322 .
Clark , R.P. ( 2006 ), “ Time impact analysis ”, available at: www.brewerconsulting.co.uk/cases/CJ0625CL.htm
Gelman , A. ( 2005 ), “ Analysis of variance: why it is more important than ever (with discussion) ”, Annals of Statistics , Vol. 33 , pp. 1 - 53 .
Hoshino , K.P. and Livengood , J.C. ( 2011 ), “ Forensic schedule analysis ”, AACE: International Recommended Practice , Vol. 29 Nos 29R-03 , pp. 130 - 139 .
Kartam , S. ( 1999 ), “ Generic methodology for analysing delay claim ”, Journal of Construction and Management , Vol. 125 No. 6 , pp. 409 - 419 .
Keane , P.J. and Caletka , A.F. ( 2008 ), Delay Analysis in Construction Contracts , Wiley Blackwell .
Kometa , S.T. , Olomolaiye , P.O. and Harris , F.C. ( 1994 ), “ Attributes of UK construction clients influencing project consultants’ performance ”, Construction Management Economics , Vol. 12 No. 5 , pp. 433 - 443 .
Maura , H.P. , Teixeira , J.C. and Pires , B. ( 2007 ), “ Dealing with cost and time in the Portugees construction industry ”, CIB World Building Congress (422), University of Minho, Guimaraes .
Mohan , S.B. and Al-Gahtani , K.S. ( 2006 ), “ Current delay analysis techniques and improvement ”, Cost Engineering , Vol. 48 No. 9 , pp. 12 - 21 .
Odeh , A.M. and Battaineh , H.T. ( 2002 ), “ Causes of construction delay: traditional contracts” , International Journal of Project Management , Vol. 20 , pp. 67 - 73 , available at: http://dx.doi.org/10.1016/S0263-7863(00)00037-5
Parchamijalal , M. and Shahsavand , P. ( 2016 ), “ The decision matrix approach to dealing with delays in construction projects ”, International Conference on Management and Dynamic Economics .
Sambasvian , M. and Soon , Y.W. ( 2007 ), “ Causes and effects of delays in Malaysian construction industry ”, International Journal of Project Management , Vol. 25 No. 5 , pp. 522 - 531 .
Stumpf , G.R. ( 2000 ), “ Schedule delay analysis ”, Journal of Cost Engineering , Vol. 42 No. 7 , pp. 32 - 33 .
Sweis , G. , Sweis , R. , Abu Hammad , A. and Shboul , A. ( 2008 ), “ Delays in construction projects: the case of Jordan ”, International Journal of Project Management , Vol. 26 No. 6 , pp. 665 - 674 .
Vilventhan , A. and Kalidindi , S.N. ( 2016 ), “ Interrelationships of factors causing delays in the relocation of utilities: a cognitive mapping approach ”, Engineering, Construction and Architectural Management , Vol. 23 No. 3 , pp. 349 - 368 .
Yang , J.B. and Kao , C.K. ( 2007 ), “ A knowledge map for delay analysis development ”, Proceedings of Fourth International Conference on Construction in the 21st Century , Gold Coast , pp. 565 - 573 .
Yang , J.B. and Kao , C.K. ( 2012 ), “ Critical path effect based delay analysis method for construction projects ”, International Journal of Project Management , Vol. 30 No. 3 , pp. 385 - 397 .
Yang , J.B. , Kao , C.K. and Lee , Y.Y. ( 2006 ), “ System requirement analysis of a construction delay analysis construction ”, 23rd International Symposium on Automation and Robotics in Construction , Tokyo , pp. 102 - 106 .
Further reading
AACE ( 2007 ), “ International, AACE international recommended practice No. 29R-03 ”, Forensic Schedule Analysis, Published by the Society of Construction Low, Administrative Office, Wantage .
Badir , Y.F.M. and Kadir , M.R. ( 2002 ), “ Industrialized building systems in Malaysia ”, Journal of Architectural Engineering , Vol. 8 No. 1 .
Desai , M. and Bhatt , R. ( 2013 ), “ A Methodology for ranking of causes of delay for residential construction projects in Indian Context ”, International Journal of Emerging Technology and Advanced Engineering , Vol. 3 No. 3 , pp. 396 - 404 .
Frimpong , Y. and Oluwoye , J. ( 2003 ), “ Significant factors causing delay and cost overruns in construction of groundwater projects in Ghana ”, Journal of Construction Research , No. 2 , pp. 175 - 187 .
Gidado , K. and Niazai , Gh. ( 2012 ), Causes of Project Delay In the Construction Industry in Afghanistan , University of Brighton .
Koushki , P.A. , Al-Rashid , K. and Kartam , N. ( 2005 ), “ Delays and cost increases in the construction of private residential projects in Kuwait ”, Construction Management and Economics , Vol. 23 No. 3 , pp. 285 - 294 .
Long , L.H. , Lee , Y.D. and Lee , J.Y. ( 2008 ), “ Delay and cost overruns in Vietnam large construction projects: a comparison with other selected countries ”, Journal of Civil Engineering , Vol. 12 No. 6 , pp. 367 - 377 .
Parchamijalal , M. , Golabchi , M. and Yusefi , E. ( 2015 ), “ Analysing windows- based Delay analysis methods in easy plan program and offering a framework in selecting the best Delay analysis method ”, Sharif Journal Civil Engineering , Vol. 31 No. 3 , pp. 41 - 49 .
Parchamijalal , M. , Shahsavand , P. and Marefat , A. ( 2015 ), “Examination and Classification of the causes of creating delays in construction projects in Iran and comparative analysis techniques delay with SCL protocol ”, 11th International Conference of Project Management , Tehran , February .
The Society of Construction Law (SCL) ( 2002 ), Delay and Disruption Protocol , 1st ed. , Society of Construction Law , Oxford , pp. 20 - 80 .
Trauner , J.T. , Manginelli , W.A. , Lowe , J.S. , Nagata , M.F. and Furniss , B.J. ( 2009 ), Construction Delays: Understanding them Clearly and Delay Analysis in Construction Analyzing them Correctly” , Elsevier Inc , London .
Wa’el Alaghbari , M. , Razali , A. , Kadir , A. and Ernawati , A. ( 2007 ), “ The significant factors causing delay of building construction projects in Malaysia ”, Engineering, Construction and Architectural Management , Vol. 14 No. 2 , pp. 192 - 206 .
Corresponding author
Related articles, we’re listening — tell us what you think, something didn’t work….
Report bugs here
All feedback is valuable
Please share your general feedback
Join us on our journey
Platform update page.
Visit emeraldpublishing.com/platformupdate to discover the latest news and updates
Questions & More Information
Answers to the most commonly asked questions here
- Canada (English)
- Canada (Français)
- Europe & Middle East
- Deutschland (Deutsch)
- France (Français)
- United Arab Emirates (English)
- United Kingdom (English)
- Asia Pacific
- Australia (English)
- Singapore (English)
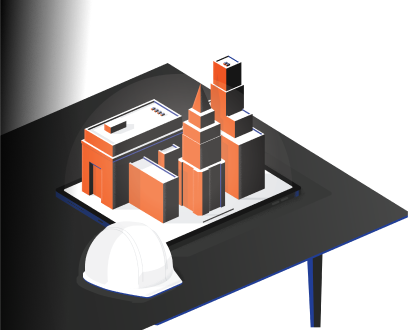
Take Your Knowledge to the Next Level
Choose from our library of free certification courses—start earning CE credits today.
Construction Delay Claims: Learn the Main Types — and Their Defenses
Last Updated Jan 30, 2024
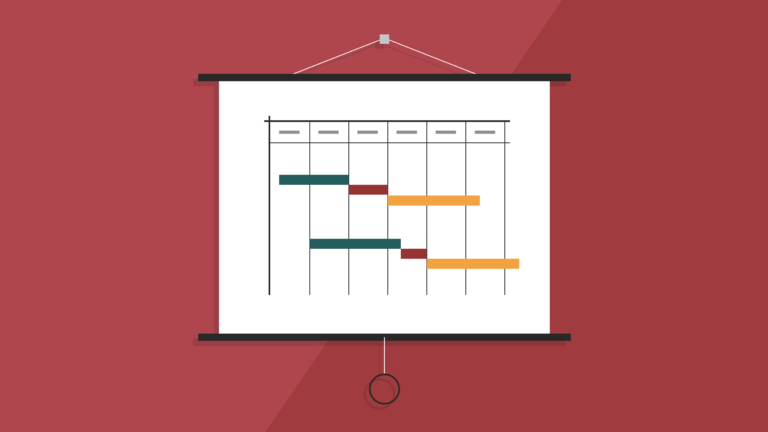
Delays are among the most common disputes that arise on construction projects. However, the process of establishing and proving a delay claim can get complicated. That's why having a comprehensive understanding of the necessary elements to justify a delay claim can be a priceless advantage. At the same time, understanding the ins and outs of delay claims can also help construction businesses defend against improper claims, too.
Table of contents
Types of construction delay claims
To determine the impact, the delay must be appropriately classified. This is a tiered classification system, it involves answering one question, then moving on to the next. The main types of schedule delays on a construction project are:
Excusable vs. inexcusable
- Compensable vs. non-compensable
The construction agreement will typically contain provisions that describe when these delay claims apply, and the notification process required in the event of a delay.
Critical vs. non-critical
This is the first and most important question to answer: Was the delay critical or non-critical?
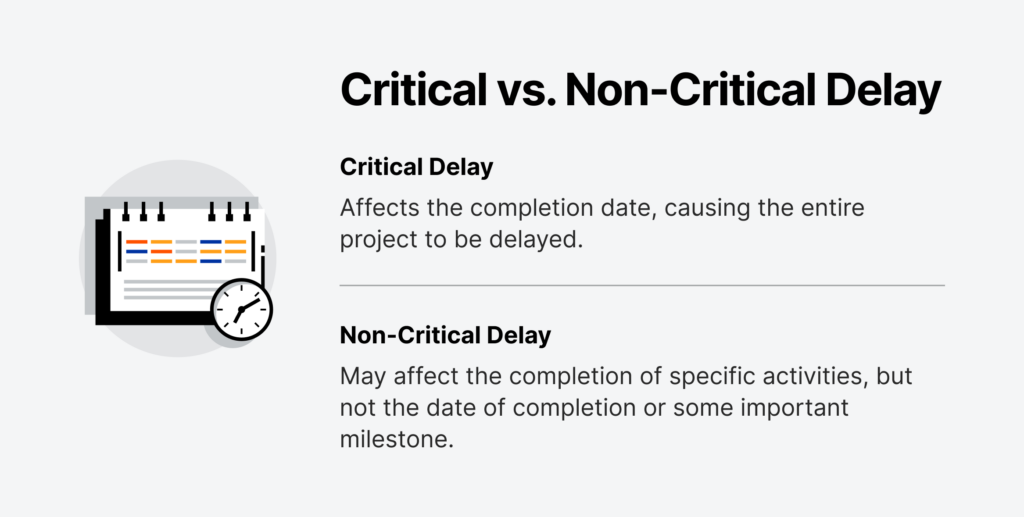
A critical delay is one that will affect the project completion date (or some other important milestone date on a project). Critical delays can't really be made up - they just tack on extra time. Non-critical delays will affect the completion of specific activities, but not the completion date or the date of some important milestone. The determining factor is whether the delay extends the Critical Path of the project .
A CPM schedule will set out a timeline of the most extended activities throughout the project. It will establish the minimum amount of time it will take to complete these “critical” activities. These critical activities need to be performed at specific times and in a particular order to allow the next critical phase to begin.
If the delay has no effect on the project’s critical path, then the delay is non-critical and may involve a simple change order to correct the delay.
Once you have determined if the delay is critical or not, you will need to establish whether the delay is an excusable one . An excusable delay is one that allows the contractor an extension of time, compensation, or both.
Why? Because these delays are out of the contractor's control . The common excusable delays should be outlined in the construction contract .
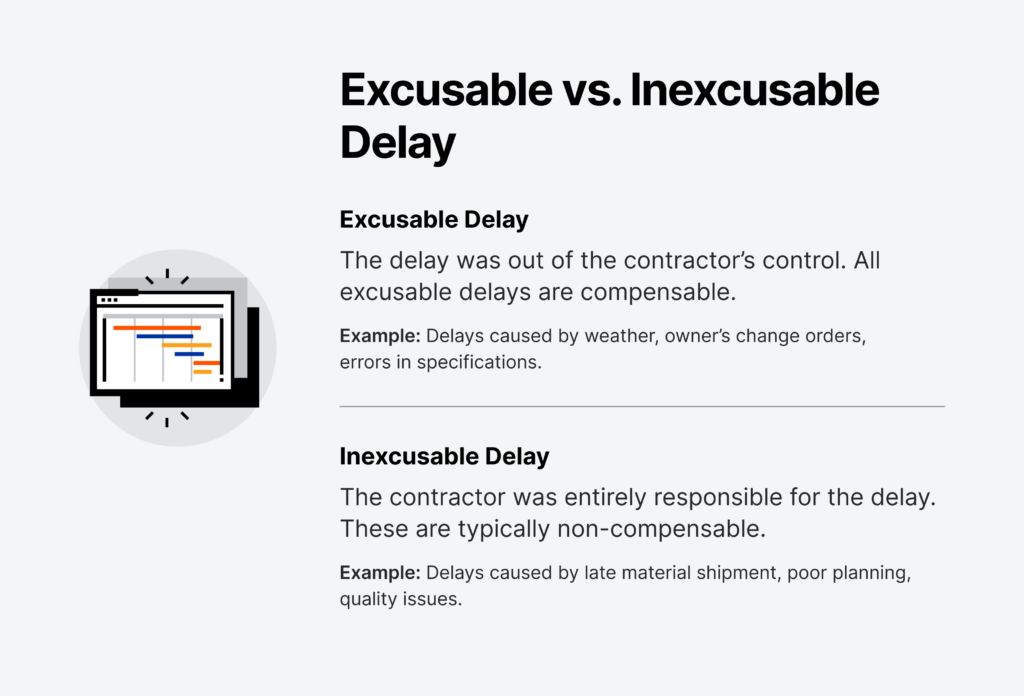
The most natural example of excusable delays is when a delay falls under a force majeure clause — events such as natural disasters or terrorist attacks. Excusable delays can also result from errors or omissions in the plans or even simple issues that were caused by the client .
Inexcusable delays are those where the contractor was entirely responsible for extending the project's duration. If this is the case, then the contractor will be liable for any costs or damages caused by the delay . This can be a result of delayed mobilization, late submissions, failure to obtain permitting (if they're responsible for it), or general poor planning on behalf of the contractor.
Compensable vs. Non-compensable delays
The final question to ask: Is the delay a compensable one? When a delay is "compensable," it means the party affected by the delay should be given either an extension of time or compensation for the delay of their work.
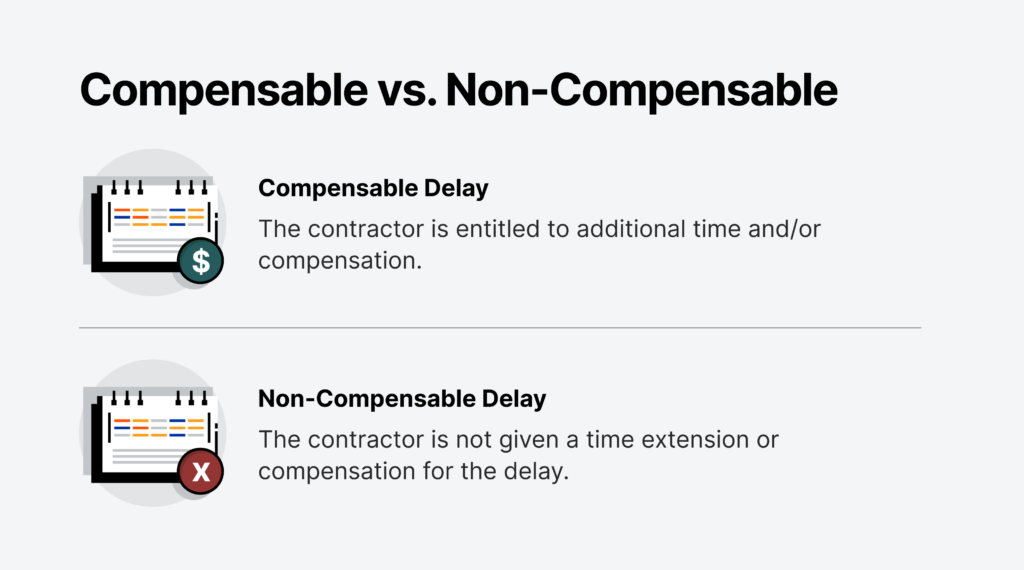
All excusable delays are compensable. This means that any time a delay is considered "excusable," the contractor will generally have a claim for a time extension, compensation, or both.
If the contractor is solely at fault, the delay will very likely be non-compensable. Non-compensable delays can fall under any of the other categories, depending on the situation and contract terms.
Legal damages for construction delays
If a schedule delay causes a financial impact to a party on the project, they may seek damages through a breach of contract claim .
Damages claimed by a contractor
For owner-caused delays (or those caused by another contractor), a contractor may have a claim for:
- Project management & supervisory expenses
- Loss of use
- Loss of rents
- Lost profits
- Insurance costs
- Construction loan interest
Damages claimed by an owner
When a contractor is at fault for a delay, an owner may have a claim for:
- Supervision costs
- Extended general conditions
- Jobsite trailer rental
- Temporary facilities/utilities
- Liability insurance
- Equipment rental & maintenance costs
- Field labor
- Increased materials cost
- Lost productivity
- Hourly labor rate increases
- De-mobilization/re-mobilization
Right to finish early
Even if your work was ahead of schedule, you might still have a valid delay claim. Let's say you had planned on finishing work earlier than the contract completion date, but encountered an owner-caused delay. You may still finish on time, but you were still delayed — and now all the costs you intended on saving by completing early are lost.
So if a contractor at the outset of the project, (a) intended to complete the contract early, (b) could do so and (c) would have finished ahead of schedule but-for the owner's actions — they could still have a valid delay claim !
5 defenses to construction delay claims
Whether a construction business is making a delay claim or defending against one, it's important to know what factors might affect the viability of a delay claim. Here are some of the more prominent defenses against a delay claim on a construction project.
Concurrent delay
A concurrent delay occurs when multiple activities affect the project's timeline, but the delays don't precisely stack on top of each other. That doesn't necessarily mean the delays have to happen at the exact same time to be considered concurrent.
Instead, if multiple delays do occur and they each independently impact the completion date, the delays can be regarded as concurrent — at least to some degree. If a delay truly is concurrent with some other delay on the project, then that can be used as an argument against compensating for the accused delay. Proving that a delay was concurrent often requires extensive expert analysis and documentation evidence. The challenge here is how to allocate the amount and of fault and liability of each party.
No damages for delay clause
Because delays are so prevalent in the construction industry, construction contracts often include a no damages for delay clause (a.k.a. no pay for delay). This essentially declares that delays are all part of the business, and any costs associated with them should be written off. The result? Eat any losses, request a time extension, then move on.
The enforceability of these clauses varies depending on the jurisdiction. Most states have prohibited or at least limited these provisions — so be sure you know how your state handles these. If a no damages for delay clause is allowed, there are still certain exceptions to enforceability.
Some exceptions might be where delays:
- are not covered by the clause language,
- are not contemplated at the time of contracting,
- sustain for an unreasonable time,
- result from active interference by the owner, or
- result from a fundamental breach of contract by the owner that justifies the non-enforcement of the clause.
In one case in California, a subcontractor won their claim against the GC after scope changes and defective materials caused project delays — even though their subcontract contained a "no damages for delay" clause.
Improper Notice
Construction contracts are chock-full of notice requirements. Most courts take these notice provisions seriously. Contractors should familiarize themselves with these from the outset of the project. Any time a delay is encountered, contractors should send a project delay letter to the GC or owner immediately. It also helps to provide photos, documentation, or other reports to support the complaint. Where notice is required, but not sent, even the most worthy of construction delay claims can falter. It's imperative to understand what notice is required under the contract and when that notice must be sent.
Learn more : How to Write a Notice of Delay for a Construction Project
Time is of the essence clause
This is a peculiar one, but it could definitely affect a claim. A "time is of the essence" clause means that the contract will hold everyone responsible for completing the agreed-upon work by the agreed-upon time. It may seem obvious, but if "time is of the essence" language is in the contract, that means that any delay (even minor ones) could be considered a material breach of the contract.
Force majeure events
We touched on these earlier. If the contract does have a force majeure clause, it will typically list a few triggering events like floods or fires. However, other events can fall under this category as well. Force majeure generally covers any occurrences that were (a) not reasonably foreseeable at the time of contracting, (b) beyond the control of the parties, and (c) not caused or compounded by negligence. Consequently, when one of these events occur, performance will either be suspended or excused depending on the contract terms and the duration of the disruption.
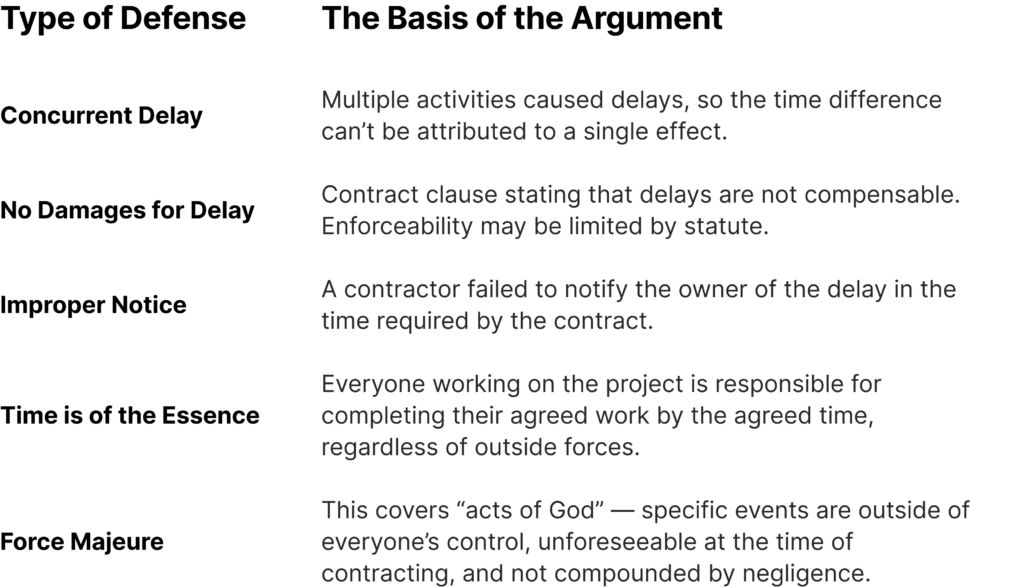
Scroll less, learn more about construction.
Subscribe to The Blueprint, Procore’s construction newsletter, to get content from industry experts delivered straight to your inbox.
You’re signed up to receive The Blueprint newsletter from Procore. You can unsubscribe at any time.
Categories:
Alex Benarroche
25 articles
Alex Benarroche serves as Associate Counsel for Procore. His legal expertise includes construction, contracts, business, and intellectual property. Alex is bilingual in English and Spanish. He earned a J.D. from Loyola University College of Law and an M.S. in Intellectual Property and Internet Law from the University of Alicante in Spain. Originally from South Florida, Alex has called New Orleans home since 2003.
Explore more helpful resources
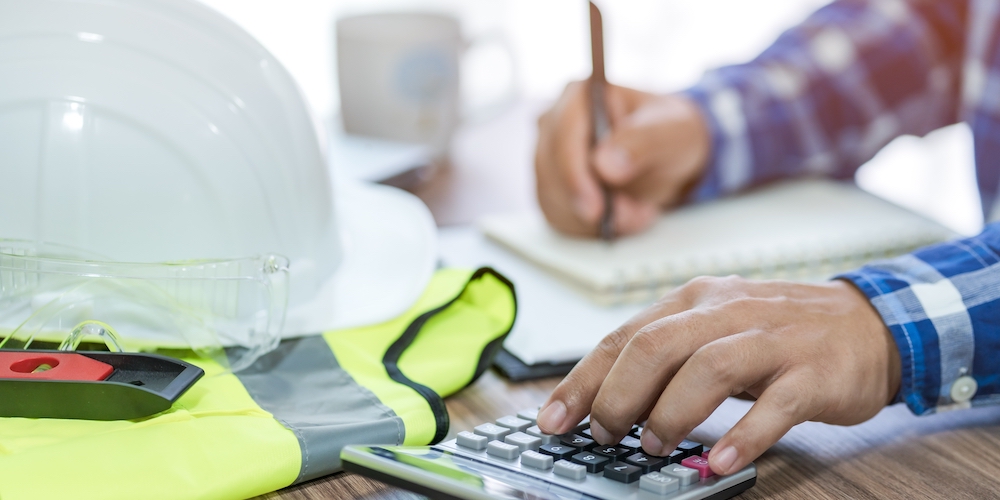
.css-c249p1::before{width:100%;height:100%;display:block;position:absolute;top:0px;left:0px;z-index:0;content:'';cursor:inherit;} Pencil Requisition: Previewing the Construction Payment Application
Construction projects don’t always go exactly as planned. Most jobs will have change orders, timing delays and other challenges. Because of the ever-changing nature of construction, it can be difficult...
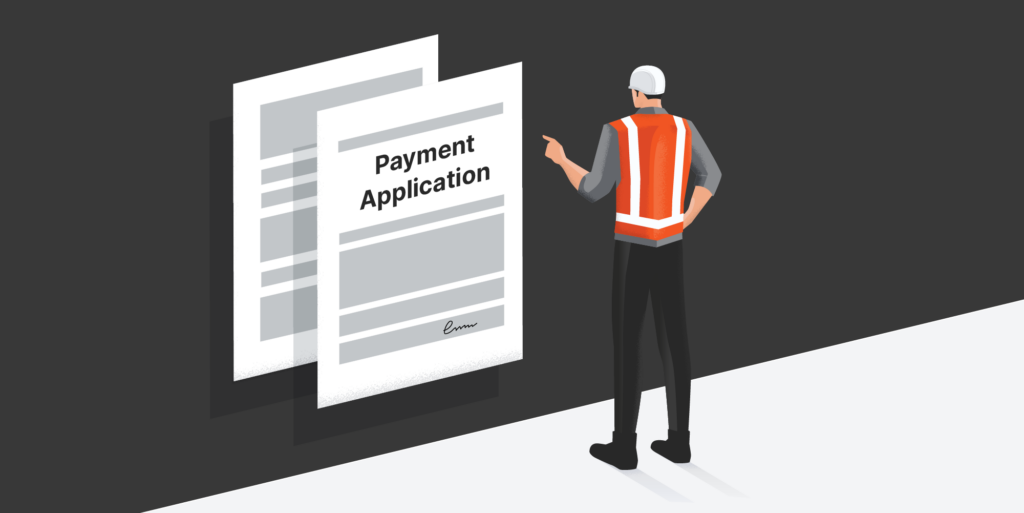
Construction Payment Applications: A Guide for Contractors
For general contractors, getting paid requires much more than just an invoice. Before any checks are sent, contractors are asked to prove what has been completed, delivered, and more with...
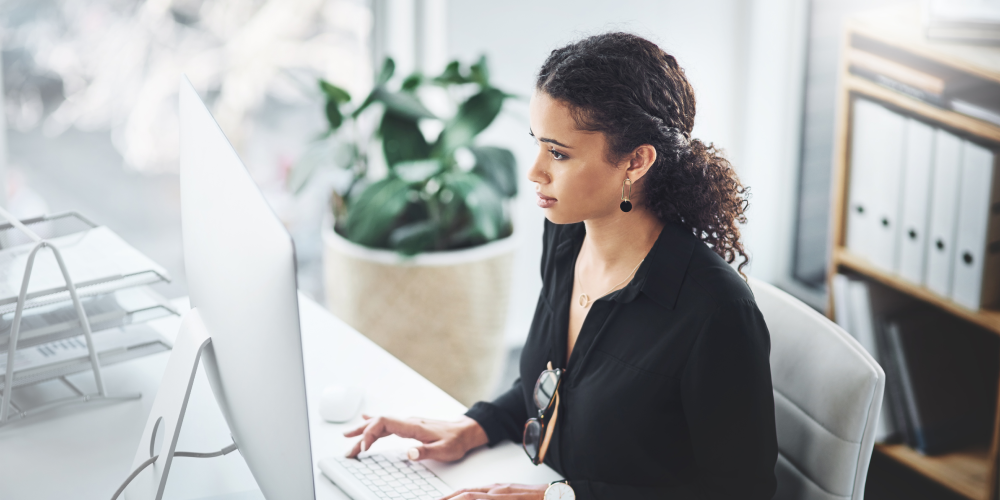
Construction Escrow: What Contractors & Suppliers Need to Know
Every construction project starts with funding — and some projects are funded through construction escrow accounts. These accounts are often opened by the lending institution to help with the distribution...
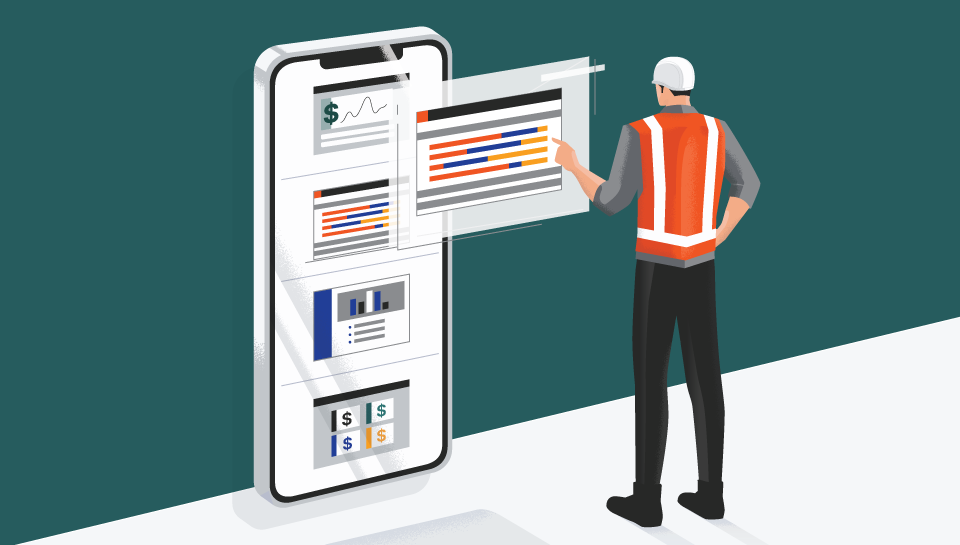
Contractor Payment Schedules: Why They’re Important & Choosing the Best Schedule for Each Project
In construction, a payment schedule is a timeline of the payments to be made throughout the lifetime of a project. On most jobs, contractors don’t receive a single, lump-sum payment...

Construction Delays
Project Controls Series
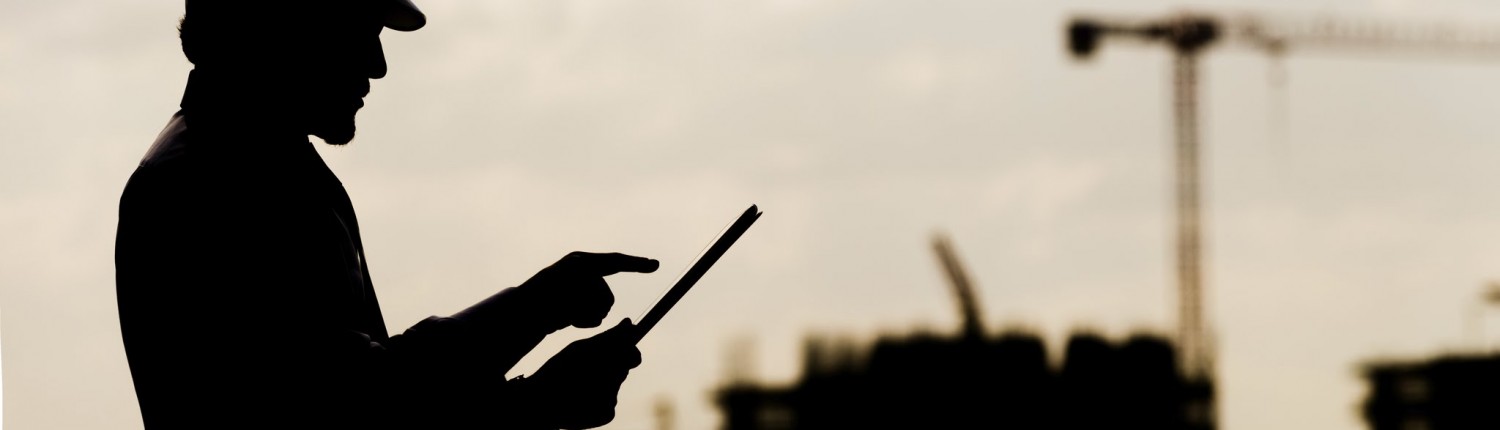
How To: Categorize, Analyze and Report Project Construction Delays
Construction Delays are unplanned events that happen during both work planning and execution that result in a cost and/or schedule variance to the original project plan. Delays can impact your project cost and extend your project delivery schedule.
Delays may also result in litigation if there is a dispute over who was responsible for the project delay – so it is critical to capture, analyze and resolve project delays quickly, and know who is responsible for each delay. Capturing, assessing and reporting on delays is a standard project management process to manage the unplanned events that happen during the planning and execution of any major project.
This 1-Page summary in our Project Controls series gives you a downloadable quick Reference Guide on the fundamentals of construction delays and a cheat sheet of the widely accepted categories for delays, and methods to assess delays.
This article will cover:
- What you need to get started capturing construction delays
- How to categorize delays when they are found
- The different methods used to assess the delay’s impact on project schedule
- Example delay report
What You Need to Manage Construction Delays:
1. a project plan with your critical path.
Your project plan will include your project’s scope, schedule, and costs. Project plans may also include resource loading and a quality plan.
Project Managers use tools like Oracle Primavera P6 or Microsoft Project to create their resource-loaded project schedule (or they simply use an Excel spreadsheet to organize their project – though managing projects in Excel can quickly become a headache). Project Managers will also integrate these tools with other software packages during work execution for daily progress tracking, delay tracking and timesheets.
2. A Delay Capture Form
You are not planning for a delay to happen on your project, but when it does you need a form at the ready to capture the details of the delay. Capturing delays in a standardized way at the point where the delay actually occurs (especially for field delays during execution) is important when it comes to assessing the delay, in particular who was responsible for the delay.
Having a standard way to capture every construction delay and report on those delays when found to project stakeholders can save Contractors a lot of time and money, avoid major headaches with the Owner and potentially avoid the risk of expensive litigation. And if you do end up in litigation, you want to have clear objective evidence of the details of every delay.
3. Delay Categorization
There are 4 generally accepted categorizations for delays:
Critical vs. Non-Critical Delays:
You want to identify if the delay is on the critical path – because if it is, the delay is going to extend your project’s completion date and will require you to update your project plan. Critical delays need to be resolved immediately. Being alerted through an email notification or some other method when these delays happen and formulating a plan to resolve the delay as quickly as possible is very important for successful project execution.
Depending on the type of delay you encountered and the criticality of the delay you may want to record a non-conformance around the delay and plan corrective & preventative actions to avoid another occurrence of that delay. You may additionally need to update your risk profile for the project if there’s potential a similar delay may happen as the project progresses.
Non-critical delays still need to be captured, but they do not necessarily impact the project delivery date. They may still have a cost impact so they also need to be reported on and resolved.
Excusable vs. Non-Excusable Delays
Whether or not it’s a critical delay you need to determine if it’s an excusable delay (it was out of the Contractor’s control to prevent the delay from occurring) or if it’s a non-excusable delay (it was a direct result of the Contractor’s actions, or they could have foreseeably taken action to avoid the delay from happening in the first place).
The contract between the Contractor and the Owner will typically specify what delays are excusable and which ones are not – so it is important that you are familiar with the language of the contract!
Some examples of excusable delays:
- Acts of God
- Floods / Fire
- Own-Directed Change (which would typically be captured as part of a formal change management system)
- Errors / Omissions (if the Owner left out critical detail which impacted the scope of the project)
Excusable delays may be compensable – the Owner may give the Contractor more time to complete the project given the delay or the Contractor may be given more money to complete the project as delays can extend the time the work crews need to be kept on.
Not all delays are excusable – some examples of non-excusable delays:
- Late performance of sub-contractors impacting project schedule / milestones
- Poor work quality (may result in re-work)
- Inadequate equipment – is usually the Contractor’s responsibility to ensure the crews have the right tools and equipment to execute their work activities
Disputes over whether or not a delay is excusable or not can cause major headaches on a project, so it is important the contract language is clear and delays are discussed with the Owner as soon as they are encountered on the project. Having a detailed, documented record of every delay and agreement between the Owner and Contractor as to who is responsible is crucial if there is ever a dispute potentially leading to litigation – document your delays!
Compensable vs. Non-Compensable Delays
Non-excusable delays are not compensable; the Contractor is expected to absorb any penalties related to non-excusable delays as it speaks to performance of the work scope.
Excusable delays may be compensable and again this would typically be specified in the contract between the Owner and the Contractor. Some examples of compensable delays:
- Owner-directed change
- Errors / omissions
The important point is that these types of delays are within the Owner’s control, so they shoulder the responsibility for the delay occurrence. Some examples of non-compensable delays:
- Flood / Fire
These types of delays are not within the control of the Owner or the Contractor; how they are handled then typically comes down to the specific case and how that is described in the contract language.
Concurrent Delays
Concurrent delays are when two delays happen at the same time, each independently affecting the project completion date – and the question becomes which delay is responsible for any delay in the project delivery.
Concurrent delays are a complicated topic and it’s often said they are both sword and shield when claiming costs due to delay, project delivery time extension, or both. Owners will often argue concurrent delays by the Contractor as a reason for awarding a time extension on the project without awarding costs. Contractors will often argue concurrent delays by the Owner as a reason why costs should not be assessed for the delays.
Again it is important to read the contract language and understand who is responsible.
Here’s a flow diagram summary of the different delay categories:
4. Delay Assessment and Analysis
Depending on the scope and complexity of the project you may use a different analysis method for evaluating the impact of the delay on the project:
Foresight (forward-looking):
This method looks ahead at the plan for completion before the work is actually done and is often referred to as the Impacted As Planned Method.
In this method delays are added into the as-planned / project baseline schedule and the forward looking project completion date is re-calculated based on those new items added in. Views of delay activities added in may focus only Owner or Contractor delays.
This method is simple however it ignores the as-built history of the project and assumes the as-planned schedule doesn’t change moving forward.
Hindsight (backward-looking):
The basis of this method is that delays are best analyzed from the end of the project looking back at what happened. This analysis method is often referred to as the Collapsed As-Built Method.
In this method an as-built schedule is built at the end of the project, and delays are assessed against that schedule. A delay is removed from the schedule to produce the collapsed as-built schedule. If the project delivery date of the collapsed schedule is earlier than the actual as-built scheduled then it is assessed that the delay was responsible for the schedule variance.
Contemporaneous:
The contemporaneous schedule is the combination of the project baseline schedule and schedule updates made along the way to manage the execution of the project. They are the most representative view of the status of the work throughout the duration of the project. This method is often referred to as the Contemporaneous Period Analysis , or Windows Analysis .
In this method the as-planned schedule is analyzed through a ‘window’ into the schedule – between two periods. Delays are analyzed on this snapshot of the schedule based on the project documents, and the schedule is calculated based on the delays. The process is then repeated for the next window.
The objective of this method is to evaluate the delay against the current critical path for the project, to determine the impact of that delay on delivery (if any) or is it accounted for in the float of the ongoing activities at that point in time.
This method gives the most accurate analysis of the true impact of delays on project schedule and takes into account the dynamic nature of the critical path through project execution. That said it’s a time consuming method to implement for a project, so consider the project needs.
5. Delay Reporting
Stakeholders need a view of the delays that have occurred and this is done through a delay log, which captures the important points of every delay recorded. Your delay capture method should tie back in to your delay log so that the assessment and analysis can happen.
Here’s an example of what a delay log may look like:
This covers the basic concepts of construction delays, including how to categorize delays, different methods to assess the impact of delays on schedule and the need to report on delays to keep stakeholders in the loop. Good delay capture and documentation can save a lot of headache and difficult meetings between the Owner and Contractor – so make sure to well document your delays.
Download the Construction Delays Reference Guide , print it off and take it with you so that you always have at your fingertips of the basics of delay categorization.
Learn how you to improve your delay capture and reporting using Industrial Audit’s secure mobile field data collection software and get started today!
Share this Efficiency Note with your colleagues!
- Share on Facebook
- Share on Twitter
- Share on WhatsApp
- Share on LinkedIn
- Share by Mail
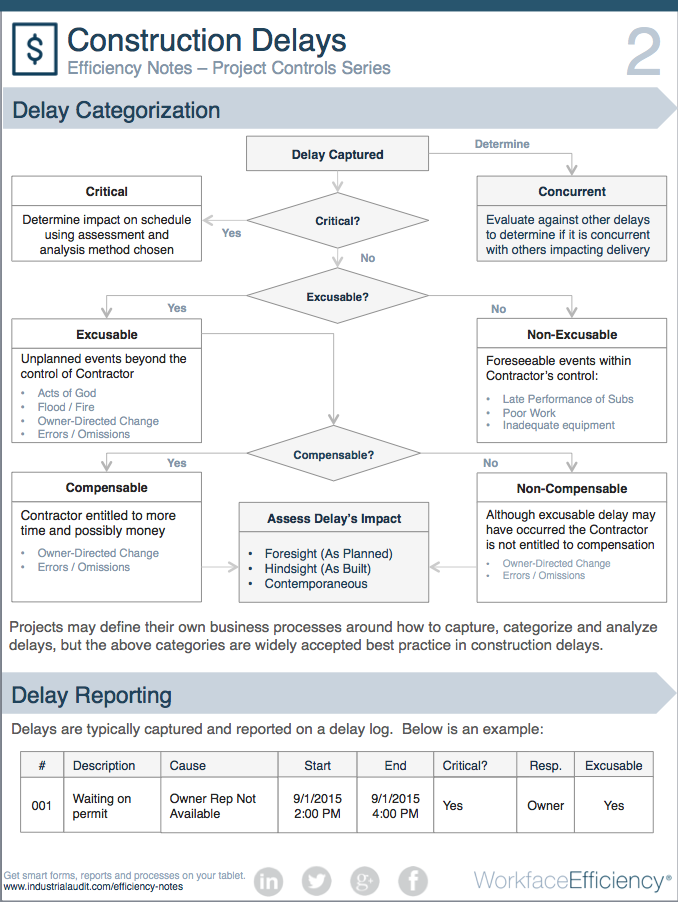
Click to download the free reference!
News and Updates

phone: +1-416-848-6088 tollfree: +1-855-33-FIELD
We answer the phone: 08:00 to 18:00, GMT-5
We reply to email 24/7.
Mail or Ship to Us!
2100 Bloor Street West Suite 6114 Toronto, Ontario M6S 5A5 Canada
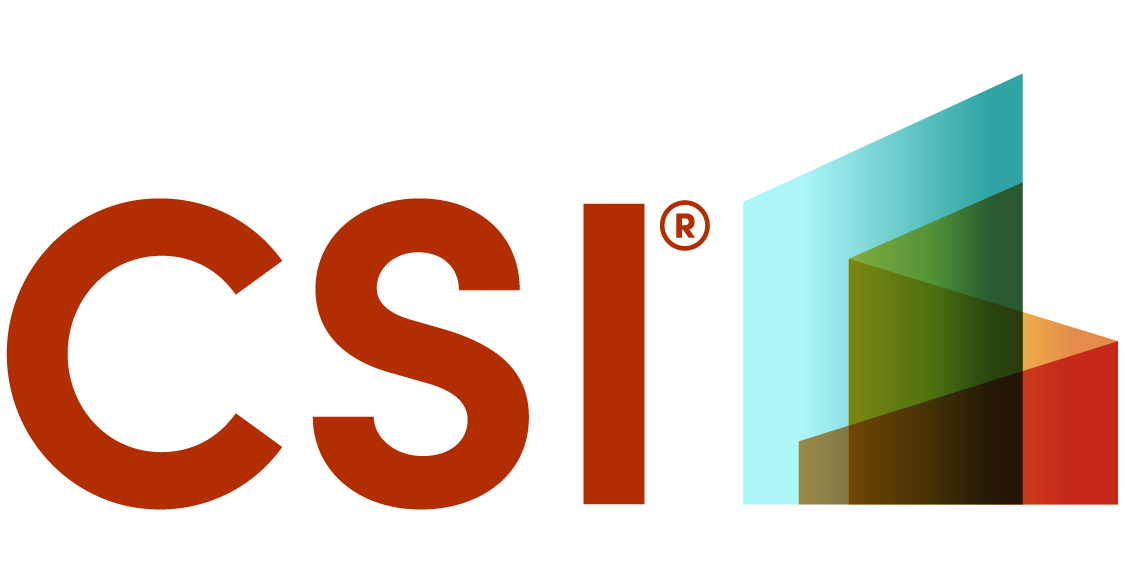
Blog Viewer
Delays in construction—a common source of claims, by kevin o'beirne, pe, fcsi, ccs, ccca, cdt posted 07-30-2021 10:44 am.
The most common sources of change proposals and claims in construction are likely owner-ordered changes in the work, differing site conditions, and delays. This blog post presents a general overview of delays in construction.
Types of Delays
Construction delays are typically apportioned into three principal categories:
- Delays within the contractor’s control.
- Delays within the owner’s control.
- Delays neither party can control.
Delays within the contractor’s control typically include delays resulting from the acts or inactions of the contractor, its subcontractors or suppliers of any tier, or anyone for whom any of them are responsible. Why the contractor has responsibility for delays by its subcontractors and suppliers is discussed in this blog post’s section on risk allocations. Other types of delays within the contractors control include delays resulting from ineffective project management, time required to remedy defective work, and other matters within the contractor’s control or responsibility.
Delays within the owner’s control include delays resulting from owner-ordered changes in the work and acts or inactions by the owner or facility manager, owner-hired design professional, construction manager as advisor (CMa), others hired by the owner (such as entities performing code-required special inspections and tests, program manager, and other owner-hired consultants), utility owners or transportation facility owners retained by the owner to perform certain work at or adjacent to the site, and other construction contractors retained by the owner for work at or adjacent to the site. On the premise of allocating contractual risk to the party best able to control that risk, the owner is responsible for delays caused by its employees, consultants, and contractors. The owner is also responsible for delays resulting from differing site conditions; the rationale for this is discussed in this post’s section on risk allocations.
Delays over which neither party has control are often termed “force majeure events” (literally, “uncontrollable force”) and often include: severe and unavoidable natural catastrophes such as fires, floods, epidemics, earthquakes, and volcanic activity; abnormal weather conditions; acts of war or terrorism; certain acts by governmental entities, such as embargoes and trade sanctions; labor disputes to which the contractor is not a direct party or a direct contributor; acts or failures to act of third-party utility owners, owners of transportation facilities, or other third-party entities (other than those hired by the owner for work at or adjacent to the site);; and perhaps others. What is considered a force majeure event often varies by contract. Perhaps the most common type of force majeure event cited in delay claims is abnormal weather, for which additional information is available here .
https://www.ejcdc.org/force-majeure-events-abnormal-weather-uncontrollable-delays-construction-project-contributed-kevin-obeirne-pe-vice-chair-ejcdc/#:~:text=Construction%20delays%20that%20are%20the,chance%20occurrence%2C%20unavoidable%20accident ”.
Location within the Contract Documents
While various provisions of the construction contract documents may allocate specific risks for certain types of delays, the principal clauses allocating such risks are typically in the general conditions, including:
- AIA A201—2017, Standard General Conditions of the Contract for Construction . Section 8.3 (“Delays and Extensions of Time”).
- EJCDC C-700—2018, Standard General Conditions of the Construction Contract , Paragraphs 4.05 (“Delays in Contractor’s Progress”) and 11.08 (“Change of Contract Times”).
- DBIA 535—2010, Standard Form of General Conditions of the Contract Between Owner and Design-Builder , Sections 1.2.8 (definition of “Force Majeure Event”) and 8.2 (“Delays to the Work”).
- ConsensusDocs 200—2017, Standard Agreement and General Conditions between Owner and Constructor (Lump Sum) , Section 6.3 (“Delays and Extensions of Time”).
CSI MasterFormat —2020 does not allocate any document or specification section numbers or titles for delays although, relative to the general topic of delays, it assigns “01 26 00 – Contract Modification Procedures” and “01 32 16 – Construction Progress Schedule”.
Allocation of Risk of Delays
Standard general conditions in widespread use in the United States generally allocate risk of delays as follows:
- Delays within the Contractors Control : The contractor is typically not due any change in the contract times or additional compensation for this type of delay. In the event of delays within the contractor’s control, the contractor is liable to the owner for liquidated damages and other damages (if any) for late completion, as established by the contract.
Delays by subcontractors and suppliers are a frequent source of disagreement between owners and contractors. For example, when a supplier delivers materials or equipment late, perhaps caused by delays at the manufacturer’s production facility or delays in shipping, the contractor may not have much actual control over the matter. Similarly, a contractor may have little control over whether a subcontractor shows up onsite to perform as scheduled. However, based on the principle of allocating risk to the party best able to control that risk, the contractor has greater ability to control its subcontractors and suppliers than does the owner.
Furthermore, occasionally, delays in delivering materials or equipment to the site or delays by a subcontractor arise from the contractor’s action or inaction, such as late authorization of subcontracts or purchase orders, insufficient communications or ineffective management of subcontractors or suppliers, or delayed payment to subcontractors and suppliers. For these reasons, the risk of delay by subcontractors and suppliers is, unless a “force majeure event,” the contractor’s responsibility..
- Delays within the Owner’s Control : For delays within the owner’s control, the contractor is typically due additional time (when the delay has adversely affected the contractor’s ability to comply with the contract times) and additional compensation for the costs of the delay. Common delay costs include extended costs for rental and use of construction equipment and machinery, even when idled), and extended “field overhead” (such as costs for maintaining field offices and storage facilities at the site, costs for site maintenance, and related costs).
Differing site conditions is a common cause of delay for which the owner is typically responsible. While some owners may perhaps believe they have no control over unforeseen conditions discovered during construction, such as differing subsurface conditions or the discovery of hazardous materials at the site, for most project delivery methods, such risk is allocated to the owner because the owner selected the site and furnished the contractor the construction drawings and specifications (i.e., the Spearin Doctrine). In design-build projects, there is usually increased risk for differing site conditions (and their associated delays) allocated to the design-builder, because the design-builder is responsible for appropriately investigating the site and preparing the design accordingly.
A basic concept in allocating the risk of delays is that the contractor is entitled to additional time only when the delay has adversely affected the contractor’s ability to comply with the contract times. When the delayed work is not on the construction progress schedule’s critical path and the delay is less than the available float in the schedule, the contractor is not entitled to additional contract time. However, even when delayed work is not on the construction progress schedule’s critical path, there may be potential for the delay to result in additional compensation to the contractor. For example, where work not on the critical path is delayed for reasons within the owner’s control and requires continuation onsite of a $500-per-hour crane that would otherwise have been demobilized from the site, the contractor may be entitled to additional compensation for the extended rental.
- Force Majeure Delays : Different standard general conditions take different approaches to allocating the risk of delays over which neither party has control. AIA A201 and ConsensusDocs 200 allow the contractor both additional time and additional compensation for force majeure delays, whereas EJCDC C-700 and DBIA 535 split the risk between the parties by allowing the contractor additional time (when the delay has adversely affected the contractor’s ability to comply with the contract times) but no additional compensation.
Because the types of delays and their associated risk allocations discussed above are so fundamental and widely-accepted in the design, construction, and legal communities, drafters of construction contracts are well-advised to reconsider the wisdom of attempting to modify them. Because contractual risk cannot be transferred without an associated cost, any such change is likely to affect the prices bid or proposed to the project owner.
Perhaps the most extreme type of fundamental change in delay risk allocations are “no damages for delay” clauses, which are relatively common in non-standard contracts unique to certain owners. Such clauses prohibit the contractor from receiving additional compensation for owner-caused delays. Unsurprisingly, “no damages for delay” clauses are strongly disliked by contractors and are, in this writer’s opinion, unfair. When included in a construction contract, such clauses almost certainly result in increased prices bid or proposed to the owner or may reduce competition among prospective bidders. Although “no damages for delay” clauses may be “legal”, courts and arbitrators have poked lots of holes in them; as just one example, Kalisch-Jarcho, Inc. v. City of New York (New York State Court of Appeals, 58 N.Y.2d 377, March 28, 1983).
Contractor arguments against “no damages for delay” clauses often assert the common law concept of “actie interference” by the owner. Such cases often allege the owner’s negligent or willful interfernce with the contractor’s ability to fulfill its contract time obligations.
Concurrent Delays
Before using a “no damages for delay” clause, the person or entity drafting the construction contract should obtain the owner’s consent to including the clause, and should advise the owner to consult with the owner’s legal counsel on the advisability of using such a provision.
A common source of disagreement concerning construction delays is concurrent delays , where two or more separate delays overlap. Causes of concurrent delays are often attributable to each party. An example of a concurrent delay is where part of the contractor’s work was behind schedule, perhaps due to a subcontractor or supplier, or inefficient project management, and the owner orders a change in another part of the work (which was not behind schedule) that also adversely affects the contractor’s ability to comply with the contract times. Impartially determining rights to additional time and compensation in concurrent delays is often challenging. Each party typically asserts the other party was the primary cause of the delay and should be responsible for the risk.
Unless the contract expressly allocates risk for concurrent delays, courts and arbitrators typically rule the owner-caused delay governs, resulting in the contractor being entitled to additional time and compensation for the owner-caused delay, even when the work was already behind schedule. For this reason, to preserve the owner’s rights to recover damages for late completion, owners and their consultants should take appropriate steps to reduce the potential for concurrent, owner-caused delays.
To continue the above hypothetical example, assume the work was 30 days beyond schedule on June 1 and further schedule slippage was anticipated, so the work will be completed 45 days beyond the contract times. The contract includes liquidated damages for late completion. On June 1, the owner ordered changes in other work that was otherwise on schedule. The owner-ordered changes would cause the changed work to be completed 28 days beyond the current contract times. Many owners and design professionals may assume, because the contractor was already going to complete the work 45 days late anyway, no extension of the contract times or additional compensation for delay costs is necessary for the changed work. The owner and design professional assume the changed work will require a change in price only for the value of the changed work itself.
In our example, absent a contract clause to the contrary, the contractor will likely contend, and a court or an arbitrator would likely agree, the contractor is due a 28-day time extension plus 28 days’ delay costs, and the value of the changed work itself. The contractor would likely be responsible for the remaining 17 days of delay until all the work is completed. Thus, the contractor is likely to not only be compensated for 28 days of delay costs, but the owner will also be entitled to only 17, rather than 45, days of liquidated damages. This is perhaps an over-simplified example and various facts and contract clauses would influence the outcome of a similar situation on an actual project.
To this writer’s knowledge, among the standard construction contracts in widespread use in the United States, only EJCDC C-700—2018, Paragraph 4.05.D.2, expressly addresses concurrent delays, as follows:
“2. Contractor shall not be entitled to an adjustment in Contract Price for any delay, disruption, or interference if such delay is concurrent with a delay, disruption, or interference caused by or within the control of Contractor. Such a concurrent delay by Contractor shall not preclude an adjustment of Contract Times to which Contractor is otherwise entitled.”
Thus, EJCDC splits the risk of concurrent delays by denying the contractor compensation for the cost of concurrent delays, but providing for additional time for the concurrent delay attributable to the owner. The latter relieves the contractor from liability for liquidated and other damages for late completion for the concurrent delay attributable to the owner.
Contractually precluding the contractor’s right to additional compensation (as indicated in EJCDC C-700—2018 Paragraph 4.05.D.2), or additional contract time, for concurrent delays is a fundamental risk allocation that will likely result in higher prices bid to the owner.
Entitlement in Delay Claims
When submitting a delay claim, the claimant must clearly assert the type of delay and demonstrate how and to the extent that the delay was the opposing party’s responsibility. Such claims must clearly indicate the time extent of the delay and the added costs incurred. The project record and facts surrounding the delay must clearly demonstrate that the delay was outside of the claimant’s contractual responsibility and was, therefore, outside of the claimant’s control.
Delay claims are often contentious and difficult to evaluate, especially when insufficient documentation is available in the project record. As discussed more fully in prior posts on this blog, the claimant must support its claim with clear language and appropriate documentation , submitted in accordance with the contract’s requirements for change proposals and claims, and the entity determining entitlement should be ethical and impartial .
https://www.csiresources.org/blogs/kevin-obeirne-pe-fcsi-ccs-ccca-cdt1/2020/06/16/claims-preparation-claims-should-be-clear-complete?CommunityKey=80c3b4dd-0d3f-4d4e-90f2-3bc6e4135dc2
https://www.csiresources.org/blogs/kevin-obeirne-pe-fcsi-ccs-ccca-cdt1/2020/07/31/partisan-professionals-contractors-deserve-ethical?CommunityKey=80c3b4dd-0d3f-4d4e-90f2-3bc6e4135dc2
In evaluating delay claims, it is essential to identify the cause(s) of the delay and correlate them with the facts surrounding the delay and the contract’s allocation of the risk of delays. When the claimant is contractually entitled to relief, the next step is to determine the appropriate changes in the contract times and compensation, if any. A discussion of the details of evaluating delay claims is, however, beyond the scope of this blog post.
Conclusions
Because delays are one of the most common types of construction change proposals and claims, it is very important for owners, contractors, and construction contract administrators to understand the basic types of delays and the contractual risk allocations of each, and to properly enforce the contract relative to change proposals and claims for delays.
Copyright 2021 by Kevin O’Beirne
The content of this blog post is by the author alone and should not be attributed to any other individual or entity.
Kevin O’Beirne, PE, FCSI, CCS, CCCA is a professional engineer licensed in NY and PA with over 30 years of experience designing and constructing water and wastewater infrastructure for public and private clients. He is the engineering specifications manager for a global engineering and architecture design firm. He is a member of various CSI national committees and is the certification chair of CSI’s Buffalo-Western New York Chapter. He is an ACEC voting delegate in the Engineers Joint Contract Documents Committee (EJCDC) and lives and works in the Buffalo NY area. Kevin O’Beirne’s LinkedIn page .
Kevin O'Beirne, PE, FCSI, CCS, CCCA, CDT 08-02-2021 09:19 AM
David Metzger, FCSI, Member Emeritus, CDT, FAIA, SCIP 07-31-2021 10:36 AM
This was an interesting and informative article.
For delays caused by a subcontractor or supplier, as in the examples you noted, a contractor could claim against the subcontractor for recovery. That would be a private matter between the contractor and their subcontractor, and there would be no reason for the owner or A/E to be involved with such a claim.
The following provisions are from AIA A421 – 2018 Standard Form of Master Agreement Between Contractor and Subcontractor where Work is provided under multiple Work Orders. I haven’t checked, but I’d expect that the corresponding agreement forms from EJCDC, DBIA, and ConsensusDocs have similar provisions.
ARTICLE 8 CLAIMS AND DISPUTES § 8.1 Subject to Section s 8.2 and 8.3, any claim, dispute, or other matter in question arising out of or related to the Subcontract shall be subject to the same dispute resolution provisions as set forth in the Prime Contract.
Article 4 MUTUAL RIGHTS AND RESPONSIBILITIES
The Contractor and Subcontractor shall be mutually bound by the terms of this Master Agreement and, to the extent that the provisions of the Prime Contract apply to this Master Agreement and to the Work of the Subcontractor, the Contractor shall assume toward the Subcontractor all obligations and responsibilities that the Owner, under the Prime Contract, assumes toward the Contractor, and the Subcontractor shall assume toward the Contractor all obligations and responsibilities that the Contractor, under the Prime Contract, assumes toward the Owner and the Architect. The Contractor shall have the benefit of all rights, remedies, and redress against the Subcontractor that the Owner, under the Prime Contract, has against the Contractor, and the Subcontractor shall have the benefit of all rights, remedies, and redress against the Contractor that the Contractor, under the Prime Contract, has against the Owner, insofar as applicable to this Master Agreement.
Contact Us:
1-800-689-2900 M - F 8 a.m. - 8 p.m. ET [email protected]
CONSTRUCT Specifier Magazine Conduct Policy Terms & Conditions Return & Refund Policy Sitemap © 2024 Construction Specifications Institute
High interest rates take growing toll as planned apartments, wind farms, shops are scrapped

Three years ago, when a local developer hatched plans for a 352-unit apartment building in West Philadelphia, the project was a no-brainer.
The city needed tens of thousands of affordable and reasonably priced housing units. Construction costs were a relative bargain since the structure would be built in pieces at a factory and assembled on-site. And interest rates were at historic lows.
Since then, Philadelphia’s housing crisis has grown more dire. But after pandemic-related material and labor shortages raised construction costs and the Federal Reserve’s flurry of interest rate hikes in 2022 and 2023 pushed borrowing costs to 23-year highs, the developer of the West Philly building scrapped the project.
Total costs had ballooned from $103 million to $131 million, according to Leo Addimando , managing partner of the developer, Alterra Properties , which announced last August that it was canceling the six-story apartment project.
“The final blow was definitely the spike in interest rates,” Addimando says. “Even if you gave me the property for free, we still couldn’t make the math work.”
High interest rates are compounding the effects of spiraling construction costs and forcing developers to scrap, significantly delay or shelve a growing share of projects across the U.S.
Among those affected are apartment buildings, renewable energy projects, shopping centers, mixed-use developments and office complexes.
The trend is making it more challenging for the nation to address a severe shortage of affordable housing , meet renewable energy goals and revitalize downtowns hobbled by the pandemic with new shops and restaurants, critics and some economists say.
What percentage of construction projects are late?
In December, nearly 30% of private and public construction projects had been significantly delayed, indefinitely stalled or scuttled over the previous six months, according to an American Institute of Architects’ member survey . That’s up from 22% in December 2022 and 15% in September 2019, before the pandemic upended the economy, AIA says. Those percentages are based on the projects' dollar value .
A relatively modest 4% of projects were outright ditched over those six months, the AIA survey said. But cancellations accelerated in the first quarter of 2024, according to ConstructConnect, a research firm. Such abandonments were up 70% for private projects compared with the same period in 2021 and 50% for public projects, the firm’s data shows.
And some delayed projects likely will be dropped eventually, says Anirban Basu, chief economist of Associated Builders and Contractors, a trade group.
Is the US economy strong right now?
Although the rash of developments axed or shelved doesn’t come close to levels reached during the Great Recession and real estate crisis of 2007-09, it’s unusual because the economy remains vibrant , Basu says. The U.S., for example, needs 4.3 million new apartments by 2035, but multifamily construction fell 14% in 2023 and is projected to decline another 20% this year, according to the National Multifamily Housing Council and the National Association of Home Builders.
And though the office vacancy rate hovers at an elevated 22% as more Americans work from home, demand is healthy for retail space, with a vacancy rate of just 4.1% in the first quarter, according to research firm JLL.
What is the renewable energy goal for the US?
Some Democratic lawmakers are especially concerned about the threat that high rates pose to multibillion-dollar green energy projects designed to mitigate the effects of climate change.
“Your decision to rapidly raise interest rates beginning in 2022, and the potential that they may remain too high for too long, has halted advances in deploying renewable energy technologies and delayed significant climate and economic benefits,” Sens. Elizabeth Warren of Massachusetts and Sheldon Whitehouse of Rhode Island wrote in a March 19 letter to Fed Chair Jerome Powell in March.
Asked about the letter the next day, at a news conference after a Fed meeting, Powell said, “Our mandate is for maximum employment and price stability and the other things that we do, and that’s what we’re trying to accomplish.
“That’s how we can best serve the public and leave the other issues, which in many cases are incredibly important, such as those you mentioned, leave those to the people who have responsibility for those.”
What will using higher interest rates do?
By rapidly hiking rates , Powell and other Fed officials have been credited with helping lower inflation from a 40-year high of 9.1% in mid-2022 to 3.5% in March 2024, based on the consumer price index (CPI). But there’s a delicate push-and-pull to its strategy, which aims to cool the economy and inflation by curtailing consumer and business demand.
Yet higher borrowing costs also crimp the private sector's ability to build housing and add other new products to the market. And that supply crunch can juice inflation.When developers cancel planned apartments, for example, landlords feel less pressure to keep rents stable so they don’t lose tenants to the new units. Rent has been the biggest inflation driver, contributing more than 30% to the COVID-induced run-up in prices, according to the CPI.
Interest rates aren’t the whole story.
How much have construction costs increased?
Hefty construction price tags pose an even bigger burden. But after climbing about 37% from 2021 to early 2023, those costs largely have stabilized and then dipped, notes Michael Guckes, senior economist of ConstructConnect.
Meanwhile, though, the Fed sharply raised its key interest rate from near zero to about 5.3% through last July, where it has held. From 2021 to early 2023, commercial construction financing costs more than doubled and have been volatile over the past year, ConstructConnect figures show.
“That scared the hell out of the market,” says Brett McMahon, CEO of Miller & Long, a construction company based in Bethesda, Maryland. “The uncertainty is just causing everybody to pause.”
He estimates that about one-third of the projects his firm is bidding on have been delayed as developers try to reduce costs or scale back blueprints.
When can we expect the Fed to lower interest rates?
As recently as March, the Fed tentatively planned to trim its key interest rate three times this year as inflation slowed. But in recent weeks, with progress on inflation stalling, Powell and other Fed officials have said rates are likely to stay higher for longer.
Developers are taking the shifting signals to heart. The Fed’s recent statements about the dimming prospects for rate cuts likely have led some companies to withdraw their proposals, Guckes says.
“I am concerned that potential owners and developers are becoming more pessimistic ... especially with the chances of 2024 interest rate cuts seemingly slipping away,” Guckes says.
As its costs spiraled higher in 2022 and 2023, Alterra, the developer of the Philadelphia apartment building, asked the current owner of the property to delay the land sale in the hope that rates would fall and to lower the purchase price.
“Ultimately, we could not come to any sort of agreement,” Addimando says. The interest rate that Alterra would have paid for a construction loan soared to nearly 10% from 5% in 2021, he adds.
Alterra, in turn, hiked its proposed rent 9.4%, from $3.50 a square foot to $3.83, putting a one-bedroom apartment at about $2,000 a month, Addimando says. But that wasn’t enough to offset the higher costs. And boosting rent a total of 15% to cover the increased expenses would have made the units pricier than rival apartment buildings a couple of blocks away that are in more residential neighborhoods and closer to area universities, he says.
By ditching the project, the company lost $2 million in preconstruction costs, Addimando says.
Not going to work out
In San Antonio, Texas, VIA Metropolitan Transit, the local transit authority, and DreamOn, a developer, scrapped plans to convert an old industrial building into about 110 apartments, including about half for lower-income residents, as well as shops, offices and self-storage space.
The $66.5 million development would have revitalized a distressed area between downtown and the West Side, DreamOn President Julissa Carielo said in a statement to the San Antonio Express-News .
With the rise in construction costs and interest rates, “It didn’t seem to (work) out anymore,” VIA CEO Jeff Arndt said in an interview with USA TODAY.
Why are offshore wind projects struggling?
Escalating costs also have doomed several renewable energy projects designed to lower greenhouse gas emissions. In the past year or so, developers have backed out of three planned offshore wind farms in Massachusetts and Connecticut, and two in New Jersey.
The two, multibillion-dollar, New Jersey projects would have powered more than 1 million homes, according to its Danish developer, Orsted.
“The significant adverse developments from supply chain challenges, leading to delays in the project schedule, and rising interest rates have led us to this decision,” Orsted CEO Mads Nipper said in a statement.
Total construction and financing costs shot up 30% to 50%. Also, the vessel that Orsted contracted to build the wind turbines in the Atlantic Ocean was significantly delayed, as were certain turbine parts. Orsted had little choice but to drop the project, which would not have yielded a profit for the company, says Maddy Urbish, head of Orsted's U.S. public relations.
New Jersey Gov. Phil Murphy called the decision “outrageous” and said it “calls into question the company’s credibility and competence.”
Yet Orsted isn’t alone. Avangrid, a Spanish energy company, ditched the offshore wind projects in Massachusetts and Connecticut for similar reasons.
The scrapped plans are jeopardizing various state goals requiring that 40% to 70% of electricity come from renewable energy by 2030 as well as President Biden’s target of deploying 30 megawatts of offshore wind capacity nationally in a similar timeframe.
“It’s a tremendous challenge,” Dan Dolan, president of the New England Power Generators Association, says of the cancellations.
Developers recently submitted new bids for the New England wind farms but it’s not clear if they’ll face similar obstacles, he says.
Orsted, meanwhile, is still moving forward with offshore wind farms near Rhode Island and Long Island, New York. The New York project was also saddled with high construction and borrowing costs. But Orsted won the contract after the state allowed developers to submit new bids so they could receive a higher price for power from ratepayers to offset the costs, Urbish says.
Some builders are putting off projects and hoping interest rates will soon fall.
'Dramatically more expensive' to get construction loan
In Boston, Hudson Group recently was granted another year by the local zoning board to start building a 22-story, 115-unit apartment building near South Station. By then, the company hopes borrowing costs will have declined somewhat, says Noam Ron, a partner in the company.
"Interest rates are at the point where these projects aren't sustainable," Ron says.
Instead of earning at least a 6% to 7% return on the development, the project could yield 5% or less, undermining its financial viability, Ron says. As a result, virtually no lenders are financing large residential buildings in Boston, he says.
"I think it's going to take time for rates to come down but we hope they do," Ron says.
Meanwhile, he says, Boston grapples with a severe housing shortage. For residents, "It means rent is really expensive."
Other developers are seeking variances from local officials to cope with higher costs.
In Concord, New Hampshire, Mark Ciborowski wants to covert a former CVS pharmacy downtown into a seven-story complex of apartments, shops and a rooftop restaurant, according to the New Hampshire Union-Leader .
Strike hits Apple Apple Store workers in Maryland vote to authorize strike
But the local zoning board denied his request to build the structure 88 feet high so he could include four floors of apartments to make the project financially viable. That exceeded the city’s 80-foot limit and violated a rule by partially blocking views of the State House from a nearby highway. Ciborowski recently asked the City Council to ease its height limit.
“I am really working hard to make the project work between construction costs and interest rates,” he told the zoning board, according to the Union-Leader.
Ciborowski didn’t return messages seeking comment.
What were the CPI report results?
Wednesday's report on the April consumer price index, a broad inflation gauge, bolstered hopes that the Fed could cut interest rates at least modestly this year.
Annual inflation overall ticked down from 3.5% to 3.4% and a core measure that excludes volatile food and energy items slowed from 3.8% to 3.6%, the lowest in three years.
Several economists said the data led them to maintain their forecasts for an initial rate cut in September.
Delays in the construction industry: Our 2022 survey results and how they compare to 2016
Posted on 3/01/2023 at 12:56 PM by Jim Burns in Blog
From the pandemic to Brexit, the construction industry has faced countless challenges in the last six years. Whether it’s supply chain battles, budget inaccuracies or labour issues, these challenges often lead to significant delays on projects across the UK.
But that’s not to say these hurdles didn’t exist before – in 2016, we asked construction professionals to complete a survey about their experiences of delays in major construction projects. The survey found delays impacted over 85% of those in the construction industry, leading to additional build costs and longer delivery times.
Of course, a lot has happened since 2016 and we thought it was time to re-assess whether delays are still causing issues.
So, we sent out our survey again this year , and almost 80% of respondents said construction delays have changed in the last few years. Consultants, designers, principal contractors and sub-contractors all answered our survey on their experience in the current climate. We wanted to know about the cost implications, extended deadlines and whether delays are having a bigger impact now than back in 2016.
In this post, we will be comparing our findings from 2016 and 2022 to find out how delays in the construction industry have changed.
Respondents reported more projects under delay in 2022
A whopping 91% of those who responded in 2022 said that, in the last few years, they had been involved in a project that had experienced delays. In the last few years, an increase of 6 percentage points compared to 2016.What could be causing this?
With the demand for new homes and other buildings continuing to rise, it is stating the obvious to say that there simply aren’t enough construction workers to meet this high demand. Since the UK left the EU there has been an overall shortage of skilled labour leading to widespread recruitment difficulties. This has resulted in fewer projects being completed on time, as contractors struggle to source materials and labour.
In addition, the UK government has recently announced plans to tighten construction regulations and increase scrutiny of building projects, resulting in further delays for contractors who need to comply with these new rules. As a result, more contractors are facing long delays when it comes to completing their projects.

How do these results compare to 2016?
We asked, “What % of projects, in general, do you estimate are subject to a delay?”

In 2016, the vast majority of respondents said that less than 30% of projects experienced delays.
Worryingly, 28% of respondents in 2022, estimated that more than 50% of construction projects now experience delays of one kind or another, compared to just 15% in 2016.
These figures illustrate a shocking increase in the percentage of construction projects being delayed and in recent years, leading to higher costs and longer timelines across the UK.
Are delay periods getting longer?
Our survey tried to identify what the average amount of time that delays adds to construction projects. The question asked: Thinking of the last delayed project you have been involved with: What would you estimate the delay to be (as a % of the original estimated delivery time)?
In 2016, the most popular answer to the question was “less than 10%” with 28% of respondents choosing that answer.
In 2022, the most popular answer was 21-30% with 27% choosing this answer.
Most notably, in 2022 those answering less than 10% had dropped to only 11%.

Also, those answering that their last project had been delayed by between 21-50% had significantly increased.
Reasons for this could include the fact that projects are becoming increasingly more complex and expensive, resulting in a longer delivery time.
There has also been an increase in demand for quality materials, which means that suppliers are taking longer to supply.
In general, 2016 saw the most delays adding just under 10% of the original estimated delivery time to a project. In 2022, far more projects are experiencing longer delays that are likely to have larger cost implications.
All of these factors contribute to an overall increase in construction project delays, making it difficult for contractors to meet clients’ expectations and make a profit.
Did delays cost companies more or less six years ago?
In 2016, we asked, what would you estimate the additional cost due to delays to be? The most popular answer was less than 10%, with 31% of responders choosing that answer. By 2022 this had reduced to 26%, now sharing the top answer with 21-31% which also had 26% of the vote.

At the top end of the spectrum, we saw a 20 percentage point increase in the number of responders estimating delays to be adding more than 20% to the cost of the project. This increased from 27.7% in 2016 to 47.56% in 2022.
Furthermore, in 2022, 5% of survey respondents said their last delayed project cost over 50% more due to delays, compared to just 3% of respondents six years ago. As expected, delays are having a greater impact on build costs in 2022 than they did in 2016.
Rising prices, particularly in common building materials and labour, have been a significant factor in the overall cost of building projects. Similarly, delays from weather and other unforeseen issues can cause contractors to miss deadlines, which become more costly when they take longer to resolve.
What are the particular reasons for construction delays in 2022?
We’ve established there are more projects and professionals experiencing delays in the construction industry now, compared to six years ago. But why is this happening and what can we do about it?
We asked respondents to choose their top three reasons for delays and weighted their answers to create the following graph.

A look at each in more detail….
Poor original planning and unrealistic scheduling.
In 2022, 31.4% of respondents said poor original planning and unrealistic scheduling were the number one reason for construction delays. Down only 2 percentage points from 2016 but still the number one reason for delays.
This is likely because some contractors failed to properly consider the project scope, budget, timeline and resources needed before they began work.
As a result, they often fell behind schedule or ran out of money before completing their tasks. Additionally, many contractors set unreasonably optimistic timelines and deadlines, ignoring the fact that it can be difficult to predict exactly how long a project will take.
Unfortunately, this lack of foresight led to many projects being delayed or even abandoned due to financial constraints. Fortunately, proper planning and realistic scheduling can help prevent these issues from occurring in the future. By ensuring that contractors consider all the relevant factors before beginning work, delays can be avoided and projects completed on time.
Resource availability (Labour and Supplies)
Resource availability came out, overall, as the second most popular reason for delays in 2022, with 20% choosing it as their number one reason and 18% choosing this as their second choice.
This showed the biggest increase compared to 2016, with only 5% of responders choosing labour and supply shortages as a reason for delays back then.
With industries everywhere struggling to keep up with demand in the wake of the pandemic, materials like timber, steel and aluminium can be hard to come by. This means that supply shortages can cause delays that were otherwise unforeseeable or unavoidable.
At the same time, labour is in short supply as skilled construction workers have been laid off or shifted to other industries. This puts additional strain on the construction industry and can lead to delays in projects. In short, resource availability is a major factor causing construction delays today – but was not a prominent cause of delays in 2016.
Lack or delay in information
In 2016, 34% of respondents said a lack or delay in information was the number one reason for construction delays. However, only 16% of respondents agreed that this was the main reason for delays in 2022.
These figures suggest that in 2022 there are more prominent issues that contribute to construction delays, like resource availability and unrealistic scheduling.
Increasingly complex regulations have made it harder for contractors to complete projects on time, as they must devote extra effort to understanding and adhering to updated safety requirements or navigating around changes in the way land and buildings can be developed. Investing in staff training or outsourcing these tasks could definitely help to reduce the delays they inevitably cause.
Who took the blame?
Whilst this question is entirely subjective it does shine a light on relationships within the industry and how people very rarely blame themselves for anything.

How can we mitigate delays?
We asked respondents to choose their top two reasons for delays and weighted their answers to create the following graph.

In 2022, 34% of our survey respondents said improved monitoring and regular updates were the best way to mitigate delays.
And 29% chose improved information such as site investigations such as site drawings and plans, before the start of work.
Also, in 2016, 34% of respondents said better scheduling and project management would be their first choice to mitigate delays. This was overtaken in 2022 by Improved monitoring and regular updates with all parties involved.
The best ways of mitigating delays seems to have remained reasonably constant over the last 5 years, with one particular factor standing out.
Both in 2016 and 2022 responders agree that harsher penalties are the least effective way to mitigate delays in the construction industry – with just 4.5% of respondents selecting this method in 2022 and 8% of respondents in 2016.
Let’s take a closer look at the different ways we can mitigate delays in 2022.
Improved information, such as site investigations and drawings
Going into a construction project with as much information as possible can help to make sure work runs smoothly and without delays. Site investigations, such as an analysis of soil conditions and existing infrastructure, can provide valuable insight that helps inform the design process.
Detailed drawings which definitively identify material assortment, locations and sizes can also help everyone be on the same page before any construction begins. By taking the time to research and plan, projects can move forward without worrying that something wasn’t thought of. Investing in quality information helps keep everyone productive and efficient.
Receiving up-to-date information about the whereabouts of buried utilities is also key to a well-managed project.
Improved monitoring and regular updates
In 2022, a quarter of our survey respondents selected improved monitoring and regular updates with all parties involved. When it comes to construction projects, delays can be a major source of frustration for everyone involved. But the good news is that improved monitoring and regular updates between all parties involved can help ensure deadlines are met and keep everything running smoothly.
By regularly tracking progress, communicating any issues as soon as they arise, and keeping stakeholders in the loop with regular updates, everyone can be on the same page and make sure that potential delays are quickly identified and addressed. This kind of proactive approach to communication and coordination can go a long way in helping a project stay on track and within budget.
In conclusion
It is clear that both the number of projects experiencing delays and the cost of these delays are on the increase. It is also evident that most people know the solutions to these issues. The bottom line is that it’s essential for everyone involved in the construction process – from contractors and vendors all the way to clients – to keep communication lines open and to ensure that, where there is a consensus, action is taken to minimise delays to save money now and in the future.
By taking proactive steps such as keeping detailed records, staying up-to-date on regulations, and planning ahead for potential issues, everyone involved can avoid costly delays and get projects done faster than ever before. With effective planning and communication, construction projects can be completed on time and with minimal cost increases. As someone once said, “Prior planning prevents poor performance”.
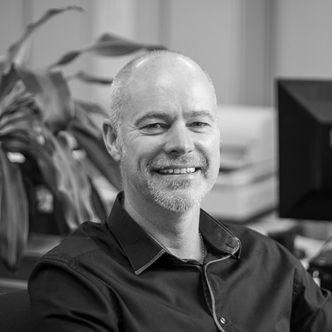
Brought in to help take the business to the next level! His role is to improve lead generation and customer satisfaction from over 7,000 registered clients. Jim loves interacting with potential and existing clients and has a wealth of marketing and sales experience through his previous roles at O2, the RAC and TalkTalk. Jim holds a BA (Hons) Business Studies degree majoring in Marketing. A season ticket holder at Liverpool FC and a keen golfer, Jim also loves the gym!
Leave a Comment Cancel reply
Your email address will not be published. Required fields are marked *
Save my name, email, and website in this browser for the next time I comment.
Sandeep Kashyap
What causes project delay & 6 effective solutions to avoid them
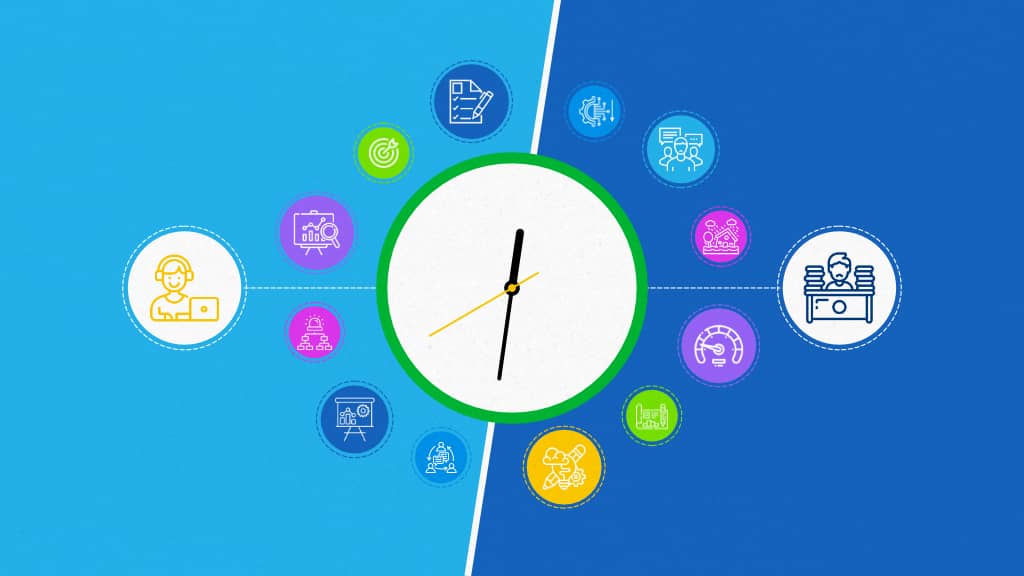
“ One day’s delay is another day’s lack of progress.” – Stuart Bowen
“Delay” is the dreaded word in this fast-paced, dynamic world we live in.
If your projects experience delays more often than not, you’re not alone in this struggle.
The PMI Pulse of the Profession survey found that nearly 43% of completed projects exceeded the original budget and 48% missed the initial deadline.
Project delays are known to give headaches to even the most efficient project managers and their teams, let alone those who are new to this industry. Plans are made to ensure hassle-free project execution, but roadblocks and failure happen and derail projects from the track.
What causes project delays and how to deal with them effectively?
This post will answer all your questions to help you consistently deliver projects on time.
Let’s start with a basic understanding of what is a project delay.
What is project delay?
Project delays mean any delays in the commencement or continuation of a project due to several factors that can cause companies to miss deadlines, exceed the actual allocated budget and even derail projects. Unexpected project delays are usually uncontrollable extend the overall project duration and necessitate a hike in project costs.
Impact of the delay of projects
Project delays cause cost overruns and reworked timelines. Is that all to it? No, there’s much more to it. Delays in projects result in a multitude of issues, and some of them are not explicit right away. Even a delay of a single day leads to additional costs that were not originally part of the budget.
Your business’s reputation could suffer a setback as well as your equation with your bosses. A delay in the project can negatively affect other projects too as you try to restrain resources needed elsewhere.
So, you can see that the adverse impact of project delays is way more than it appears on the surface.
7 Most common causes of project delay
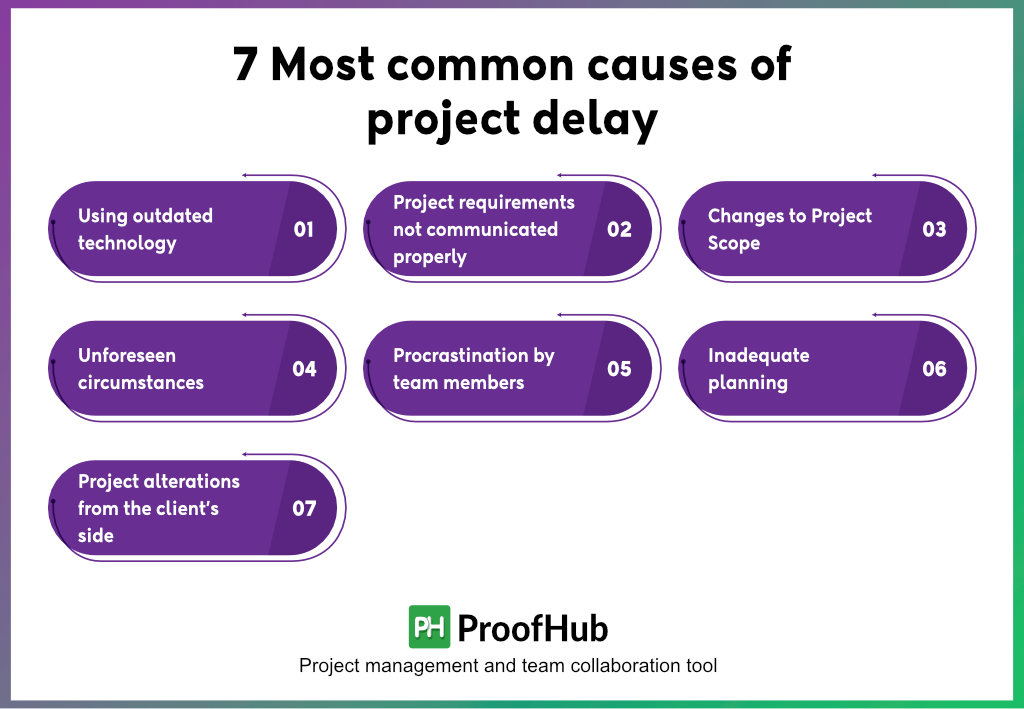
1. Using outdated technology
Using outdated and cumbersome technology is one of the main reasons for project delays. Companies continuing with traditional methods, like manual entries, spreadsheets, long email threads, etc, face various challenges, especially when managing multiple projects and remote teams simultaneously.
Gartner says that Cloud will be the centerpiece of new digital experiences, but many companies have still not realized the importance of cloud-based solutions. As a result, they are losing customers to competitors implementing cloud software.
2. Project requirements not communicated properly
According to David Grossman’s report , the cost of communication barriers stands at $62.4 million per year, per company.
Good communication is the cornerstone of the timely completion of projects, but many teams experience project delays because communication between team members, clients, and other stakeholders is not effective due to many reasons – preconceived judgments, ignorance, not using the right communication tools , distance and time zones, etc.
Vital communication falling through the cracks can obstruct work processes, inevitably causing delays in project completion.
Stay connected with your team through the best employee communication software .
3. Changes to Project Scope
One of the biggest roadblocks to implementing Agile is unclear project scope. The Project scope outlines determining factors such as deliverables, exclusions, assumptions, and constraints. When these factors are unexpectedly changed, a project has to be reviewed, replanned, and usually restarted, and efforts made so far become irrelevant.
Changes in project scope can impact the quality, deadlines, cost, and schedule of a project. This means additional resources ( time, money, human resources ) will be needed as compared to those initially planned and allocated.
4. Unforeseen circumstances
One of the main project delay reasons includes unforeseen circumstances, that are beyond human control. Natural disasters can happen anytime and can cause delays in your project. The same goes for other crucial factors like political or economic climate.
Let us take a look at the example of construction project management, where 39% of projects were halted in the wake of the global pandemic i.e. COVID-19. These delays cannot be avoided and all project stakeholders must accept these.
5. Procrastination by team members
Procrastination by some of the team members is counted among the main culprits for poor performance, which eventually leads to project delays. Some people take longer than expected to complete certain tasks, which further delays the following dependent tasks.
There can be many reasons why people procrastinate – task aversiveness, work stress, anxiety, carelessness, feeling overwhelmed, etc. To avoid procrastination and project delays, businesses should identify people who often fall short of deadlines. Reasons behind their slow work should be identified and corrective action should be taken to ensure your projects do not deviate from track.
6. Inadequate planning
Poor planning and scheduling can result in project delays. If a project is not started right, it would be unrealistic to assume it will end right. Poor planning in project management translates to not laying out a clear timeline and not allocating resources adequately. Vagueness surrounds projects marred by poor planning.
Team members have no clear picture of what is expected of them and there’ll be a sense of dissociation as the project lacks clear goals and direction. This means that project delay is nothing but inevitable.
7. Project alterations from the client’s side
Many times, clients want to make changes to a project that can disrupt its progress. The entire timeline of a project needs to be restructured, which needs a lot of valuable time and other resources.
To avoid sudden alterations to a project, clients should sign off on an elaborate project description before it starts. Doing this helps project teams to execute projects in an organized way whereas unprecedented, last-minute changes from clients bring the project to a sudden halt, further extending its timeline.
Phew! So many reasons for project delays, but the good news is that delayed projects can be brought back by implementing some tried-and-tested ways to avoid them and ensure your projects are completed and delivered on time, thus delighting your clients no end.
Read on to know more about it.
How to avoid delays in projects (6 smart tips)
Alright. We’ve read what causes project delays and there is no reason for you to feel overwhelmed. The good news is that 90% of project delays can be avoided by you by incorporating a few smart strategies in your project management style.
Do you know that most project delays are not caused by working longer on some tasks but by unclear job responsibilities and miscommunication? Yes, it’s true.
So, how to keep your clients happy by avoiding project delays and building on your business’s reputation?
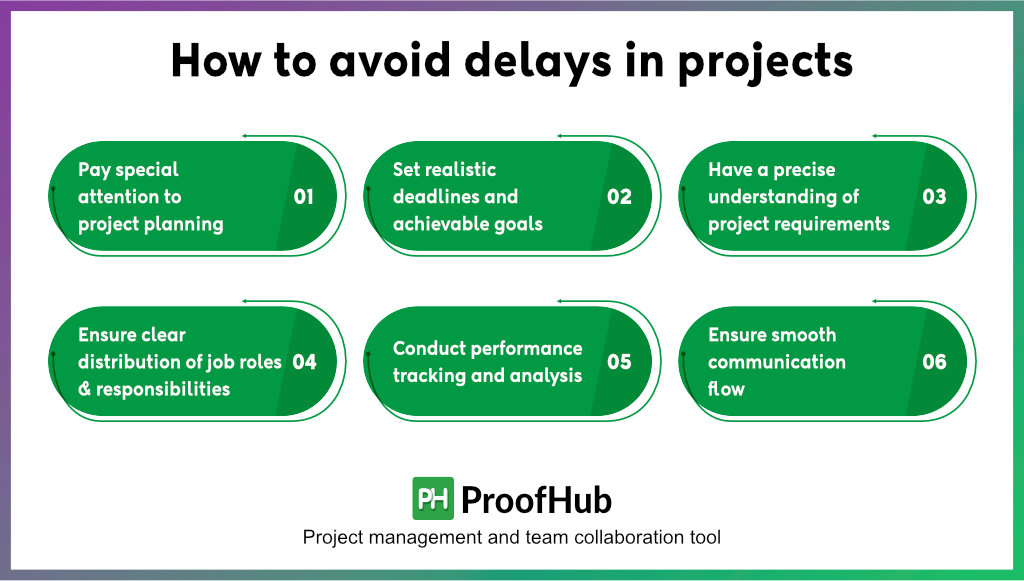
The following strategies have greatly benefitted many teams and businesses ( our organization included ).
1. Pay special attention to project planning
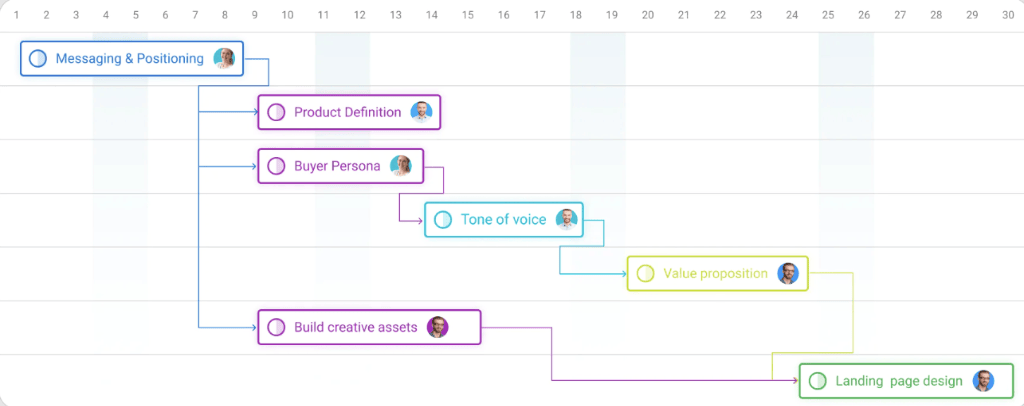
Now, the planning stage is where most project teams get it right, or wrong. This is where project managers need to get their act right to avoid delays in processing and future complications in a project. A well-developed project plan that clearly outlines a certain timeframe defined stages, and designated resources reduces the overall vagueness and risks.
Now, you might as well plan projects with pen and paper, but using a robust PM software like ProofHub can help you successfully plan and schedule projects while keeping things documented and accessible to everyone involved.
Using a reliable and highly functional project management and team collaboration tool can help you to:
- Make a task list of all the tasks required to complete a project
- Assign tasks to the right people
- Define the start and end dates for each task
- Plan work around deadlines and properly allocate resources
- Track tasks’ progress through multiple views – Board, Gantt, and Table view
- Identify potential bottlenecks and resolve them before they cause project delays
- Keep everyone in the loop with a smooth communication flow
- Organize and collaborate on all digital files and documents in a centralized location
Keep a full control on your deadlines using effective project planning software. Now plan smartly & be organized.
2. Set realistic deadlines and achievable goals
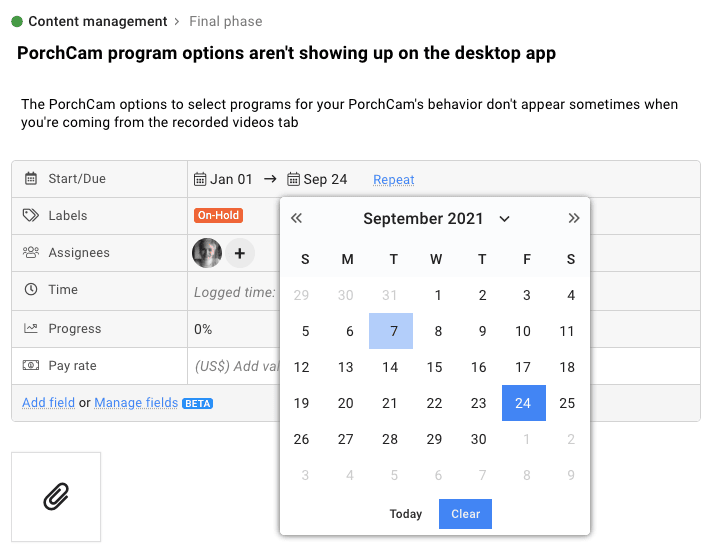
Do you get overly ambitious with your deadlines and goals? It helps to be realistic because even the most productive people have their limits. Sometimes, project managers can set unrealistic deadlines just because they want to impress clients. This blunder stresses out people.
Why overpromise and underdeliver and dent your company’s reputation?
Here’s how to set realistic deadlines for your team members that motivate your team members and not overwhelm and stress them out even before they start to work on their tasks.
- Use ProofHub’s reliable and easy-to-use task management tools to ensure a clear distribution of job roles and responsibilities.
- Analyze the individual productiveness, skills, and experience of your team members and set deadlines accordingly.
- Set time estimates for tasks to define the amount of time it should take to complete a particular task and know when the time taken exceeds the estimated time.
- Categorize and label tasks as urgent, high-priority, and low-priority tasks so assignees can organize and attempt their work accordingly.
- Use a time-tracking tool to keep track of the time spent on different tasks.
3. Have a precise understanding of project requirements
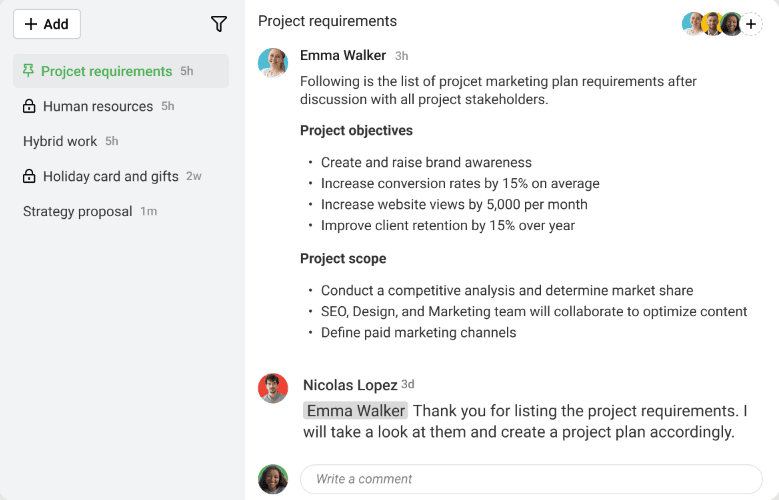
Do you understand project requirements thoroughly to determine the complexity of the project? It is the project complexity that decides the effort and duration of the project. Project managers should remember that unclear or poor understanding results in bad project estimates, which in turn leads to project delays as you’ll be thinking: Oh No! ‘ I’ve badly underestimated this project.’
We don’t want this to happen to you in any case because a bad understanding of your project requirements will likely take your project nowhere before it sinks deep down. Here’s how you can better understand project requirements.
- Perform a requirement analysis before the project flags off
- Invest a considerable amount of time in understanding the requirements to ensure zero gaps in knowledge
- Create a requirement specification document
- Ask the client to sign the requirement specification
4. Ensure clear distribution of job roles & responsibilities
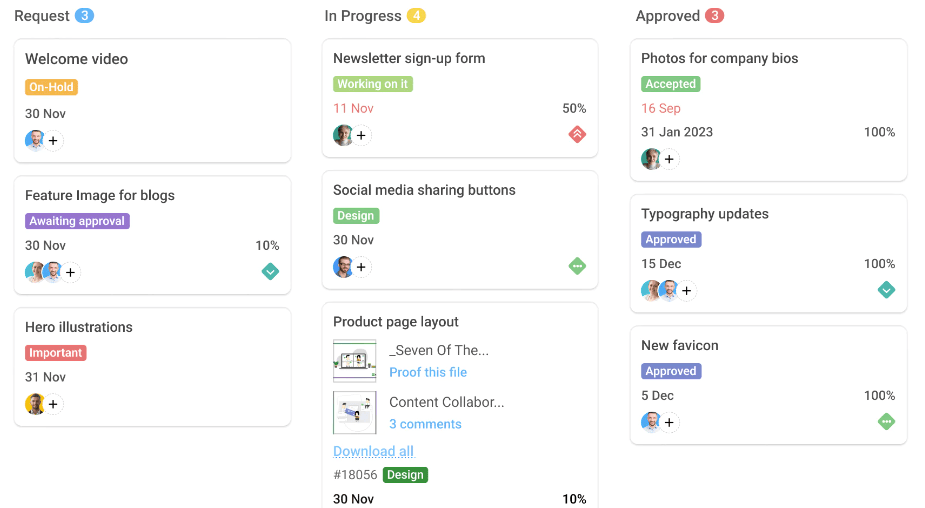
Many times projects are delayed because of confusion surrounding job roles and responsibilities. When people lack clarity on their responsibilities at the workplace, not taking ownership of the tasks at hand is a common scenario.
What will a person do if they are assigned a task that does not match their skillset?
Procrastination, poor quality of work, dragging tasks unnecessarily longer than usual. This is where your project schedule goes completely haywire.
Use a smart task management tool like ProofHub to create, allocate, and track tasks at every stage.
We recommend you implement these additional following tips to ensure everyone knows what’s expected of them.
- Hold a collective team meeting to explain what you expect from each team member.
- Discuss job responsibilities with every person in a one-on-one meeting.
Explore how ProofHub’s task management system can help you managing your resources , Checkout here – Task management system
5. Conduct performance tracking and analysis
If you track tasks within a project at every stage then there’s a little scope for project delays. No, you don’t have to check in with your team members several times a day to see what they are up to. This will make them feel a tad uncomfortable.
Instead, you should use a PM tool like ProofHub that helps you to have a Bird’s eye view of every team member’s assigned tasks. You can see how tasks are progressing and if there are potential hurdles that need to be addressed to make projects stay on track.
You might likely have to shake up some of your team members if they are going slower than expected. While you should trust your team members with their job responsibilities, make sure that people are aware that tasks need to be completed by due dates.
Here’s how to regularly track the performance of your team members .
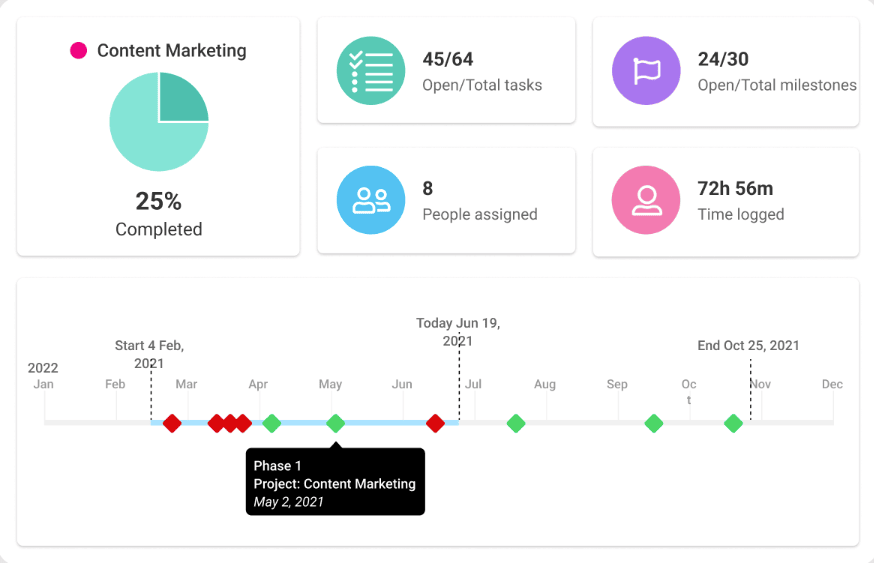
- Track overdue tasks, work-in-progress, and completed tasks for each employee across projects .
- Review work in progress regularly.
- Help employees with self-monitoring tools win inbuilt capabilities such as time tracking , Board view, Table view, and Gantt charts .
6. Ensure smooth communication flow
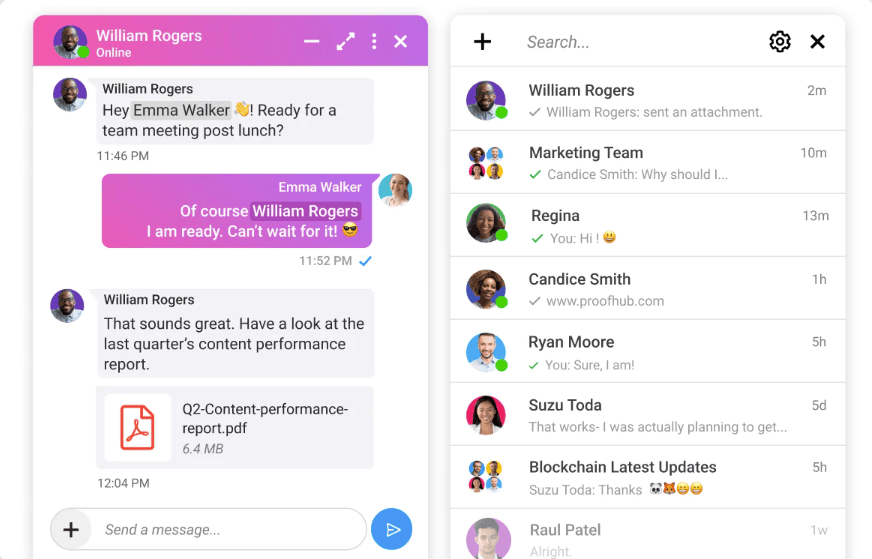
For timely project completion and delivery, the communication between all team members, clients, and stakeholders has to flow smoothly, without vital information falling through the cracks. Stakeholders should be kept in the loop and provided timely, detailed information on the project’s current status, achieved milestones, and team concerns to avoid derailing the project in the long run. Smooth communication helps to keep things transparent as everyone stays updated on all recent developments within the project.
ProofHub has understood this very well and offers an in-built Chat feature that allows quick information exchanges regarding projects. It can be one-on-one or between groups. As a result, there is no risk of critical information being lost, and there is no communication gap as well.
Stakeholders should also be updated on new change requests, the scope of change, and necessary changes to be taken, so they can accommodate change requests without obstructing the project schedule.
Maintaining a seamless flow of information is easy these days as there are various communication tools available – team chat apps , audio, and video conferencing tools, etc.
Project delay examples
Some typical examples of project delays are:
Example 1: A project team member working on a project is assigned a dependent task with a set time estimate of 5 hours. However, the assignee takes 3 hours ( completes the task in 8 hours ) more to complete this task, which results in a further delay in the start of another task by 3 hours. As a result, the delay in completion of one task causes other dependent tasks to be delayed and the entire project schedule has to be reshuffled.
Example 2: Programmers and designers can take much time improving the details of software or design, even when the improvements were not asked for by the client. This can extend the review and approval process, which might cause project delays.
How to manage project delays?
You’ve tried everything in the book to avoid project delays, but even that does not guarantee a 100% hassle-free project completion and delivery. So, what to do when your project has encountered a few roadblocks and it’s likely to be delayed? Read on to know more.
What if project delays still happen?
It’s true that even after meticulous planning and careful execution, some projects still get delayed, and it’s not a new situation for seasoned project managers. So, the question arises – what if project delays happen even after you’ve made every effort in the book to avoid them?
Legitimate questions deserve thoughtful replies. We would recommend not getting overwhelmed by such delays and avoiding making hurried decisions.
Here’s what you can do to mitigate risks caused by project delays.
- Conduct an urgent team meeting and delve deeper into the causes behind the delay while not playing the blame game.
- Deprioritize interdependent tasks if a project deadline is suffering.
- If a project gets delayed due to budgetary issues, pass the issue to board members or other concerned authorities.
- Never back down from taking ownership of your mistakes and don’t hesitate to coordinate with your subordinates.
How to communicate project delays?
When project delays happen, it’s common for managers and their teams to panic and spend significant time identifying reasons and planning corrective actions. However, amid all this, it’s essential to communicate project delays to stakeholders and clients quickly so they are in the loop.
The best part in explaining project delay to them is that they can be a part of the solution you and your team are trying to devise and implement.
Here are some quick tips on how to effectively communicate project delays.
- Let clients/stakeholders know ASAP about the possible delay in the project, without waiting any longer. It’s better to express concern than to keep quiet and cause last-minute chaos.
- Keep a positive attitude when communicating project delays. Don’t look for excuses and play blame games. Instead, focus on potential solutions and focus on the direction your project is moving.
- Provide some context for project delay, but don’t dig deep into it. Prepare a plan on how to get your project back on track and discuss it with your clients as they are least interested in what went wrong and why.
- Be upfront about timeline changes even if the new delivery date is unclear. You can state that the project delivery will likely happen within 1 week or 1 month ( depending on the project type and its timeline ). It sets expectations and avoids further confusion and misunderstanding.
Organize and manage your work with the best project management software for your team .
The final word
Project delays are the last thing you’d want as a project manager as it causes several setbacks for the organization. As mentioned earlier, there’s a solution to every problem and project delays can be avoided too.
We would recommend you have a detailed look at each of the six strategies listed in the article and implement them in your projects ASAP. We believe that the key to avoiding project delays lies in keeping every team member in the loop by bringing the entire team together on a single collaborative platform.
ProofHub helps you have better control over teams and projects as you have a comprehensive view of all tasks and projects. You can sign up for a free 14-day trial to discover the amazing capabilities of this tool.
What causes project delay?
Delays in project completion can happen due to various reasons – poor project planning, procrastination, scope change, last-minute changes from clients, poor communication, etc.
What are the consequences of project delay?
Delayed projects result in cost overrun, time overrun, disagreement between parties, damage to the company’s reputation, and strained relationships between team members.
How to prevent project delays?
Project delays can be avoided by – proper planning and scheduling, smooth communication flow, and clarity to everyone regarding job roles and responsibilities.
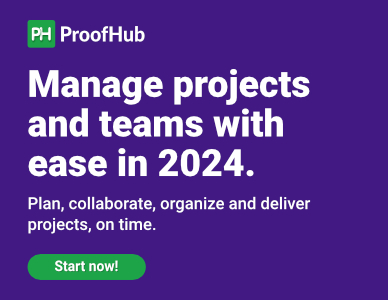
- Share on LinkedIn
- Email this Page
- Share on Facebook
- Share on WhatsApp
Try ProofHub, our powerful project management and team collaboration software, for free !
No per user fee. No credit card required. Cancel anytime.
Project delays are holding back clean power installation, report says
- Medium Text
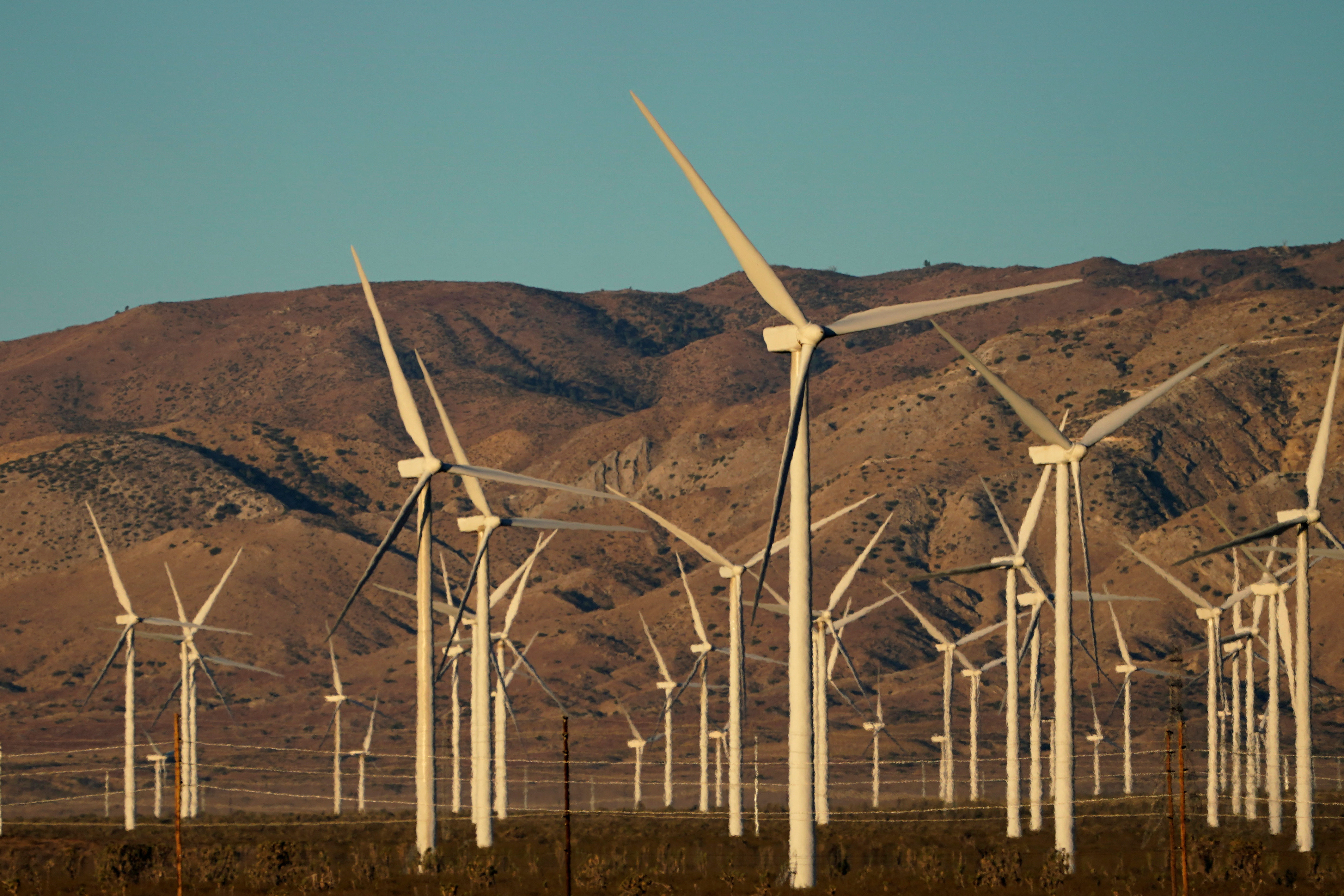
WHY IT'S IMPORTANT
By the numbers.
Sign up here.
Reporting by Vallari Srivastava in Bengaluru; Editing by Tasim Zahid
Our Standards: The Thomson Reuters Trust Principles. New Tab , opens new tab
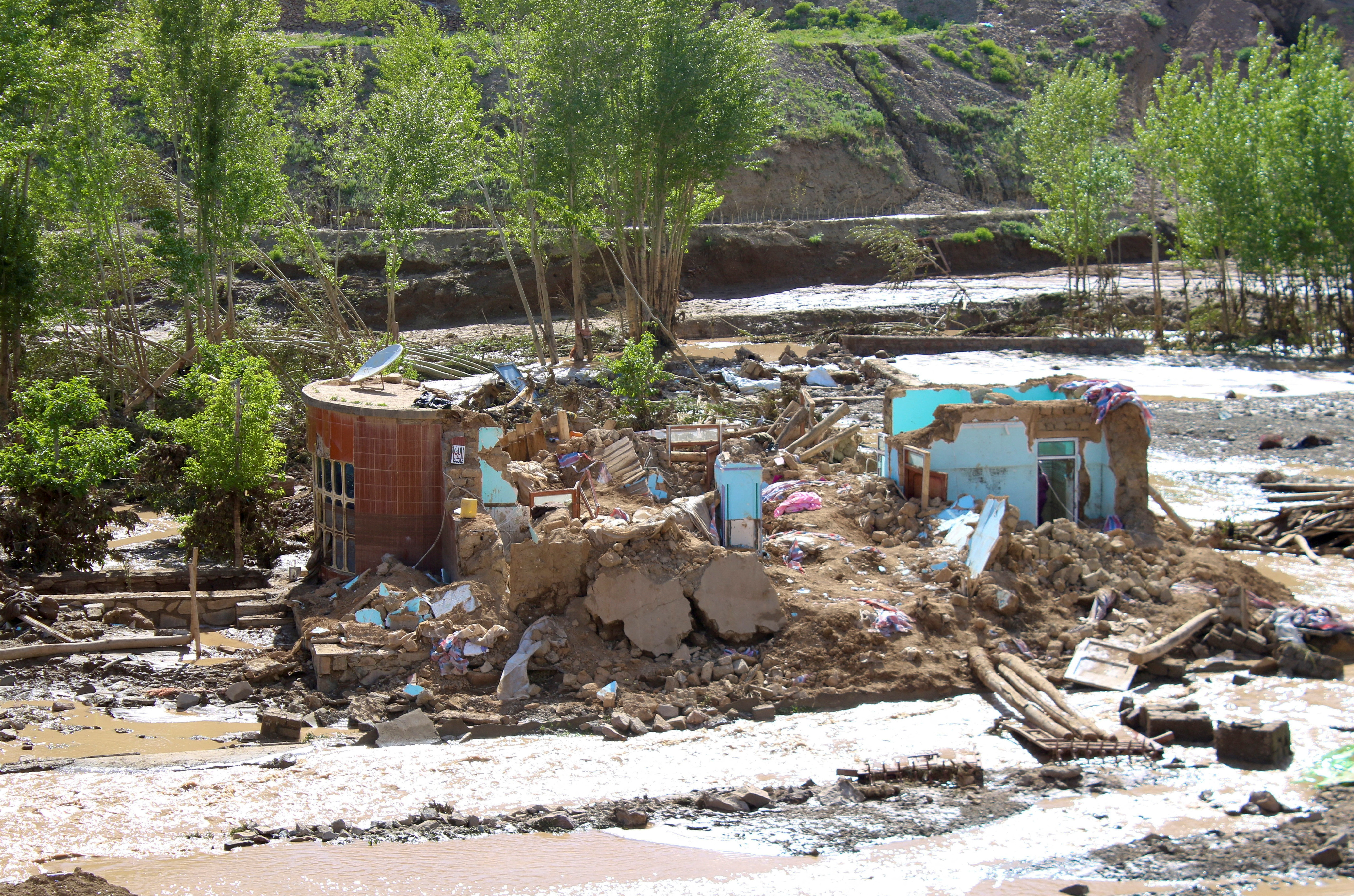
Sustainability Chevron
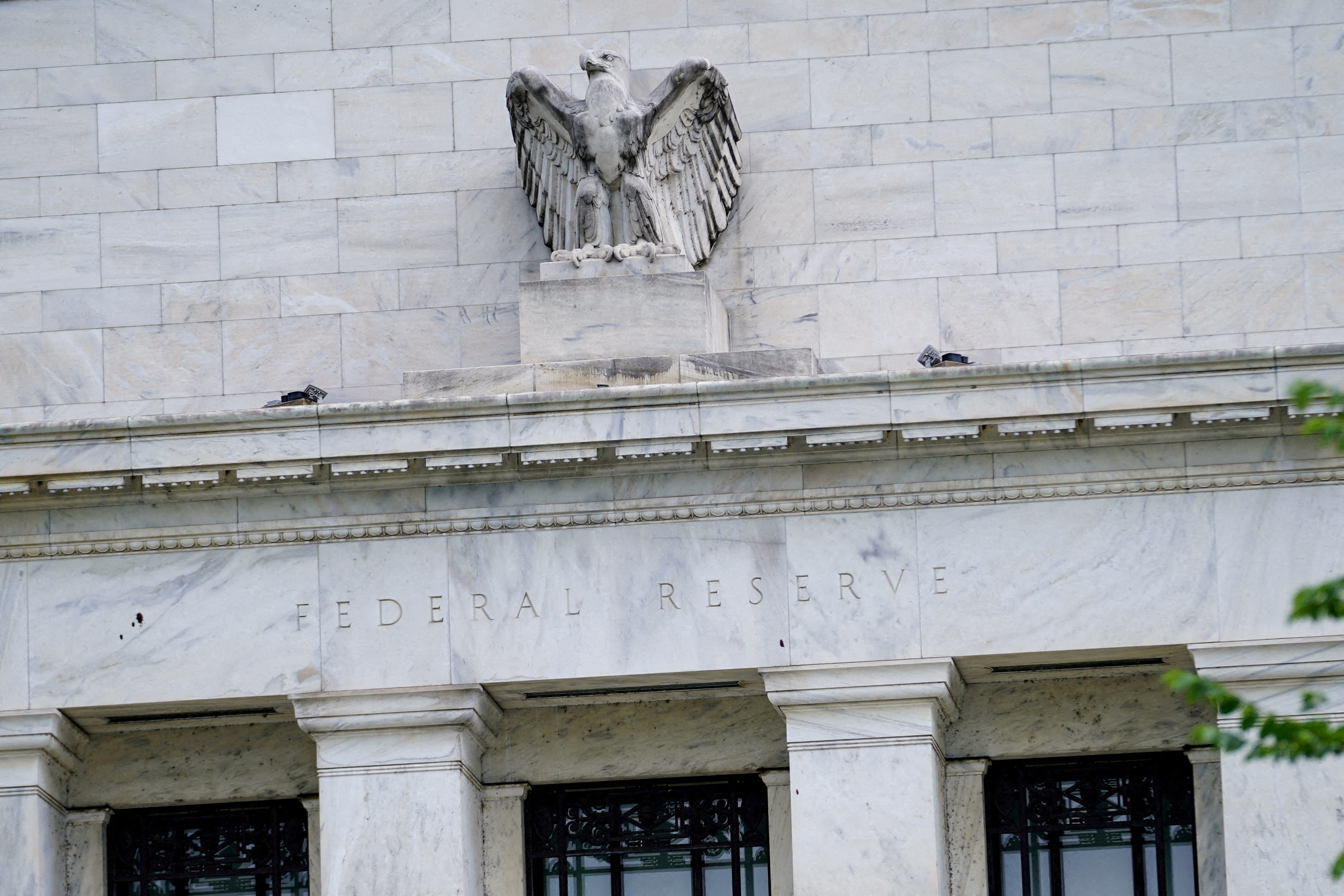
US regulators reconsider capital hike for big banks, WSJ reports
The Federal Reserve and two other U.S. regulators are moving toward a new plan that would significantly reduce a nearly 20% mandated increase in capital for the country's biggest banks following lobbying efforts by industry CEOs like JPMorgan Chase's Jamie Dimon, the Wall Street Journal reported on Sunday.
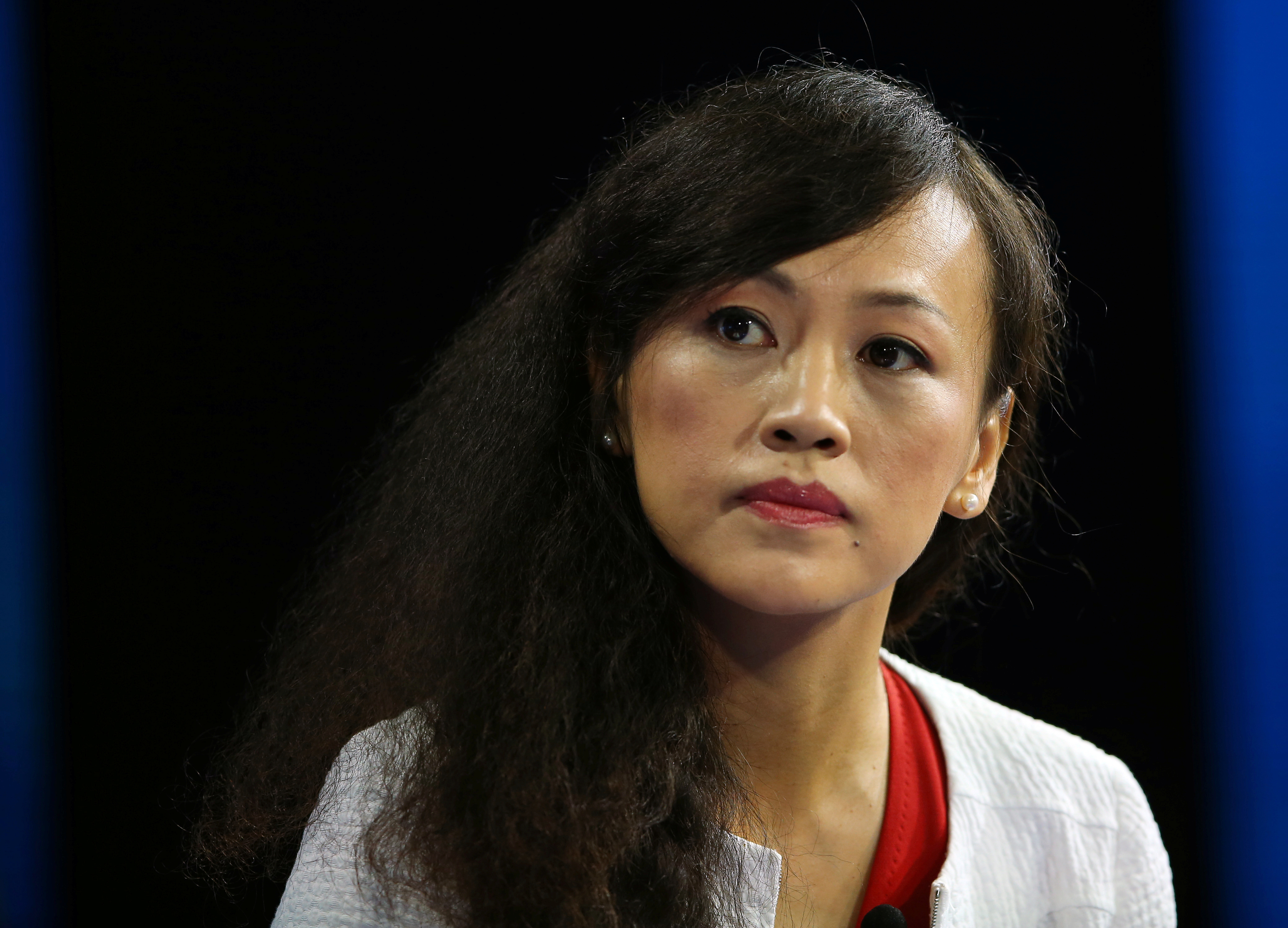
'So about that traffic': Fort Collins tells drivers it knows Harmony construction 'sucks'

The city of Fort Collins feels your pain driving construction-clogged East Harmony Road —and playfully addressed the elephant in the road on social media.
Complaints are common during most road construction projects, but the Harmony Road project has particularly been a pain in the rearview mirror because it's the city's major east-west entrance to Fort Collins.
Friday, the city posted on thread on its Facebook and X accounts assuring agitated drivers that things will get better:
"So about that traffic. If you've driven on or around Harmony Road lately, you've noticed some ... changes.
"We've got a few things to say. Welcome to Harmony Road Work: A Thread.
"The bad news: Construction almost always means delays, and this one is a big project, so we know it's slowing your commute down, and it sucks.
"But we've got some good news, too: Thanks to the amazing weather and our community changing up driving routes, the project is running ahead of schedule!
"Soon you'll have smooth lanes and speedy commutes, but we know it's taken a lot of eye rolling and watch checking."
The city also was open to allowing people to vent on its platforms.
"Still want to complain about your garbage commute? We get it. Whether you thank the crews for their hard work or you hurl language that would make your mother blush, we're always here to listen to your feedback, so fire away."
A drone video with the posts shows lanes with new asphalt and lane markings but also a long line of traffic.
Some of the delays could be reduced if drivers would embrace zipper merging.
When is the Harmony Road projected to be completed?
The city is sticking to its June 7 completion date, though it said on its social media post most of the work will be done by Friday, May 24, which kicks off the Memorial Day weekend.
The city started this $3 million project, which involves 2 miles of Harmony Road from Timberline Road to Strauss Cabin Road, with concrete work in late March.
On April 29, crews began milling the lanes. Milling is a process of removing part of the existing asphalt pavement to prepare for repaving. This process is expected to take around six weeks, according to the city.
At least one lane of traffic will remain open in each direction at all times during construction period. Drivers should expect delays and consider alternate routes.
Typical working hours will be 7 a.m. to 7 p.m. weekdays, but some work may occur outside these times or on the weekends to expedite the project.
Harmony Road project has one last large hurdle before completion
The Harmony Road and Timberline Road intersection is by far the city's busiest with an average daily vehicle count of more than 82,000, according to city data.
The city said it plans to completely close the intersection from the evening of May 31 through June 3.
For more details about the project, visit https://www.fcgov.com/streets/harmonyroadwork .
Construction paused on mega Riverwalk project in Mission Valley
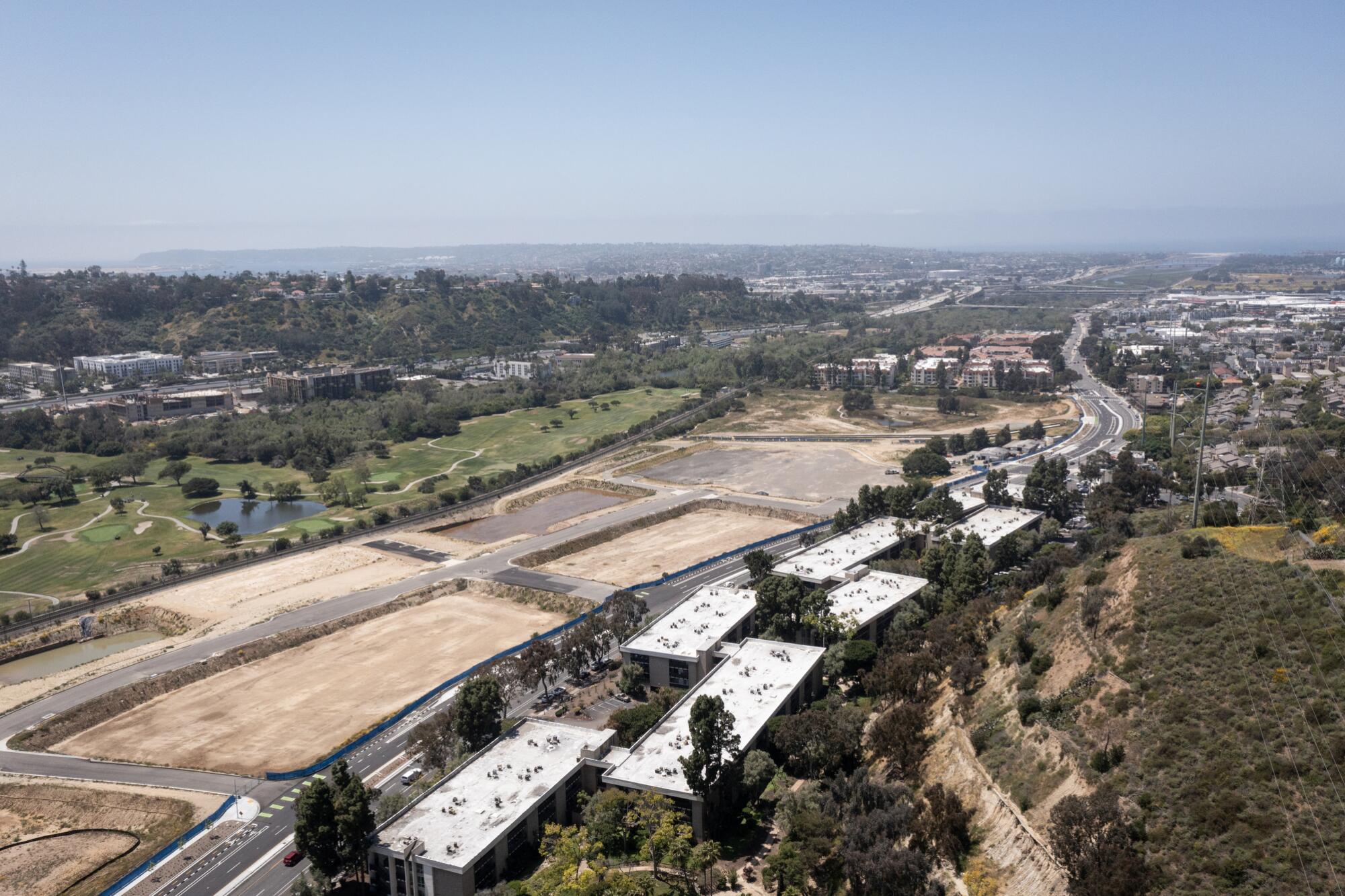
Real estate developer Hines is waiting for market conditions to improve, meaning the project’s first batch of apartments are still more than two years away from being completed
- Show more sharing options
- Copy Link URL Copied!
The cacophony of construction activity at the sprawling Riverwalk project site that follows Friars Road just west of Fashion Valley mall has been replaced with nothingness as the promise of nearly a thousand homes is suspended until market conditions improve.
After completing $90 million worth of infrastructure improvements, including a new bike lane along Friars Road and all of the on-site utility and foundation work, Houston-based real estate investment manager Hines has hit the pause button on its $4 billion mega project.
This story is for subscribers
We offer subscribers exclusive access to our best journalism. Thank you for your support.
Clark Construction, the project’s initial general contractor, has removed all of its equipment from the site, leaving audibly silent — and visibly flat — a construction site that should already be populated with partially completed residential buildings.
With the ground work done, Hines hit a natural demarcation line in the building process and is waiting for more favorable financial conditions before erecting its first structures, the developer said. The developer cited the cost of debt as a result of high interest rates as the main reason for the setback, but said that high construction and supply costs are also to blame.
“When we started this project, we knew that we would face economic cycles, and the partnership was set up for that. And so we find ourselves in a moment where there’s some volatility in the markets, but that’s really a blip on the radar screen,” Hines Managing Director Eric Hepfer told the Union-Tribune. “We’ve got everything lined up. And so when the conditions are right, we will move forward on the vertical side of this.”
The deliberate pause means the project’s first batch of apartments — 937 market-rate units were initially promised for early next year — are still at least two years away from being completed. The developer said that it has also decided to pare back the initial phase to 721 apartments. An additional 216 units will be built shortly after that, the developer said, and the project’s total unit count remains unchanged.
The 195-acre, mixed-use Riverwalk project hails from Hines and longtime land owner the Levi-Cushman family. It will eventually replace the entirety of the Riverwalk Golf Club at 1150 Fashion Valley Road. The partners teamed up on the current plan in 2017. San Diego City Council members signed off on the project in 2020 .
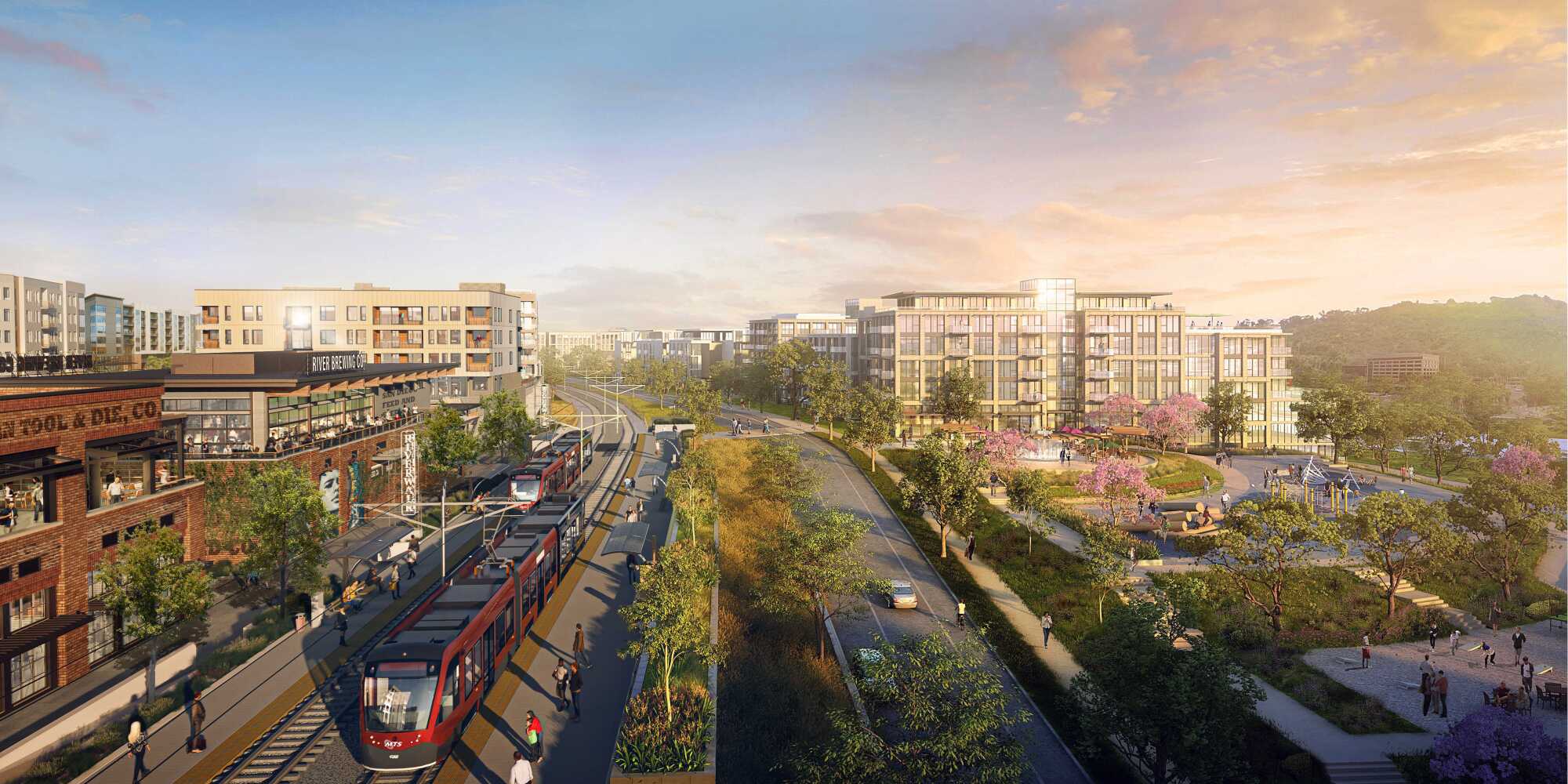
At build-out in 2035, Riverwalk will include 4,300 apartments and condos, 152,000 square feet of retail stores, 1 million square feet of office space and a new trolley stop. The project, which is bisected by the trolley line, will feature a downtown-style main street. And the development plan calls for 97 acres of parks, open space, and trails with bikeways and pedestrian walkways that follow the San Diego River Pathway.
In September 2022, Hines started construction on the initial phase of work on the golf course’s shuttered northern, nine-hole course opposite Friars Road. The first phase of work, which includes half of the project’s retail footprint, is now budgeted at $600 million.
To date, the developer has made good on its promise to improve circulation for cars, bikes and people traveling on Friars Road. Specific off-site improvements include a new traffic signal, landscaped medians, a buffered bike lane and a two-way cycle track on the south side of Friars Road.
And although less visible, new stormwater infrastructure is said to have greatly improved how the site functions.
“We installed all of the stormwater infrastructure early on. And so what that does is it takes all the rainwater off Friars Road that used to flood onto the golf course and diverts it into stormwater basins, which treat that water before it discharges into the river,” said Pete Shearer, who is a director with Hines. “So the issues that other neighborhoods have experienced recently with flooding, we put in that infrastructure to handle that specifically at Riverwalk. We’re handling all of the regional water that’s hitting the roads.”
The developer also raised the former golf course’s elevation to create the project’s roads and building pads, meaning the entire site is now at grade with Friars Road, he said.
But the project’s many homes, heralded by Mayor Todd Gloria and other local dignitaries as key to combating what they often characterize as a housing crisis, will have to wait.
“We have an investor as well as a lender who can proceed on this,” Hepfer said. “It’s really a function of evaluating the market conditions and the right time to move forward.”
Real estate investment firm Affinius Capital (formerly USAA Real Estate) is the equity partner on the project. Hines declined to provide the name of its lender.
The developer’s election to wait is a byproduct of a real estate financing market frozen by high interest rates, said Nathan Moeder, real estate analyst with London Moeder Advisors.
“Right now we’re in a high construction cost environment and a high interest rate environment,” he said. “That’s why a lot of these residential projects are being put on hold. They’re not being developed because I think (developers) are waiting for the Federal Reserve to really signal that they are decreasing rates and that rates are going to be coming down.”
When building financial models for their projects, real estate developers take the income anticipated from the project and divide it by the project’s total costs, and are typically looking for a one-year return on costs, after the project is built and leased, of 6 percent or 6.5 percent, Moeder said. But because interest rates today are 6.5 percent, the annual return would only service the debt, he said.
“The margin is so thin,” Moeder said. “That’s why they’re waiting. There’s too much risk in the market.”
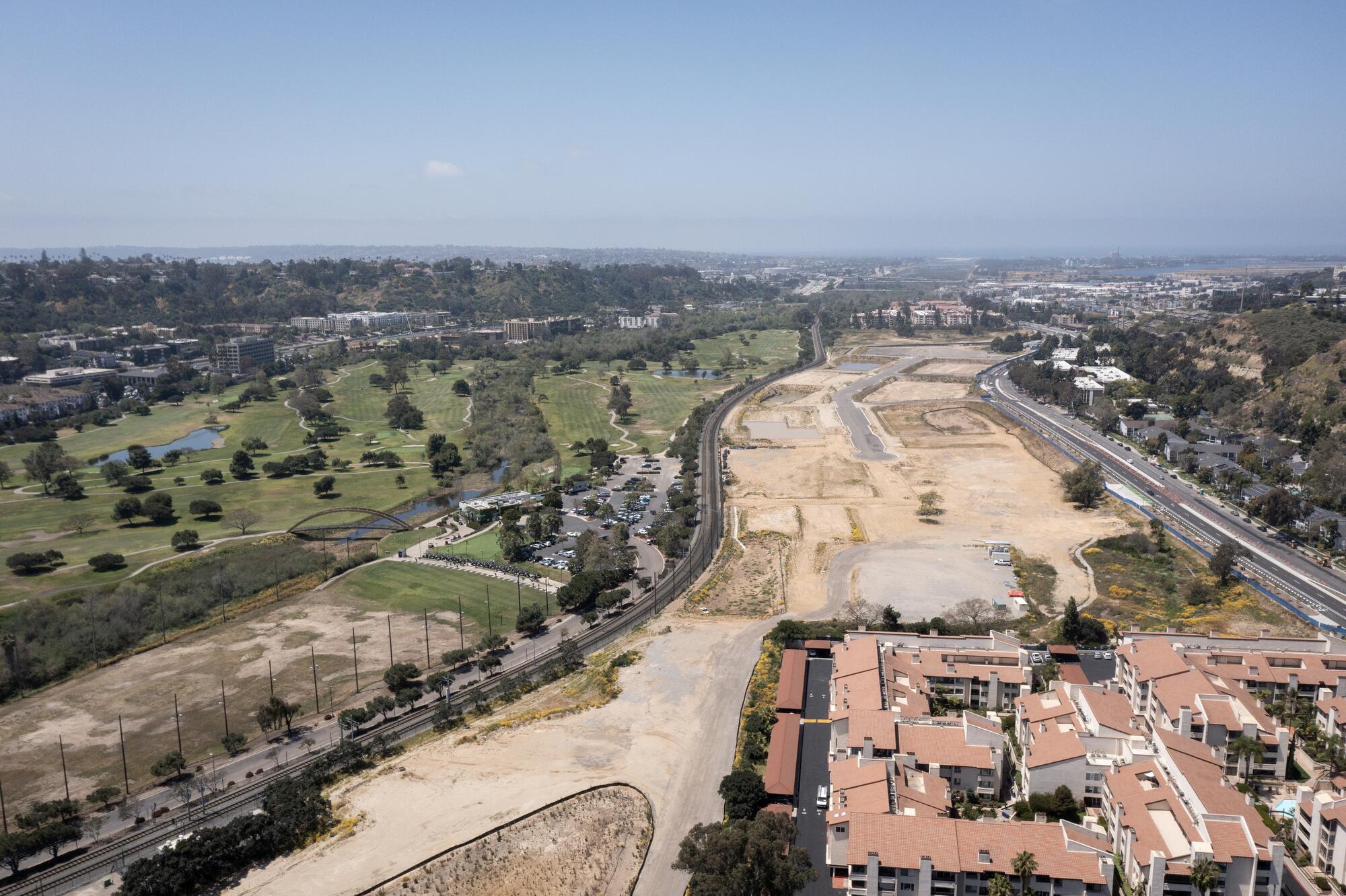
And the problem is not unique to Riverwalk.
“The Fed is trying to slow down the economy and get inflation under control. So that’s why Treasuries are high and interest rates are high and everything is high,” Moeder said. “This could be a long-term problem. If we have longer-term high interest rates, it’s going to be difficult to build because costs are not coming down. And so something will have to be figured out. Otherwise, we’re not going to see a ton of housing.”
Hepfer characterized Riverwalk’s construction hiatus as a “momentary pause.” The developer acknowledged that it could be anywhere from a few months to a year or longer before the developer resumes work.
“We are long-term investors, long-term holders with the partnership with the Cushman-Levi family, and with our capital partner Affinius,” Shearer said. “We hope it’s a short-term blip. ... It could be very soon or it could be longer. It really is dependent on what happens in the larger macro-economic environment.”
The developer is, however, still moving forward with Riverwalk’s first affordable housing project, which will set aside 188 units for low-income families and is on a path independent from the market-rate units. The initial subsidized project is being built in partnership with Wakeland Housing and Development Corporation. The project last year was awarded a $41.1 million grant from a state program and is currently being designed. Construction is expected to start in mid-2025.
Hines is required, as a condition of its agreement with the city, to set aside a total of 430 units for people making 65 percent or less of the area median income.
Get U-T Business in your inbox on Mondays
Get ready for your week with the week’s top business stories from San Diego and California, in your inbox Monday mornings.
You may occasionally receive promotional content from the San Diego Union-Tribune.
Orange barrel season is here: 14 big road projects planned in Metro Detroit

Construction workers are set to extract most of the surface of Southfield Road from 11 Mile to 12 Mile in Lathrup Village and Southfield, repair the road's base and pave two new layers of asphalt.
In Macomb County, crews will rebuild Kelly Road between 14 Mile and 15 Mile in Fraser.
And in the Dearborn area, the Michigan Department of Transportation is resurfacing a section of Southfield Freeway in Wayne County.
These are just a few of the many road projects that are taking place this year in Metro Detroit. From Clinton Township to Commerce Township, more than 100 road projects are planned across Metro Detroit, and road officials urge patience.
Construction season has traditionally started in late March or early April, but over the last few years, the Michigan Department of Transportation has been working on many major projects earlier as winters have been milder, so the season has started in the late winter, said MDOT spokesperson Diane Cross.
Still, summer is prime time for construction, meaning drivers should be prepared for orange barrels, delays and detours.
"We understand that road construction is disruptive, but unfortunately, there's no way to rebuild, repave or reconstruct a road without disrupting traffic," said Craig Bryson, senior communications manager for the Road Commission for Oakland County.
The Macomb Department of Roads has more than 50 projects planned, ranging from road reconstruction to non-motorized pathway projects, said department spokesperson Eric Dimoff. Projects will top more than $100 million. Two examples include reconstructing Garfield Road between 14 Mile and 15 Mile in Fraser and extending Garfield in Macomb Township to 25 Mile.
By contrast, the Road Commission for Oakland County has 57 major road construction projects planned for this year, which will cost nearly $84 million. The agency is reconstructing Brown, Giddings and Silverbell roads from Jamm Road to M-24 in Orion Township and Auburn Hills.
Bryson asked motorists to slow down and stay alert in construction zones. The agency appreciates "the public's patience," he said.
Several major projects are progressing on Metro Detroit's freeways as well. The approximately $269 million Interstate 96 Flex Route project between Kent Lake Road and Interstate 275 in Oakland County is in its final year.
More: 3-year 'Flex Route Project' to begin Monday on I-96 in Oakland County
The project, once completed, will allow motorists to drive on the inside shoulder of eastbound I-96 for a few hours in the morning and the inside shoulder of westbound I-96 for a few hours in the afternoon, which are peak times.
MDOT is widening the inside shoulders of I-96 and making them stronger, so they can handle the weight of the extra traffic. Cross said the project, going in along a stretch of the freeway that sees an average of 88,000 cars a day, will help with congestion.
"The only time 96 is bad is in the morning on the eastbound side, and in the afternoon, the westbound side ― that's when we have the heaviest traffic, the biggest delays, the most crashes," she said.
Below are 14 of the biggest projects this year in Metro Detroit.
Macomb County roads
More than $100 million in infrastructure projects are planned in Macomb County.
Garfield Road will see an extension in one area and reconstruction in another. In the $9 million extension, workers will construct a new road and make other improvements between 23 Mile and 25 Mile. This project will “enhance safety, improve traffic flow, and ease congestion throughout the corridor,” a department news release said.
"That will be definitely a much-needed north-south thoroughfare," said Bryan Santo, the director of Macomb County's Department of Roads.
This is the second phase of the extension project; the first involved extending Garfield from 22 Mile to 23 Mile.
Another portion of Garfield between 14 Mile and 15 Mile in Fraser will be reconstructed, which means the road will be fully rebuilt. In this $5.5 million project, the road will be widened to three lanes, providing for a center left turn lane and deceleration lanes.
Macomb County Department of Roads is also working on two projects on Kelly Road. In one, which costs more than $5.5 million, the road will be reconstructed between 14 Mile and 15 Mile, which is a carryover from the 2023 construction season. In the other project, which costs nearly $1.6 million, Kelly will be rehabilitated between 15 Mile and South Nunneley Road.
The county plans to complete the $220 million Innovate Mound project this year as well. It has already reconstructed the road from Interstate 696 to M-59, but this year, it is replacing the Bear Creek culvert, constructing an 8-foot-wide path between 15 Mile and 18 Mile and doing landscaping work, among other steps. This year's work costs $30 million.
The Michigan Department of Transportation also is resurfacing M-53 , or Van Dyke Freeway, between 18 Mile in Sterling Heights and M-59, or Hall Road, in Utica and repairing bridges along the corridor in an about $16.5 million project.
M-53 southbound between Hall and 18 Mile has been closed since March and will reopen in June. M-53 northbound will close at that time and re-open at the end of fall.
Oakland County roadways
Of the $84 million in major projects that the Road Commission for Oakland County is planning, one of the most prominent is the reconstruction of Brown, Giddings and Silverbell roads. This $15 million project, which stretches from Jamm Road to M-24, will be completed this year. The roads are in the vicinity of General Motors Co.'s Orion Assembly plant , the former Chevrolet Bolt electric vehicle plant being revamped to start producing electric trucks in late 2025.
"One of the issues they had had in the past was that the roads were in such bad shape that General Motors was objecting to bringing their trucks with new vehicles out of the plant on the rough roads there," said Bryson, the road commission's senior communications manager. "We get that. We didn't want them to damage new vehicles."
The commission is also doing a $5.3 million major resurfacing of Southfield Road from 11 Mile to 12 Mile in Lathrup Village and Southfield. Bryson said "major resurfacing" means the agency will remove most of the existing road surface and repair the base. It's more in-depth than a simple resurfacing project.
The agency is also conducting a $5.5 million major resurfacing of Walton Boulevard from Adams Road to Livernois Road in Rochester Hills.
Meanwhile, the $269 million I-96 Flex Route project, which stretches from Kent Lake Road to I-275, is in its last year. All of the traffic has been shifted to the eastbound side of I-96, which has already been rebuilt.
The result of the flex route project is that motorists will be able to use a shoulder as a lane during peak hours. MDOT is doing this instead of adding another permanent lane, which has downsides, according to Cross.
"If you make the shoulder a lane, now you gotta buy more property and build a shoulder, and there's a lot of environmental issues in that, in the sense of there's a lot of wetlands in that area," she said.
MDOT also is in the third year of a $275 million, four-year project to reconstruct I-696 from I-275 to Lahser Road. Traffic has shifted to the eastbound side of I-696 while the agency rebuilds the westbound side.
Wayne County roads
The Michigan Department of Transportation is conducting numerous projects in Wayne County. In a $15.5 million project, it's milling and resurfacing M-39 (Southfield Freeway) from just south of I-94 to Ford Road. The freeway is down to two lanes in each direction, but most weekends this summer, it will be down to one lane.
Cross said the project "has a big impact to the Dearborn area, and we fully acknowledge that."
The agency is also in the first year of a three-year, $139 million project to reconstruct M-14/I-96 between Sheldon Road in Plymouth and Newburgh Road in Livonia. This year, MDOT will mainly do bridge work and widen the shoulders on M-14 so that traffic can be moved onto the shoulders during the next two years.
The agency also is working on a $18.5 million project to replace two bridges and improve four bridges on U.S. 24 (Telegraph Road) from the U.S. 24/I-75 connector to Mercier Avenue, north of Eureka Road, in Taylor. The agency has also closed the northbound direction of the U.S. 24/I-75 connector. The southbound side of the connector will be closed next year.
- Grand Rapids/Muskegon
- Saginaw/Bay City
- All Michigan
Expect traffic delays as Michigan Medicine bridge project advances in Ann Arbor
- Updated: May. 13, 2024, 2:06 p.m. |
- Published: May. 13, 2024, 9:11 a.m.

The East Medical Center Drive bridge over the Amtrak line in front of Michigan Medicine in Ann Arbor on Sept. 21, 2021. Alyte Katilius | The Ann Arbor News
- Lucas Smolcic Larson | [email protected]
ANN ARBOR, MI - A $14-million rehabilitation and widening of an Ann Arbor bridge at the entrance to the University of Michigan’s hospitals is entering a new phase.
Commuters will experience delays and officials recommend they seek alternate routes, if possible.
Beginning Monday, May 20, a new set of restrictions will begin for the second phase of the East Medical Center Drive bridge construction, a hotly-debated project years in the making.
Read more: $14M project to widen Michigan Medicine bridge in Ann Arbor moving forward
Construction crews will shrink the available travel lanes on the bridge, closing the west half of the structure to begin replacing the bridge deck, relocating utilities and making other improvements, city officials said.,
One vehicle lane in each direction on the bridge will remain open throughout the duration of the project, officials said.
However, during the new phase of construction, running through Sept. 6, no northbound East Medical Center Drive left turn will be allowed onto westbound Fuller Road, according to the city. A detour will route traffic right along eastbound Fuller Road to the two Fuller Road left-turn lanes across from the Fuller Park pool.
Southbound Maiden Lane traffic will also not be allowed to turn left onto eastbound Fuller Road, officials said. Traffic will be routed north on Maiden Lane, east on Plymouth Road, south on Murfin Avenue and south on Bonisteel Boulevard back to Fuller Road.
The sidewalk on the west side of the bridge will be closed during the new phase of construction, with pedestrians detoured to the east side.

A map shows a series of closures and traffic restrictions for the second phase of the East Medical Center Drive bridge rehabilitation and widening project in Ann Arbor, near the University of Michigan hospitals. Phase 2 of the project is scheduled to run from Monday, May 20 to Friday, Sept. 6, 2024. City of Ann Arbor
Lane and sidewalk closures are also planned as a result of the project on West Medical Center Drive near the bridge, with traffic maintained, according to the city’s project website and a map of the shutdowns.
Crews will also be building a new East Medical Center Drive dedicated right-turn lane to the Rogel Cancer Center entrance, according to the project summary.
The costs of project, meant to remedy deteriorating conditions on the bridge and also improve traffic flow at the entrance drive to the Michigan Medicine complex, are being shared between the city and the University of Michigan.
A third stage of construction is planned in mid-September, with a fourth coming in December and final work taking place in the spring of 2025, according to the city.
Want more Ann Arbor-area news? Bookmark the local Ann Arbor news page , the Ypsilanti-area news page or sign up for the free “ 3@3 Ann Arbor ” daily newsletter.
More from The Ann Arbor News
- ‘On stolen land.’ Before Ann Arbor was Ann Arbor, it was home to Native Americans
- Knight’s Steakhouse has spent 40 years bringing steaks, comfort to Ann Arbor
- 5 great coffee shops to check out near University of Michigan now that students are gone
- Saline students head to Chelsea’s Robin Hills Farm for 2024 prom
- See how the Michigan Rattler cocktail comes together at Lowertown Bar and Cafe
If you purchase a product or register for an account through a link on our site, we may receive compensation. By using this site, you consent to our User Agreement and agree that your clicks, interactions, and personal information may be collected, recorded, and/or stored by us and social media and other third-party partners in accordance with our Privacy Policy.
Traffic Alert: Construction Projects on U.S. 422 in Montgomery County to Cause Delays
MONTGOMERY COUNTY, PA — The Pennsylvania Department of Transportation (PennDOT) has revealed upcoming construction projects on U.S. 422 in Montgomery County, set to impact traffic flow next week.
Starting May 20 through May 23, drivers can anticipate lane closures and periodic stoppages along westbound and eastbound U.S. 422 for shoulder, roadway, and bridge reconstructions. Controlled blasting activities will lead to intermittent traffic stoppages and paces on specific days, while concrete patching work will necessitate a rolling lane closure on westbound U.S. 422 between interchanges.
“Motorists should prepare for potential backups and delays during their commute,” warned a PennDOT official, emphasizing the need for extra travel time due to the ongoing construction activities.
These initiatives are part of multimillion-dollar projects aimed at enhancing U.S. 422 infrastructure, including pavement rehabilitation, bridge replacements, and overall roadway improvements between key interchanges.
As construction progresses, PennDOT urges drivers to stay informed about the scheduled activities, remain patient, and exercise caution while navigating through the affected areas.
Drivers can check current road conditions by visiting the MyChesCo Traffic Center . Stay updated on the latest news and information from MyChesCo with our free newsletter . Follow MyChesCo on Twitter at twitter.com/MyChesCo and like us on Facebook at facebook.com/MyChesCo .
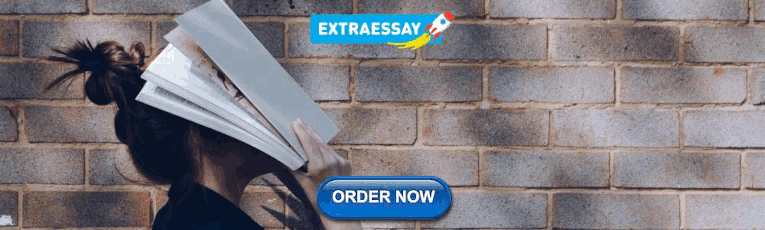
COMMENTS
Construction delays are often result of a mismanaged event/s and can be seen as a risk for the projects, which if identified, analyzed and managed in a systematic process at inception, could be managed, minimized, shared, mitigated or accepted to give some good results and minimize chances of further delay. Delay in construction project has a ...
The results of the study (2021) show that all the identified causes for construction project delays are correlated to 4 main factors (which account for 69.18% of the sample variance): Supply management - 21.41%. Workforce management - 20.79%. Project management - 17.64%. Management of climatic conditions - 9.34%.
A professional writer for more than 10 years, his focus is now on showcasing the benefits of the industry's top connected construction software platform: Trimble Construction One. Construction project delays are caused by budget errors, labor shortages, slow approvals, subcontractor woes & more. Check our tips to keep things on track.
How to Minimize the Effect of Construction Delays. We mentioned it above - every project is different, and so is every delay. Depending on the relationships involved, some fixes may be more appropriate than others when a construction delay occurs. Still, some overarching ideas can help minimize the effect of construction delays. Be realistic
Expected Reasons for Construction Project Delays. In 2022 alone, 91% of construction managers surveyed indicated that they were involved in projects that experienced delays. Most of those delays were related to an unrealistic project plan (31%) and resource issues (19%).
4 Major Causes of Construction Delays. 1. Project Financing. Construction projects are typically financed through commercial construction loans, which pay for the upfront costs associated with the ...
Conceived more than a half century ago, with a construction contract awarded in 2006, that project was supposed to be completed by 2011. Early estimates put the cost at $2.2 billion, then $4.3 ...
1. Change In Project Scope. The scope of work in a construction project defines as the deliverables that are expected at the end of a project. Poor scope definition at the start can be a result of cost overrun and time delay of any construction project. Therefore all the project plans, schedule, cost, and quantity estimation, procurement and ...
The causes of delays on large-scale construction projects are many and varied; changes orders, financial issues, adverse weather, supplier delays, poor design, lack of experience (owner or contractor) or unforeseen ground conditions. These are just a few of the most common causes of delay. However each cause corresponds to a particular type of ...
Use Project Management Software: Tools like ActiveCollab can help with scheduling, task management, communication, and more, making it easier to manage projects and avoid delays. Stakeholder Engagement: Engage stakeholders throughout the project. Their input and feedback can provide valuable insights that can help avoid potential delays.
Spot potential delays early. Many construction project delays can be avoided — or at least minimized. To be able to do this, you need to know how to spot the early warning signs of a project delay. The two most common of these signs include: Unclear or changing project scope: This is a major warning sign of a project delay. It's usually a ...
Construction delays refer to the deviation from the specified time for completing activities as per the contract, resulting in increased costs, potential contract terminations, legal disputes, and other consequences. Mismanaged events typically cause construction delays, posing risks to projects. However, suppose these risks are identified ...
Inadequate project management on the client's side can cause significant delays in the construction process. Poor planning, ineffective communication, and a lack of coordination between different parties can disrupt the project workflow, leading to avoidable delays. Lastly, financial issues also feature prominently in the common causes of ...
Failure to execute a process/activity also causes a delay to the project timeline as it needs more time to redo the work. Implementation failure may be caused by the communication gap, non-skilled/less skilled workers, or resource availability. 10. Use of obsolete project management tools and technologies.
5 tips to minimize the effect of construction delays. Regardless of the type of delay you're dealing with and who's to "blame," a delay needs a resolution. Handling schedule delays correctly can make the difference between minimizing their effect and letting the schedule spiral out of control. 1. Set realistic expectations.
Delays to large-scale construction projects have more than doubled during the Covid-19 pandemic, according to new data released today by nPlan. Research by machine learning startup nPlan found that the median delay for projects completed before the pandemic was approximately 100 days, while pandemic-era projects have a median delay of more than ...
Acceleration may happen on a construction project under three basic scenarios: 1. Voluntary Acceleration. This occurs when the contractor makes up for time lost due to non-excusable critical path delays for which they are responsible. Consequently, voluntary acceleration is rarely the subject of construction claims or disputes as almost all ...
The aim of this paper is to identify the delay factors in construction projects and introduction type of delay analysis techniques for applying more reliable and precise techniques in order to reduce the frequency and to mitigate the severity of disputes and litigation due to delay claims because delays are considered to be a serious problem in ...
The main types of schedule delays on a construction project are: Critical vs. Non-critical. Excusable vs. inexcusable. Compensable vs. non-compensable. The construction agreement will typically contain provisions that describe when these delay claims apply, and the notification process required in the event of a delay.
What You Need to Manage Construction Delays: 1. A Project Plan with your Critical Path. Your project plan will include your project's scope, schedule, and costs. Project plans may also include resource loading and a quality plan. Project Managers use tools like Oracle Primavera P6 or Microsoft Project to create their resource-loaded project ...
By Kevin O'Beirne, PE, FCSI, CCS, CCCA, CDT posted 07-30-2021 10:44 AM. The most common sources of change proposals and claims in construction are likely owner-ordered changes in the work, differing site conditions, and delays. This blog post presents a general overview of delays in construction. Types of Delays.
High interest rates are compounding the effects of spiraling construction costs and forcing developers to scrap, significantly delay or shelve a growing share of projects across the U.S. Among ...
At the top end of the spectrum, we saw a 20 percentage point increase in the number of responders estimating delays to be adding more than 20% to the cost of the project. This increased from 27.7% in 2016 to 47.56% in 2022. Furthermore, in 2022, 5% of survey respondents said their last delayed project cost over 50% more due to delays, compared ...
Vagueness surrounds projects marred by poor planning. Team members have no clear picture of what is expected of them and there'll be a sense of dissociation as the project lacks clear goals and direction. This means that project delay is nothing but inevitable. 7. Project alterations from the client's side.
Only 22% of the clean power capacity delayed in 2023 have been commissioned, the report added. The total combined capacity of projects experiencing delays since 2021 has exceeded 62 GW, with only ...
The city started this $3 million project, which involves 2 miles of Harmony Road from Timberline Road to Strauss Cabin Road, with concrete work in late March. On April 29, crews began milling the ...
As aerial view of the Riverwalk project site, as seen looking west on Tuesday. The developer started construction on the golf course's shuttered northern, nine-hole course facing Friars Road in ...
Still, summer is prime time for construction, meaning drivers should be prepared for orange barrels, delays and detours. "We understand that road construction is disruptive, but unfortunately ...
A map shows a series of closures and traffic restrictions for the second phase of the East Medical Center Drive bridge rehabilitation and widening project in Ann Arbor, near the University of ...
MONTGOMERY COUNTY, PA — The Pennsylvania Department of Transportation (PennDOT) has revealed upcoming construction projects on U.S. 422 in Montgomery County, set to impact traffic flow next week ...